2018 №06 (06) |
DOI of Article 10.15407/as2018.06.01 |
2018 №06 (02) |
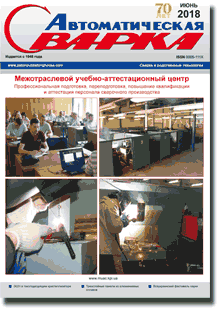
Avtomaticheskaya Svarka (Automatic Welding), # 6, 2018, pp. 3-11
Evolution of structure of nickel oxide dispersion strengthened alloys in fusion welding
K. A. Yushchenko, B. A. Zaderii, I. S. Gakh, A. V. Zvyagintseva, L. M. Kapitanchuk, Yu. V. Khaskin
E.O. Paton Electric Welding Institute of the NAS of Ukraine. 11 Kazimir Malevich Str., 03150, Kyiv, Ukraine. E-mail:office@paton.kiev.ua
Change of nanodispersed structure of nickel OSD-alloys as a result of fusion welding was considered. Welded joints, produced at different modes of argon-arc, electron beam and laser welding, were investigated. It is shown that degradation of nanosized structure takes place in all considered cases. It expressed mainly in change of strengthening particles up to microsized level, some variation of their chemical composition and morphology. A level of structure degradation depends on a level of overheating of weld pool metal, which in turn, is determined by value of specific power, welding rate, heat input and cooling nature. It is shown that the positive result, i.e minimum degradation of initial metal nanostructure, can be reached at optimum combination of the maximum technologically acceptable welding rate and heat input concentration, minimum margin and controlled distribution of power, which provide through penetration and formation of weld with parallel fusion surfaces. 19 Ref. , 9 Fig.
Keywords: OSD-nickel alloys, fusion welding, weld pool, degradation of nanodispersed particles, welding rate, heat input nature, weld formation
Received: 12.04.2018
Published: 29.05.2018
References
- Gessinger, G.Kh. (1988) Powder metallurgy of high-temperature alloys. Chelyabinsk, Metallurgiya, Chelyab. Div. [in Russian].
- Valiev, F.Z., Aleksandrov, I.V. (2007) Volumetric nanostructured metallic materials: Production, structure and properties. Moscow, IKTs Akademkniga [in Russian].
- Chebryakova, E.V. (2011) Peculiarities of mechanism of strengthening of metal matrices with nanoparticles of refractory compounds. In: of All-Russian Conf. on Nanomaterials NANO 2011. Moscow, IMET RAN [in Russian].
- Gusev, A.I. (1998) Effect of nanostructural state in compact metals and joints. Uspekhi Fiz. Nauk, 168, 29–58 [in Russian].
- Soni, P.R. (2000) Mechanical alloying: Fundamentals and applications. Cambridge, Cambridge Int. Sci. Publ.
- He, X.D., Xin, Y., Li, M.W., Sun, Y. (2009) Microstructure and mechanical properties of ODS-Ni-based superalloy foil produced by EB-PVD. of Alloys and Compounds, 467(1–2), 347. https://doi.org/10.1016/j.jallcom.2007.11.122
- Gleiter, H. (2000) Nanostructured materials. Basic concepts and microstructure. Acta Mater., 48(1), 1–29. https://doi.org/10.1016/S1359-6454(99)00285-2
- Andrievsky, R.A., Glezer, A.M. (1999) Size effects in nanocrystalline materials. Peculiarities of structure. Fizika Metallov i Metallovedenie, 88(1), 50–73 [in Russian].
- Rebinder, P.A. (1958) Physicochemical mechanics. Moscow [in Russian].
- Janko, B. (1986) High-temperature alloys for gas turbines and other application. Brussels, D. Ridee.
- Kondrik, A.I., Kovtun, G.P., Datsenko, O.A. et al. (2008) Modern materials for thermonuclear power engineering. Kharkov, NNTsKhPTI [in Russian].
- Azerenkov, N.A., Kovtun, G.P., Litovchenko, S.V. (2009) Nanotekhnologies and nanomaterials in nuclear power engineering. In: of Int. Scient. Conf. on Physicochemical Principles of Formation and Modification of Micro- and Nanostructures. FMMN, Zbirnyk Nauk. Prats. Kharkiv, NFTTsMON ta NANU, 2009, 152–157.
- Kovtun, G.P., Verevkin, A.A. (2010) Nanomaterials: Technologies and materials science (Review). Kharkov, NNTs KhPTI [in Russian].
- Howard, S.M., Jasthi, DB, K., Arbegast, W.J. et al. (2004) Friction stir welding of MA957 oxide dispersion strengthened ferritic steel. In: Fusion materials semiannual progress report for the period ending. December 31, 55–60.
- Hemilton, M.L. et al. (2000) Fabrication technology for ODS alloy MA957, PNL-13165.
- Shinozaki, K et al. (1997) Metallurgical and mechanical properties of ODS alloy MS956 friction welds. Welding J., 76(8), 289–299.
- Feng, Z., Ren, W. (2006) Initial development in joining of ODS alloys using friction stir welding. Report No. ORNL/GEN4LTR-06-021.
- Portnoj, K.I., Babich, V.N. (1974) Dispersion-hardened materials. Moscow, Metallurgiya [in Russian].
- Kelly, A., Nicholson, R. (1966) Dispersion hardening. Moscow, Metallurgiya [in Russian].