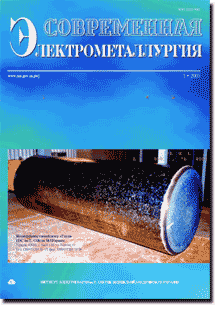
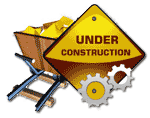
ELECTROSLAG TECHNOLOGY
Mitchell A. and Frederiksson H. Electroslag remelting of high-nitrogen steels 2
Steels containing nitrogen at levels which are at or above the 1 bar saturation solubility limit in the liquid at the liquidus temperature offer considerable metallurgical property advantages in many respects. For example, when nitrogen is used as a substitute for carbon in stainless grades, the alloys have superior corrosion properties especially in biomedical applications: nitrogen as a strengthening element in tool steels offers advantages in freedom from carbide particles which affect the polishability. Most of the steels grade of interest require electroslag remelting to control segregation without loss of nitrogen and the behaviour of nitrogen during this process is the subject of this work. It is concluded that the required process pressures are closely related to the alloy composition and that to prevent porosity in the product the ESR step must be carried out at an appropriate overpressure of either nitrogen or argon. The addition of nitrogen during ESR is also discussed and it is shown that this is possible only through solid additives.
Zhadkevich M.L., Biktagirov F.K., Shapovalov V.A., Ignatov A.P. and Gnatushenko A.V. Application of electroslag melting for production of ferroalloys from mineral raw material 10
It is shown that the electroslag melting with non-consumable electrodes has much in common with a multi-slag ore-thermal process. In either case the power is generated mainly in the condition of resistance, which is a molten slag. Therefore, the electroslag melting is rather suitable for the processing of mineral raw material with a selective recovery of metals in case of producing of a large amount of slag melt (slag ratio is 3Д4 and more), that was confirmed, for example, in melting out of titanium slag from ilmenite concentrate.
Tsykulenko K.A., Fedorovsky B.B. and Tsykulenko A.K. Application of bimetal and refractory materials in ESR mould designs 14
Feasibility of increase in ESR mould service life is considered, factors influencing the fracture resistance of copper water-cooled mould walls and ways of its improvement are analyzed. New designs of current-carrying ESR moulds using bimetal and refractory materials, in selection of which the type of material being remelted should be taken into account, are described.
ELECTRON BEAM PROCESSES
Akhonin S.V., Milenin A.S. and Pikulin A.N. Modeling of processes of evaporation of alloying elements in EBSM of cylindrical ingots produced from Ti-base alloys 17
Mathematical model of evaporation of alloying elements in electron beam surface melting (EBSM) of ingots produced from titanium-base alloys has been developed. In the scope of the offered model the dependencies of chemical composition of the ingot melted zone on power of electron beam guns and angular rate of ingot rotation were obtained. Adequacy of the model was confirmed by experimental data obtained in surface melting of cylindrical ingots produced from alloy Ti-6Al-4V.
PLASMA-ARC TECHNOLOGY
Zhadkevich M.L., Shapovalov V.A., Torkhov G.F., Nikitenko Yu.A. and Burnashev V.R. Investigation of technological parameters of plasma-arc heating in melting and spinning of melt 22
Effect of main technological parameters of plasma-arc skull melting on distribution of temperature in melt was studied. The change in temperature of a ceramic nozzle of OP-133 unit in the process of melt spinning was determined.
Shapovalov V.A., Melnik G.A., Zhirov D.M., ZhdanovskyA.A. and Tsykulenko K.A. Towards the plasma liquid-phase reduction of iron from oxide raw material 25
Scheme of plasma liquid-phase reduction of iron from its oxides has been offered. It is shown that the content of sulphur and phosphorus in the ready product is several times lower than the admissible content for pig iron.
Najdek V.L. and Narivsky A.V. Technological process of vacuum-plasma treatment of metallic melts 28
Results of investigation of effect of vacuum-plasma treatment of molten metal on effectiveness of refining, structure and strength characteristics of aluminium alloys are presented.
VACUUM-INDUCTION MELTING
Rudoj A.P., Zhuchenko L.P., Melnik V.Kh. and PortnovA.P. Effect of rhenium on properties of high-purity chromium and its alloys with lanthanum 30
Using induction and arc methods the ingots of chromium-lanthanum alloys with rhenium additions were melted in furnaces with copper crucibles and moulds. Hardness and transition temperature of these alloys were investigated. It is shown that hardness of chromium alloys with lanthanum at 0.10Д0.13 wt.% of rhenium is decreased to 1140 MPa, while at 0.46 wt.% it is increased up to 1235 MPa. Transition temperature is increased from 20 to 180 °C with increase in rhenium concentration up to 4.0 wt.%.
ENERGY AND RESOURCE SAVING
Zhadkevich A.M. Brazing of defects of aircraft and ship turbine blades Е challenging technology of extension of their life (Retrospective analysis of status and prospects of development) 33
Retrospective analysis of status and prospects of development of brazing of parts of a gas turbine engine hot path is given. Problems of selection of heat-resistant alloys for turbine blades are shown. Methods of manufacture of cast blades are described. Volumes of possible repair works using brazing of blades are shown on the examples of three construction companies. History of brazing development is presented. Application of new brazing filler alloys is grounded. Methods of brazing of blades and parts of GTE are described and prospects of implementation of technologies in the sphere of repair manufacturing and their effectiveness are described.
Lakomsky V.I. and Tsybulkin G.A. Analytical model of specific resistance of electroconductive bulk material 40
New analytical model of a functional dependence of electric resistance of bulk mixture on sizes of its particles has been offered. Results of experimental check-out of the produced model for the estimation of external specific resistance of a crushed thermoanthracite are given.
Petrov B.F. Throttling of coal charge flow in electric calcinator 43
Situation has been considered which was occurred in operation of electric calcinators IET-10-UkhLD-4 of PA "Sibelectroterm" at Dneprovsky electrode plant of OJSC "Ukrgrafit". Some results of joint work of the plant and E.O. Paton Electric Welding Institute of the NAS of Ukraine, which have led to the creation of almost new furnace having no drawbacks of the old design, are described briefly. The full movement of thermoanthracite in it is ensured and the second adjustable source of heating of all the coal charge is created.
(You are viewing the simplified file contents)