2016 №06 (12) |
DOI of Article 10.15407/tpwj2016.06.13 |
2016 №06 (14) |
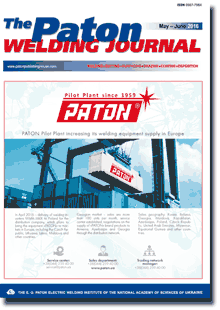
The Paton Welding Journal, 2016, #5-6, 75-80 pages
Peculiarities of structure of Cu–Cu, Ni–Cu and Steel–Cu joints produced by overlap friction stir welding method
G.M. Grigorenko, M.A. Poleshchuk, L.I. Adeeva, A.Yu. Tunik, E.V. Zelenin And S.N. Stepanyuk
E.O. Paton Electric Welding Institute, NASU 11 Kazimir Malevich Str., 03680, Kiev, Ukraine. E-mail: office@paton.kiev.ua
Abstract
The work is dedicuted to investigation of overlap friction stir welded joints of sheet billets of homogeneous (Cu–Cu) and dissimilar metals with unlimited (Ni–Cu) and limited solubility (Cu–St.3, Kh18N10–Cu) of the components in solid state. The FSW process is performed due to plastic deformation of metal being heated to recrystallization temperature without melting. The leading role in this process plays mechanical stirring of metals in plastic state. The role of diffusion processes is insignificant. The quality joints are received at optimum welding modes. Plasticization and dynamic recrystallization in FSW of Cu–Cu plates promote for grain refinement (5–30 mm) in the stir zone and develop dense weld microstructure, comparable with the base metal. The weld microhardness reaches 80–107 % of the base metal microhardness. FSW of Cu and Ni resulted in the quality welded joint with mutual penetration of one metal into another at up to 3 mm depth. Interdiffusion of Cu and Ni along the grain boundaries takes place at up to 20 μm depth with formation of solid solution interlayers of these metals. Examination of Cu–St.3 and Kh18N10–Cu joints demonstrated significant grain refining in the recrystallization zone as well as in the HAZ. St.3 and Kh18N10 steels plung in copper at 1000 and 2000 μm depth in form of bands and strips. Large amount of Fe-based inclusions, embedded in form of separate bands and particles, is noted in the stir zone. Thus, applying the welds at specific distance from each other allows producing quality solid welding-up of upper thinner plate to massive lower plate (as in deposition) with overlapping of recrystallization zones at minimum heating and distortion of the parts. The carried investigations allow recommending this method for reconstruction of initial dimensions and development of protective layer (Ni, Kh18N10 steel) on copper plates of CCM mold. 11 Ref., 1 Table, 8 Figures.
Keywords: friction stir welding, lap joint, mechanical stirring of metals, diffusion, solubility in solid phase, microstructure, X-ray spectrum microanalysis, chemical composition, microhardness
Received: 14.04.16
Published: 19.07.16
References
- Thomas, W.M. Friction stir butt welding. Pat. 9125978.8 G.B. Int. Cl. PCTrGB92. Publ. 01.12.91.
- Lebedev, V.K., Chernenko, I.A., Mikhalsky, R. et al. (1987) Friction welding: Refer. Book. Leningrad: Mashinostroenie.
- Ericsson, L.G., Larsson, R. (2003) Rotational friction welding: Researches and new fields of application. Tekhnologiya Mashinostroeniya, 6, 81–84.
- Mishraa, R.S., Ma, Z.Y. (2005) Friction stir welding and processing. Materials Sci. and Eng., 50, 1–78.
- Arbegast, W.J. (2006) Friction stir welding. After a decade of development. Welding J., 85(3), 28–35.
- Grigorenko, G.M., Adeeva, L.I., Tunik, A.Yu. et al. (2014) Structural features of FSW joints of metals with different element solubility in the solid phase. The Paton Welding J., 4, 6–16. https://doi.org/10.15407/tpwj2014.04.01
- Xue, P., Ni, D.R., Wang, D. et al. (2011) Effect of friction stir welding parameters on the microstructure and mechanical properties of the dissimilar Al–Cu joints. Materials Sci. and Eng., 528, 4683–4689.
- Saeida, T., Abdollah-Zadehb, A., Sazgarib, B. (2010) Weldability and mechanical properties of dissimilar aluminum-copper lap joints made by friction stir welding. Alloys and Compounds, 490, 652–655. https://doi.org/10.1016/j.jallcom.2009.10.127
- Kosta, A., Coelho, R.S., dos Santos, J. et al. (2000) Microstructure of friction stir welding of aluminium alloy to magnesium alloy. Ibid., 66, 953–956.
- Karmanov, V.V., Kameneva, A.L. (2013) Friction stir welding of aluminium alloys: Matter and specifics of process. Kiev: Naukova Dumka.
- Graf, E.V., Shevchuk, M.V. (2008) Friction stir welding of nonferrous metals and their alloys. In: of 12th Regional Sci.-Pract. Conf. of Students on Advanced Technologies and Economy in Machine-Building, 17–19. Yurga: TPU.