Welding of Metals: Classification, Brief History, Development
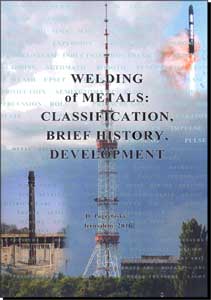
Welding of Metals: Classification, Brief History, Development
380 pp., 250 pictures, a dozen of tables, 205 x 290 mm, hard cover, Jerusalem, Israel. ISBN 978-965-572-159-1
The book price is $175.
In June, 2016 the former staff member of Paton Welding Institute published in Jerusalem a new book Welding of Metals: Classification, Brief History, Development. It gives a lot of information about metal welding processes, including ones not listed in American and European normative documents which the author tries to match to each other. For the purpose of international harmonization, a preliminary attempt was made to provide a unified classification of about 300 welding methods based on the abbreviations that are similar to ones adopted in the American Welding Society. At the same time the book author tried to create the impartial review of historical metal welding developments against a background of general sciences evolution and progress of adjacent processes. Some comparative, economic and other considerations are given too together with a rich illustrative material and large number of references.
The book may be useful for different welding specialists, industrial engineers, designers of precision metal structures and various electro-mechanical devices as well as for students of relevant specialties.
The main purpose of the book is to contribute to general picture of welding development. More than 300 welding methods are mentioned that were developed in the former USSR, modern Ukraine, Russia, USA, Great Britain, Germany, France, Sweden, Japan, Finland, Austria, China, Australia, Brazil, Switzerland and many countries. ESAB, EWI, EWM, Fronius, Hobart, ISF- RWTH, Kemppi, Lincoln, Miller, Phillips and other companies are widely represented.
Orders for book please send to:
POB 31445, Jerusalem 91313, Israelwww.actualweld.com
About the author
David Pogrebisky, who is engaged in welding during 55 years, work as a welder, operator of a large welding robot, foreman, production engineer, manager of E.O. Paton Electric Welding Institute division, lecturer, welding designer, senior staff scientist, has obtained a large experience in various aspects of welding, scientific investigations, welding technologies and equipment. All this permitted him to write the given book.More details (click to open)
Main reasonable suggestions and comments on the book Welding of Metals: Classification, Brief History, Development that would be firstly considered in American (A) & European (E)* Standards (there are given numbers of pages or figures which help to explain the essence of each statement).
Let us analyze this book text from the beginning up to the end, sometimes running ahead or going back, but mainly moving progressively from Chapter 2 to Chapter 20 and choosing the most significant of our suggestions with the aim of the convergence and the expansion of existing welding-brazing processes regulations, applied for metals.
1.) (A): Terms of Braze Welding that exist in European Standards with the given numbers of processes: 971 - Gas; 973 - Gas Metal Arc; 974 Gas Tungsten Arc; 975 Plasma Arc and, maybe Micro Plasma Arc (pp.19, 18); 75 -Light Radiant Welding (p.19, see below the point N.33.); 916 Induction Brazing (p.20).
2.) (A) & (E): to introduce (it is not obligatory) Induction Braze Welding that we marked as IBW (p.20) and, maybe, other induction joining processes first of all, high frequency ones, including IH.HF - High Frequency Induction Heating (p.271).
(A): maybe, to introduce IW.HF = 743 = Induction HF Welding that exists in (E) (p.20, 237).
3.) (E): to introduce Exothermic Braze Welding, Flow Welding (pp.19, 45, 234, 235) and the group of methods named as Welding by Stored Energy, adopted by AWS not long ago, that we marked as W.SEN (p.38, 273).
4.) (A) & (E): to convey to the customer-readers the understanding of the phenomenon of Contact Fusion and introduction of the terms of Contact Fusion Welding (WCUF) and its modifications (pp. 24-26, 267) as well as the designation of the tremendous class of Fusion Welding (FUSW) (pp.27, 57, 270), and separating inside of it the auxiliary term of Shallow Welding (SHA) (p.28, 264).
5.) (A) & (E): to underline the fact of filler material usage or the so-called autogenous processes performance (p.29), that as a specific case of (A): has to be included as, maybe, GTAW.AS = TIG.AS = AS.TIG = AS.GTAW = 142 = Autogenous Gas Tungsten Arc Welding Using Inert Gas (pp.29, 236).
6.) (A) & (E): maybe, to introduce of Micro Flame Oxyhydrogen Welding mOHW as well as a general notion of Micro Welding mW and its variants (pp. 41, 33, 34, 271). However, it is obligatory to introduce the term mPAW = Micro Plasma Welding (with direct current) and, maybe, only its main derivatives sub-methods, because of exclusive properties of low ampere arc due to its ability to be very effectively constricted (pp. 155-157, 239, 257, 258) and see below the point N.34.
7.) (A) & (E): GORW to introduce Welding by Method of G.V. Gorbunov, maybe, with main its modifications. We have to remind that this method was named by his author as welding by method of contact fusion (pp.37, 38, 236, 254).
8.) (A): only designate the existing term of Stored Energy Welding (maybe, as W.SEN), but in case of (E): to introduce this term (p.38, 39, 273).
9.) (A) & (E): to introduce the Arc Welding in Nitrogen Atmosphere (p.42, 244) and Low Pressure - we highlighted it by suffixes LP, CA -in camera & HCAD with Hollow Cathode Arc Discharge (pp.69, 70, 233, 236, 254). At the same time, it is necessary to mention High Pressure Arc Welding that we marked by suffix or prefix HYP (pp.69, 70, 233, 236, 254), as well as main Surfacing & Cladding processes and Repairing Restoration methods, including ESD - Electro-Spark Deposition process (pp.105-113, 241, 248, 254, 261-262, 264-265, 271).
10.) (E): to restore the fundamental term FOW = Forge Welding (p. 43).
11.) (A): to introduce and (E): to restore FICRW = 118 = Firecracker Welding (by Laying Electrode) and GRAW = 112 = Gravity (Arc Feed) Welding (pp. 44, 235, 236).
12.) (A) & (E): to separate TW.FU = NPTW = Thermite (Exothermic ) Welding by Fusion (Non-Pressure) and TW.PR = PTW = Thermite (Exothermic ) Welding by Pressure (pp. 46, 242).
13.) (A) & (E): among some variants of Cold Welding, maybe, to separate only: Shock (CW.SHK); Under Vacuum (CW.V) and in Space (SPC.CW) (pp.49-50, 234, 247, 264, 272).
14.) (A) & (E): to widen Diffusion Welding (DFW = 45), maybe, only to such cases as - while pressure is applied by using effect of Difference in Thermal Expansion of materials involved in process (DTE); with Intermediate Layers (IL); without vacuum (NV); Shock in vacuum (SHK) (pp.51-54, 234). Maybe, it is also reasonable to introduce as an auxiliary WDRP.W = W.WDRP = Wedge-Pressure Welding (pp.55, 242).
15.) (E): to introduce ROW = Roll Welding (pp.56, 240).
16.) (A) & (E): We must admit our mistake in pp. 59, 243 where (while basing on the deleted European Standard ISO 857-1: 1998) it was introduced AW.GS.NCE = Gas Shielded Arc Welding with Non-Consumable Electrode with number 14 of European Classification. Really for this number it had to be Tungsten Electrode. However, this term has also a right to exist.
17.) (A) & (E): to note the requirements of backing, - speaking about Submerged and other fusion welding methods, - and to reflect the usage of SAW.ON = Submerged Arc Welding with Method On (Semi-Submerged Arc Welding) that is mainly used for aluminum alloys welding (pp.64, 65, 241, 256, 263). By the way, some American documents pay serious attention to the backing.
(A): to introduce SAW.PD = MPSAW = 124 = Submerged Arc Welding with Metallic Powder Addition; SAW.ST = 122 =with Strip Electrode; SAW.STC = 126 =with Cored Strip Electrode; SAW.TE = 125 =with Tubular Cored Strip Electrode (p.241);
18.) (A) & (E): to introduce BMAW.SL = Bare Metal Arc Welding by Self-shielding (non-tubular, but monolithic) Wire (developed by T. Slytskaya) (pp.72-73, 233).
19.) (A): to introduce GTAW.TE & GTAW.TERG = 143 & 146 = Gas Tungsten Arc Welding Using Inert Gas and Tubular Cored Filler Material (Wire, Rod) & Plus Reducing Gas Additions (pp. 73, 237).
20.) (A) & (E): to provide for the designation of Welding with Stabilized Arc (STB) and of GTAW with Usage of Keyhole Effect (KY), GTAW.AFL = ATIG = PATIG = GTAW with Activating Flux Using & only for (A): Welding in Reducing Atmosphere & TAG = 147 = Gas Tungsten Arc Welding Using Active Gas (pp.75, 76, 236, 247, 270).
21.) (A) & (E): to specify the use of High Speed Rotating Arc Welding (usually mentioned in literature as HSRAW) (pp.80, 81, 255, etc.).
22.) (A): to specify the usage of compulsory forming (CF) not only in Electrogas welding processes, but also in Submerged Welding (SAW.CF) and Upset Welding (UW-2S.CF);
(E): at the same time to specify all these processes (pp.81, 82, 100, 234, 246, 263, 266, etc.).
23.) (A): to reflect the enumerated below 5 stud arc methods, because they are adopted in European Standard ISO 4063:2009, with proposed by us designations or in another way: SW.CDAD(R) = 785, SW.CDAT = 786, SW.DACS = 783, SW.DAFC = 787, SW.SCYD = 784 ((pp.84, 85, 241, 242).
(A) & (E): to introduce SJ = Stud Joining without arc usage that includes the given below Friction and Resistance Stud Welding (pp.85, 271).
24.) (A) & (E): to reflect, on possibilities, of magnetic field usage while performance of Arc, Electroslag, Resistance Welding and some Welding-Brazing processes (pp.83-85) and to underline modulated character of many methods (pp.85-87, 103, 243, 245, 249, 250, 254, 258, 260, 263-266, 268, etc.).
25.) (A): to designate some resistance methods like: RSW-ID = 211 = Indirect Resistance Spot Welding; RSEW.LS = 221 = Lap Seam Welding; RSW-D = 212 = Direct Resistance Spot Welding; RSEW.PL = 223 = Pre-Lap Seam Welding; RSEW.W = 224 = Wire Seam Welding; RSEW.FOI = 225 = Foil Butt-Seam (Resistance) Welding; RSEW.ST = 226 = Seam Welding with Strip; FW.H = 241 = Flash Welding with Preheating; FW.NH = 242 = Flash Welding without Preheating; SJ.RW = 26 = Resistance Stud Welding; maybe, FW.P-DR = Pulsed Flash Field Welding with Draw-tension, etc. (pp.97-104, 235, 240, 241, 250).
(A): only to mark & (E): to determine and to represent a few resistance processes performed in solid state condition, that although rarely, but sometimes takes place. For example, it may be: PW.SE (ss) = Projection Seam Welding in the Solid State and PW.SP (ss) = Projection Spot Welding in the Solid State (pp.104, 261).
26.) (A) & (E): to introduce ERRT Electric Resistance Restoration Technologies and ERWS Electric Resistance (Welding) Surfacing, because now they are intensively being developed (pp.110, 111, 248).
27.) (A) & (E): Electroslag Welding methods may be more represented in all documents - like ESW.R = Resistance Electroslag Welding or ESW.TE = Electroslag Welding-Surfacing with Tubular (Cored) Electrode, but in (A): it has to be obligatory given: ESW.ST = 721 = Electroslag Welding with Strip Electrode, ESW.W = 722 = Electroslag Welding with Wire Electrode, because using of wire is implied by default; maybe, ESW.TETI = Electroslag Welding with Tubular (Cored) Electrode, containing strengthening particles of TiB2, and some others (pp.115-119, 234, 248, 249).
28.) (A) & (E): to reflect such known friction joining technologies: FRW.ORB = Orbital Friction Welding, FRW.RA = Radial Friction Welding, FSSW = Friction Stir Spot Welding = FSW.SP = Spot Friction Stir Welding, SJ.FSW = SFSW = Stud Friction Stir Welding. Maybe, it is also reasonable to mention SRF.FR = Friction Surfacing, but obligatory for (A): SJ.FRW = 423 = Friction Stud Welding (120-123, 235, 241, 250).
29.) (A) & (E): maybe, to widen Ultrasonic Welding methods. And in any case the mention of ultrasonic oscillations usage looks logical as a minimum as in Resistance, Diffusion and, maybe, Arc Welding, as well in some welding-brazing processes. For example, such designations may be used for: RSW.US.W-R = US.W-R.RSW = Resistance Spot Welding with Using of Ultrasound Oscillation in Conformity with Wedge-Reed System, DFW.CPUS = Diffusion Welding with Previous Applying of Ultrasonic Oscillations, AW.USF = Arc Welding in Ultrasonic Field and BW.USF = Braze Welding with Ultrasonic Oscillations Usage (pp.124, 125, 245, 247, 263, 266).
30.) (A) & (E): Percussion and Capacitor Discharge Welding methods belong to the group of W.SEN = Stored Energy Welding methods group (point N.8.), but what to choose among proposed by us terms and designations is a task of experts in this field. Probably, as one of the main term can be stated CDW = W.CD = Capacitor Discharge Welding that may be divided on some sub- methods shown in FIG.11-6, with Percussion Welding, including one in Vacuum (PEW.V) (pp.126-133, 233, 246, 261, 270).
31.) (A) & (E): The term THCOW = Thermocompression Welding has a right to exist. In ISO 857-1:1998 and Russian Standard 857-1: 2009 there are given the general definition of Heated Element Welding (Welding by Heated Element) - that we marked as HELM - and related to it modifications. The majority of them we used, but under the name of THCOW modes, and we invite the experts to deal with them (pp.133, 134, 242, 265, 266).
32.) Comment: The introduced in Chapter 12 Group of Quick-Momentary Welding Processes (W.QM & W.QP/M), illustrated by FIG.12-1 (p.135) about three whales on which rests the welding, maybe, has surprised the experts. However, it permits to give the simplest explanation, for example, of possibilities to join dissimilar materials while usage such processes as Explosion (EXW), Magnetic Pulse (MPW) and the so-called Cold Metal Transfer Gas Metal Arc Welding (see point N.36. If these considerations are approved by experts, they can be documented by (A) & (E). (135-144, 273).
(A): to adopt the term HMEW = 44 = welding by High Mechanical Energy which unites EXW and MPW in one group. Other our suggestions may be debatable, however, in some cases it looks reasonable for - (A) & (E): to underline such processes in vacuum as EXW.V and MPW.V (136, 138, 139, 249, 257).
33.) (A) & (E): to take, in our opinion, into consideration the existence of LEBW = Low Energy Beam Welding group of methods. And among them, maybe, to reflect such Light Radiant processes as - with Dark Patched Edges in the Places to be Welded (LRW.DTP), Braze Welding (LRBW) and, probably, Brazing-Welding processes performed with Using of Sun Energy (LRBW.SUN). Speaking about HEBW = High Energy Beam Welding group of methods, that can be highlighted in (E), maybe, it is reasonable at first to reflect key holing (KY) and unfolding (UD), Pulse (P), Modulated (M) and Spot (SP) modes, as well as for LBW to name modes with Using Powder Alloys (PD), including Self-Fluxing ones (PDSF). It is debatable to mention LBW.EL = Pulsed Laser Welding by Beams with Elliptical Form without Filler Material and LBW.EMPS = Laser Beam Welding with Electromagnetic Support of Weld Pool and such modes of LBW as: with Attendant Loading by Mechanical Force (ALF), with long focal length using Key hole effect- Remote (RKY), Scanner (SC). However, maybe, it looks desirable to introduce for high concentrated energy welding methods by fusion such term as W.SELT = SELT.W = Fusion Welding by Seam Lap, Tee, and Closed Corner - Joints (using Arc, Plasma, Beam Processes and their combinations) without filler material usage. (145-153, 237, 247, 248, 256, 264).
(A): to introduce EBW.SG = 513 = Electron Beam Welding with Addition of Shielding Gas and such sub-methods of LBW as: Solid State (LBW.SO = 521), Gas (LBW.GA = 522) and Semi-conductor (LBW.LDKY = 523) and (as it was written in point N.1.) LRW = Light Radiant Welding. (146, 148, 152, 234, 238).
34.) Comment: Speaking about Plasma Treatment of metals, we have to note that generally a constricted arc may be received due to obtaining the arc column with rather smooth cross section by such main means: 1) plasma forming nozzles; 2) focusing by external flow of gas or 3) water and its steam, by an external 4) magnetic field or 5) high frequency electric field + some their combinations. That is why me make the general marking of Constricted Arc Welding as CN.AW. However, in the majority of cases now in practice there are used means NN.1 & 2 and rarely - N.3. And realized by them processes are named as Plasma Arc Welding ones - PAW. In the point N.6. was firstly mentioned the motivation of separation of mPAW (< 25-40 A) and PAW (> 40 A and up to a few thousands amperes). The matter is that effect of constricting arc is to the greatest extent manifesting while very small arc currents (especially, <5-10A), when while right welding parameters usage, due to very high concentration of heat, Micro Plasma Welding may be in competition with EBW and LBW. There is used the so-called needle arc (see FIG.14-4 and FIG. 14-5 of pp. 156, 157). But we have to avoid double arcing as it is explained in p.157 & FIG.14-6. Because mPAW is used for thin metals, we propose to: (A) & (E): to introduce, as minimum, such Micro Plasma modes: with direct current in continuous mode (mPAW.A); by Alternative Current (mPAW.AC); by straight polarity rectangular pulses without using of filler material (mPAW.B); by variable polarity impulses (mPAW.C = mPAW.RP) similar to the mode mPAW.AC, but characterized in that the impulses are rectangular and amplitude of straight polarity pulses is about 2 times bigger than of ones of reverse polarity; with reverse polarity current (mPAW.D); Low pressure (mPAW.LP). mPAW.BN = Micro Plasma Welding by straight polarity pulses with BACTRIAN (two-humped) camel shape without using of filler material FIG.14-19, -20, -21, pp.167-169 as well as the so-called Modernized Foil Edge Weld EFM (FIG.14-18; p.166) can be adopted, maybe, later. Also for thin metal it is reasonable to reflect different methods by the Welding with Attendant Loading by Mechanical Force (we mark these methods by suffix ALF) pp.158-159, FIG.14-7, 14-9,); Plasma Bidden (BID) (FIG.14-7, p.158) and Bidden Pulse (BID.P) techniques. Among indeed Plasma Welding Processes, as we suggest, besides the mentioned above ones it is obligatory necessary to highlight such as: with Alternative Current (PAW.AC); with Key hole effect (PAW.KY) (FIG.14-18, p.160); Pulsed (PAW.P); Powder-feed (PAW.PD) FIG.14-31, p.175; Three Phase (PAW.THP); Plasma Steam Welding (PAW.STM) FIG.14-32, p.176, 177) unfortunately we did not note it in LIST 20-1; and, maybe, some other next to them welding methods, including plasma welding with hot wire (FIG.14-30, p.30), in N2 or CO2 shielding atmosphere (FIG.14-37, p.179). (See also pp.154-179, 239, 240, 260, 271).
(A): to introduce PABW = 975 = Plasma Arc Braze Welding; PAJW = 154 = Plasma Arc Jet Welding (Plasma Arc Welding with Non-Transferred Arc; PA-JW = 155 = Plasma Arc Welding with Semi-Transferred Arc (pp.19, 158, 239).
35.) (E): to take into consideration the terms and definitions of Manual (MA), Semi-Automatic = Partly Mechanized (SA=PAM), Automatic=Fully Mechanized=Machining (AU=FUM=MACH) and robotic (RB) welding. The latter definition, as to us, is better than that used by AWS (ROB), and it should be linked specifically to the used welding method. For instance, it may be GMAW.RB = RB.GMAW = Robotic Gas Metal Arc Welding (p.180, 181). In the both (A) & (E) it would be wise to allocate the term Low-cost automation of (arc) ~ Simple=Small Mechanized (SM) welding. But much more important for normative documents is to reflect possible variants of ORB = Orbital Welding (FIG.15-3, p.183) together with used during these processes backing. For example, it may be ORB.LBW.WBG.AR = Orbital Welding with Gas Backing by Argon. Speaking about orbital welding it is reasonable to separate tube to tube (including the domination for pipe welding according to ASME code, FIG.15-3a & b, p. 183 and FIG.15-4, p.184) and tube to plate processes (FIG.15-3c, p.183 & FIG.15-5, 15-6, 15-7, 15-8, pp.184-186). It is also logical to highlight Multiple (MU) processes, as well as during orbital as while submerged welding (FIG.15-2, p.182). Rarely used method AW.IE = Welding by Immovable Electrode (FIG.15-9, p.186,187), in our opinion has to be also mentioned in auxiliary normative documents (pp.180-187, 259, 260, 271)- nearly the mentioned above in the point N.11. FICRW = 118 = Firecracker Welding.
36.) Comment: In our LISTs 20-1, 20-2 & 20-3 there are given a lot of GMAW methods, and it is difficult to take into account all of them. That is why in LIST 20-1 we noted the given in European Standard for (A): GMABW = 973 = Gas Metal Arc (Weld Brazing) Braze Welding, GMAW.MLC = MIG.MLC = GMAW.TEML = MIG.TEML = 133= Gas Metal Arc Welding with Using Inert Gas and Metal Cored Wire. Comment: The both (A) & (E) documents provide such general GMAW methods with sometimes corrected by us designations of transfer modes: GMAW.GL = 13-G (Globular); GMAW-P = 13-P (Pulsed); SMAW-S = 13-D (Short Circuiting=Deep Transfer); GMAW-SY = 13-S (Spray-Axial). We add to the both (A) & (E): GMAW-RSY = 13-RS (Rotational Spray) FIG.16-4, p.193 (and see also FIG.16-5, p.194, FIG.16-15, p.201). In spite of some dozens of the given in LIST 20-2 GMAW modes (pp.250-253), in our opinion, their big quantity may be limited only to: GMAW.AC (with Alternative Current) ~ GMAW.VP (with Variable Polarity), GMAW.CMT (using Cold Metal Transfer), GMAW.DP (Double Pulsed) ~ GMAW.PP (Pulse on Pulse). It is also possible officially to recognize at first the GMA methods with such names: STT (p.196, FIG.16-7), TIME (pp.201, 202, FIG.16-15) and Synergic (SYN) (p.199, FIG.16-11). In future the list of approved regulations in Gas Metal Arc Welding techniques can be essentially refined by experts in this area. In particular, it relates to GMAW.TIME-TW(-TD) = 13-S (sub-variants) = Gas Metal Arc Welding with TWIN(TANDEM) T.I.M.E. - process of Spray (transfer) or CO2-2SD.W (CO2-2S welding) = Welding in Carbon Dioxide Atmosphere, Using the Gas with Two Speeds as well as many others (pp.188-208, 235,236, 250-253).
37.) Comment: We decided to separate the group of welding under extreme conditions (UE -Unusual Environmental Conditions or HCW Hard Conditions Welding, p.209). As seem to us, the standards of (A) & (E): must obligatory include as a minimum 2 important terms: SPC.W = Space Welding (unfortunately, it is given in the both LISTs 20-1 & 20-3 instead of only one pp.241, 271) and UWW = Underwater Welding (though it is a general term, by default it means UWW.W = Underwater Wet Welding pp.242, 272). On the contrary UWW.DR = Underwater Dry Welding exists that practically is equivalent to HYP.AW = Hyperbaric Arc Welding (see the point N.9.). The variants of wet welding may be marked with the application of suffixes that show the used given specific method, like UWW.TCE = Underwater Welding by Tubular Covered Electrode (FIG.17-5, p.213) or UWW.GTA (FR, FS, etc.) = Underwater Gas Tungsten Arc (Friction, Friction Stir, etc.) Welding pp.209, 211-214, 266, 267. The same principle may be used while definition of Space Welding specific method: Arc (AW), Cold (CW), Diffusion (DFW), Resistance (RW). As an example, we can give SPC.SUNW = Space Welding with using of Solar (Sun Light) Energy (pp. 209-217, 241, 242, 264, 266, 267, 271, 272).
38.) The situation with definitions of hybrid and combined welding methods looks simple, however for (A) & (E): it is problematic to reflect such exclusive methods, for instance, as: (LB+PA).GASPD.SRF = Hybrid Laser Beam and Plasma Arc Gas Powder Surfacing, (LB+IH).SRF = Hybrid Laser-Induction (attendant Heating) Surfacing. GTAW.PAW.CX = Tungsten Inert Gas Welding Combined with Coaxial Plasma Arc is a very simple definition (FIG.18-5c, p.220). But there are more simple examples connected with the so-called Re-welding (pp.108, 109), like RE.mPAW- DFW = The Repeated Welding, including first Micro Plasma Welding and then Diffusion Welding. (pp.218-222, 237, 239, 240, 253, 255, 261, 262).
39.) (A) & (E): Resuming our considerations about general classes of welding, we suggest that such basic obligatory definitions have to be saved: 0) FUSW = 0 = Fusion Welding; 1) AW = 1= Arc Welding; 2) RW = 2 = Resistance Welding; 3) because of bigger universality instead of OFW we propose other abbreviation - GASW = 3 = (Fuel) Gas Welding (of course, this statement is debatable); 4) PRW = 4 = Pressure Welding with division of it into: 4a) PRW.FU = 4a = Pressure Welding with Fusion, 4b) PRW.NFU = 4b = Pressure Welding without Fusion and 4c) PRW.SFU = 4c = Pressure Welding with very Slight local Fusion. Further: 5a) LEBW = Low Energy Beam Welding Processes, 5b) HEBW = High Energy Beam Processes. Then, according to our suggestions (which are also debatable), may be proposed the new very large class of methods 6) W.PRA = 6 = Welding with application of Pressure. We think that this class may cover: PRW = 4, ESW, EGW + CF.SAW, the separated by us GORW, TW.PR, W.QM, the biggest part of RW = 2 = Resistance Welding (including the mentioned in point N.25 method FW.P-DR) and many methods that we marked by suffix ALF (see point N.34). And in ISO 4063 free number 6 can be given to this massive class which together with very large class of FUSW = 0 = Fusion Welding is roughly shown in FIG.19-1, p.226. Practically the provided by ISO 4063 groups with number 7 & 9 all joining methods belong to FUSW = 0 and W.PRA = 6 = Welding with application of Pressure. As it is known, the designation by number the 8-th group (penultimate) methods does not belong to welding-brazing processes. Let us here pay a little bit attention to proposed by us parts of PRW = 4 = Pressure Welding. It is almost everything clear with such its part as PRW.FU = 4a = Pressure Welding with Fusion. But, maybe, only now we understand that the provided by AWS Solid State Welding class SSW = PRW.NFU = 4b = Pressure Welding without Fusion + PRW.SFU = 4c = Pressure Welding with very slight Local Fusion.
40.) At the end it is reasonable to underline that we have to designate some processes and tools effects connected with welding methods. There are 3 categories of these processes: Preliminary, Attendant and subsequent (Post). Besides the mentioned above methods with Attendant Loading by mechanical Force (ALF) see our points N.34, N.39, - it may be pre-heating (H), Post High frequency-ultrasonic peening (HFPI), Local pre-Heating (LOH), Post Heat treatment (PH), etc. (pp. 243, 244, 269). Speaking about this book General TABLE (22-1), we understand that it does not include many important facts and publications that have been fixed in Eastern Europe, USA and Japan, but were, unfortunately, unknown for this book author. And he would be very glad to receive any advices and remarks that can improve this table- Chapter 22, hoping that in any case this book will be useful for its readers (especially for ones that are non-sufficiently familiar with elaborations and achievements in the field of welding made in the former Soviet Union and the post-Soviet space). The author will hope that the American Welding Society and the International Institute of Welding, although slowly, but still will take into account some of the proposals contained in this book, contributing to the international harmonization of welding and related to it terms.
*It is well known that, according to European Standards, markings of methods are given by numbers.