2017 №04 (08) |
DOI of Article 10.15407/as2017.04.09 |
2017 №04 (10) |
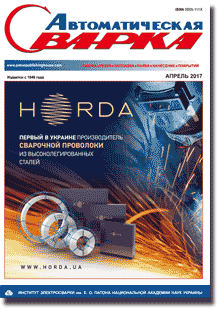
Avtomaticheskaya Svarka (Automatic Welding), #4, 2017, pp. 48-53
Development of electric arc spray coatings for reconditioning rods of hydraulic cylinders of mining equipment, using flux-cored wires
T.R. Stupnitsky, M.M. Student, V.I. Pokhmursky and M.B. Tymus
G.V. Karpenko Physico-Mechanical Institute, NASU 5 Nauchnaya Str., 79060, Lvov, Ukraine. E-mail: student-m-m@ipm.lviv.ua
Abstract
The paper outlines the main requirements to flux-cored wires based on ferroalloys of Fe–Cr–C and Fe–Cr–B systems with more than 12 wt.% chromium for electric arc spraying of wear- and corrosion-resistant coatings. It is found that, unlike steel, presence of 12 wt.% chromium in flux-cored wire charge does not ensure corrosion resistance of coatings in neutral water solutions. The causes for that were studied. It is experimentally established that corrosion resistance of coatings containing more than 12 wt.% chromium is inversely proportional to their chemical microheterogeneity. High effectiveness of application of coating impregnation with inhibited 3 % solution of Hydroway 1060 to prevent aggressive environment penetration through pores in the coating to the substrate is demonstrated. Synergistic compositions of sodium benzoate + benzyl benzoate inhibitors were developed, which provide up to 99.14 % degree of corrosion protection of the coating steel substrate. 12 Ref., 1 Table, 8 Figures.
Keywords: arc spray coatings, flux-cored wires, ferroalloys, chemical heterogeneity, corrosion resistance, oxide, carbide, boride, inhibitor
Received: 20.03.17
Published: 17.04.17
References
- Picas, J.A., Forn, A., Matthaus, G. (2006) HVOF coatings as an alternative to hard chrome for pistons and valves. Wear, 261, 477–488. https://doi.org/10.1016/j.wear.2005.12.005
- Aguero, A. et. al. (2011) HVOF-deposited WCCOCr as replacement for hard Cr in landing gear actuators. Thermal Spray Techn., 20(6), 1292–1309. https://doi.org/10.1007/s11666-011-9686-1
- Flitney, B. (2007) Alternatives to chrome for hydraulic actuators. Sealing Technology, 10, 8–12. https://doi.org/10.1016/s1350-4789(07)70460-9
- Markovich, S.I. (2007) Increase in wear resistance of machine parts by electric arc spraying of composite coatings using dissimilar wires: Syn. of Thesis for Cand. of Techn. Sci. Degree. Kiev.
- Poletaev, V.A., Tretyakova, N.V. Karamov, I.A. (2007) Examination of metallized electric pump parts for wear resistance. Vestnik IGEU, 3, 1–4.
- Baldaev, L.Kh. et al. (2007) Efficiency of application of modern thermal spraying methods for corrosion and wear protection of chemical industrial equipment. Khimicheskaya Tekhnika, 11, 32–33.
- Janpin, K., Jiansirisomboon, S. (2011) Characterization and microstructure of thermal sprayed stainless steel/magnesium oxide nanocomposite coatings. of the Microscopy Society of Thailand, 4(1), 56–59.
- Dallaire, S., Legoux, J.-P., Levert, H. (1995) Abrasion wear resistance of arc-sprayed stainless steel and composite stainless steel coatings. Thermal Spray Techn., 4(2), 163–168. https://doi.org/10.1007/BF02646107
- Wielage, B. et al. (2013) Iron-based coatings arc-sprayed with cored wires for applications at elevated temperatures. Surface and Coating Technology, 220, 27–35. https://doi.org/10.1016/j.surfcoat.2012.12.013
- Khoma, M.S., Sisin, G.M. (2010) Influence of corrosion in environment with different pH on local electrode potentials of steels. -Khim. Mekhanika Materialiv, 3, 92–97.
- Stupnytskyi, T.R. et al. (2016) Optimization of the chromium content of powder wires of Fe–Cr–C and Fe–Cr–B systems according to the corrosion resistance of electric-arc coating. Materials Sci., 52(2), 165–172. https://doi.org/10.1007/s11003-016-9939-8
- (1981) book on chemistry. Ed. by A.M. Sukhotin. Leningrad: Khimiya.