2016 №04 (01) |
DOI of Article 10.15407/as2016.04.02 |
2016 №04 (03) |
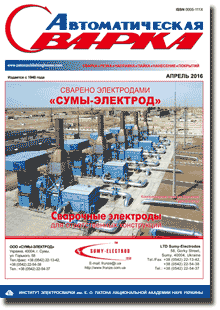
Avtomaticheskaya Svarka (Automatic Welding), #4, 2016, pp. 26-34
Influence of electric-magnetic composite field on WC particles distribution in laser melt injection
Liang Wang1,2, Yong Hu1,2, Shiying Song1,2 and Jianhua Yao1,2
1Research Center of Laser Processing Technology and Engineering, Zhejiang University of Technology 18 Chaowang Str., 310014, Hangzhou, PRC. E-mail: ddtwl@foxmail.com
2Zhejiang Provincial Collaborative Innovation Center of High-end Laser Manufacturing Equipment Hangzhou, PRC
Abstract
The laser melt injection (LMI) method is always used to prepare a metal-matrix composite layer on the surface of substrate. In LMI process, the laser beam melts the surface layer of substrate locally while simultaneously injecting particles of additional material. In order to control the distribution of reinforcement particles in LMI layer, an electricmagnetic composite field can be applied. The effect of electric-magnetic synergistic on the reinforcement particles distribution in LMI was investigated using experimental and numerical method. The spherical WC particles were used because their regular shape was most close to the simulation conditions and good tracer performance in the melt flow. The distribution of WC particles in longitudinal section was observed by SEM and calculated by computer graphics processing. The trajectory of WC particles in the melt pool was simulated by a 2D model coupled the equations of heat transfer, fluid dynamics, drag force, Lorentz force and phase transition. The simulation results were compared with experimental data and were in good agreement. The results indicated that the effect of electric-magnetic synergistic on the reinforcement particles distribution was verified. The distribution of WC particles in LMI-layer was influenced by the direction of Lorentz force induced by electric-magnetic composite field. When the Lorentz force and gravity force are in the same direction, the vast majority of particles are trapped in the upper region of LMI-layer, and when these forces are in the opposite direction, most particles are concentrated in the lower region. 34 Ref., 8 Figures.
Keywords: laser melt injection, WC particles, Lorentz force, particles distribution, electric-magnetic composite field
Received: 08.12.2015
Published: 02.06.2016
References
1. Liu, D., Chen, Y., Li, L. et al. (2008) In situ investigation of fracture behavior in monocrystalline WCp-reinforced Ti–6Al–4V metal matrix composites produced by laser melt injection. Scripta Materialia, 59, 91–94. https://doi.org/10.1016/j.scriptamat.2008.02.033
2. Li, L., Liu, D., Chen, Y. et al. (2009) Electron microscopy study of reaction layers between single-crystal WC particle and Ti–6Al–4V after laser melt injection. Acta Materialia, 57, 3606–3614. https://doi.org/10.1016/j.actamat.2009.04.021
3. Verezub, O., Kalazi, Z., Sytcheva, A. et al. (2011) Performance of a cutting tool made of steel matrix surface nano-composite produced by in situ laser melt injection technology. J. Materials Proc. Techn., 211, 750–758. https://doi.org/10.1016/j.jmatprotec.2010.12.009
4. Do Nascimento, A.M., Ocelik, V., Ierardi, M.C.F. et al. (2008) Wear resistance of WCp/duplex stainless steel metal matrix composite layers prepared by laser melt injection. Surface and Coatings Techn., 202, 4758–4765. https://doi.org/10.1016/j.surfcoat.2008.04.061
5. Cabeza, M., Castro, G., Merino, P. et al. (2014) A study of laser melt injection of TiN particles to repair maraging tool steels. Surface and Interface Analysis, 46, 861–864. https://doi.org/10.1002/sia.5373
6. Do Nascimento, A.M., Ocelik, V., Ierardi, M.C.F. et al. (2008) Microstructure of reaction zone in WCp/duplex stainless steels matrix composites processing by laser melt injection. Surface and Coatings Techn., 202, 2113–2120. https://doi.org/10.1016/j.surfcoat.2007.08.065
7. Vreeling, J.A, Ocel??k, V., Pei, Y.T. et al. (2000) Laser melt injection in aluminum alloys: On the role of the oxide skin. Acta Materialia, 48, 4225–4233. https://doi.org/10.1016/S1359-6454(00)00278-0
8. Li, F.q., Li, L.q., Chen, Y.b. (2013) Arc enhanced laser melt injection of WC particles on Al surface. Surface Eng., 29, 296–299. https://doi.org/10.1179/1743294412Y.0000000094
9. Pei, Y.T., Ocelik, V., de Hosson, J.T.M. (2002) SiCp/Ti6Al4V functionally graded materials produced by laser melt injection. Acta Materialia, 50, 2035–2051. https://doi.org/10.1016/S1359-6454(02)00049-6
10. Vreeling, J.A., Ocelik, V., de Hosson, J.T.M. (2002) Ti–6Al– 4V strengthened by laser melt injection of WCp particles. Ibid., 50, 4913–4924. https://doi.org/10.1016/s1359-6454(02)00366-x
11. Chen, Y., Liu, D., Li, F. et al. (2008) WCp/Ti–6Al–4V graded metal matrix composites layer produced by laser melt injection. Surface and Coatings Techn., 202, 4780–4787. https://doi.org/10.1016/j.surfcoat.2008.04.057
12. Liu, A., Guo, M., Hu, H. (2009) Improved wear resistance of low carbon steel with plasma melt injection of WC particles. J. Materials Eng. and Performance, 19, 848–851. https://doi.org/10.1007/s11665-009-9547-y
13. Liu, A., Guo, M., Hu, H. et al. (2008) Microstructure of Cr3C2-reinforced surface metal matrix composite produced by gas tungsten arc melt injection. Scripta Materialia, 59, 231–234. https://doi.org/10.1016/j.scriptamat.2008.03.012
14. Guo, M., Liu, A., Zhao, M. et al. (2008) Microstructure and wear resistance of low carbon steel surface strengthened by plasma melt injection of SiC particles. Surface and Coatings Techn., 202, 4041–4046. https://doi.org/10.1016/j.surfcoat.2008.02.019
15. Liu, A., Guo, M., Zhao, M. et al. ( 2007) Microstructures and wear resistance of large WC particles reinforced surface metal matrix composites produced by plasma melt injection. Ibid., 201, 7978–7982. https://doi.org/10.1016/j.surfcoat.2007.03.042
16. Liu, D., Li, L., Li, F. et al. (2008) WCp/Fe metal matrix composites produced by laser melt injection. Ibid., 202, 1771– 1777. https://doi.org/10.1016/j.surfcoat.2007.07.053
17. Verezub, O., Kalazi, Z., Buza, G. et al. (2009) In-situ synthesis of a carbide reinforced steel matrix surface nanocomposite by laser melt injection technology and subsequent heat treatment. Ibid., 203, 3049–3057. https://doi.org/10.1016/j.surfcoat.2009.03.024
18. Guo, B., Fletcher, D.F., Langrish, T.A.G. (2004) Simulation of the agglomeration in a spray using Lagrangian particle tracking. Appl. Math. Modelling, 28, 273–290. https://doi.org/10.1016/S0307-904X(03)00133-1
19. Minier, J.-P. (2015) On Lagrangian stochastic methods for turbulent polydisperse two-phase reactive flows. Progress in Energy and Combustion Sci., 50, 1–62. https://doi.org/10.1016/j.pecs.2015.02.003
20. Chen, Y., Liu, D., Li, L. et al. (2009) Microstructure evolution of single crystal WCp reinforced Ti–6Al–4V metal matrix composites produced at different cooling rates. J. Alloys and Comp., 484,108–112. https://doi.org/10.1016/j.jallcom.2009.04.057
21. Kloosterman, A.B., Kooi, B.J., de Hosson, J.T.M. (1998) Electron microscopy of reaction layers between SiC and Ti–6Al– 4V after laser embedding. Acta Materialia, 46, 6205–6217. https://doi.org/10.1016/S1359-6454(98)00265-1
22. Anandkumar, R., Almeida, A., Vilar, R. et al. (2009) Influence of powder particle injection velocity on the microstructure of Al–12Si/SiCp coatings produced by laser cladding. Surface and Coatings Techn., 204, 285–290. https://doi.org/10.1016/j.surfcoat.2009.07.025
23. Gatzen, M., Tang, Z., Vollertsen, F. (2011) Effect of electromagnetic stirring on the element distribution in laser beam welding of aluminium with filler wire. Physics Procedia, 12, 56–65. https://doi.org/10.1016/j.phpro.2011.03.008
24. Tang, Z., Gatzen, M. (2010) Influence on the dilution by laser welding of aluminum with magnetic stirring. Ibid., 5, 125–137. https://doi.org/10.1016/j.phpro.2010.08.037
25. Gatzen, M. (2012) Influence of low-frequency magnetic fields during laser beam welding of aluminium with filler wire. Ibid., 39, 59–66. https://doi.org/10.1016/j.phpro.2012.10.014
26. Velde, O., Gritzki, R., Grundmann, R. (2001) Numerical investigations of Lorentz force influenced Marangoni convection relevant to aluminum surface alloying. Int. J. Heat and Mass Transfer, 44, 2751–2762. https://doi.org/10.1016/S0017-9310(00)00299-4
27. Bachmann, M., Avilov, V., Gumenyuk, A. et al. (2013) About the influence of a steady magnetic field on weld pool dynamics in partial penetration high power laser beam welding of thick aluminium parts. Ibid., 60, 309–321. https://doi.org/10.1016/j.ijheatmasstransfer.2013.01.015
28. Schneider, A., Avilov, V., Gumenyuk, A. (2013) Laser beam welding of aluminum alloys under the influence of an electromagnetic field. Physics Procedia, 41, 4–11. https://doi.org/10.1016/j.phpro.2013.03.045
29. Zhou, J., Tsai, H.-L. (2007) Effects of electromagnetic force on melt flow and porosity prevention in pulsed laser keyhole welding. Int. J. Heat and Mass Transfer, 50, 2217–2235. https://doi.org/10.1016/j.ijheatmasstransfer.2006.10.040
30. Bachmann, M., Avilov, V., Gumenyuk, A. et al. (2012) Numerical simulation of full-penetration laser beam welding of thick aluminium plates with inductive support. J. Physics D: Appl. Physics, 45, 035201. https://doi.org/10.1088/0022-3727/45/3/035201
31. Akbari, M., Saedodin, S., Toghraie, D. et al. (2014) Experimental and numerical investigation of temperature distribution and melt pool geometry during pulsed laser welding of Ti6Al4V alloy. Optics & Laser Techn., 59, 52–59. https://doi.org/10.1016/j.optlastec.2013.12.009
32. Morville, S., Carin, M., Peyre, P. et al. (2012) 2D longitudinal modeling of heat transfer and fluid flow during multilayered direct laser metal deposition process. J. Laser Appl., 24, 032008. https://doi.org/10.2351/1.4726445
33. Brent, A.D., Voller, V.R., Reid, K.J. (1988) Enthalpy-porosity technique for modeling convection-diffusion phase change: Application to the melting of a pure metal. Numerical Heat Transfer. Pt B: Fundamentals, 13, 297–318. https://doi.org/10.1080/10407798808551388
34. Fu, Y., Loredo, A., Martin, B. et al. (2002) A theoretical model for laser and powder particles interaction during laser cladding. J. Materials Proc. Techn., 128, 106–112. https://doi.org/10.1016/S0924-0136(02)00433-8