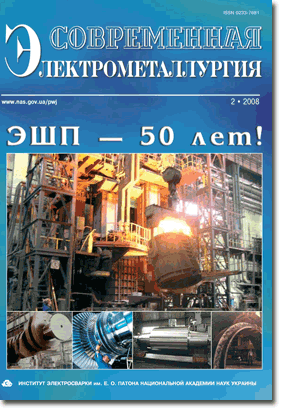
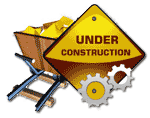
ESR is 50 years! 2 ELECTROSLAG TECHNOLOGY
Mitchell A. Solidification of metal in remelting processes 3
The two remelting processes of electroslag and vacuum arc remelting are widely used in industry for the manufacture of high quality steels, superalloys and titanium alloys. Originally employed for refining, they are now used principally as solidification controlling steps in ingot manufacture. Since the boundary conditions of the process can be readily measured, many attempts have been made to model the ingot solidification. In this work we review the models and indicate their success in application. We conclude that although the present CFD models have greatly assisted in our understanding of the basic processes, as yet they are insufficient to describe the detail required for useful application in industry.
Protokovilov I.V. Electroslag melting of halogenide oxygen-free fluxes 12
It is proposed to perform melting of halogenide oxygen-free fluxes by electroslag method in a copper water-cooled mould with application of a non-consumable titanium electrode. It is shown that forced rotation of the pool melt by means of a longitudinal external magnetic field intensifies melting of the charge and allows increasing productivity of the flux melting process.
ELECTRON BEAM PROCESSES
Zhuk G.V. On influence of metal heating power distribution in mould in EBCHM process on structure of titanium ingots 15
Prospects of producing large-sized (more than 1 m diameter) ingots of titanium alloy using method of electron beam cold hearth melting have been substantiated. The experimentally confirmed calculation data are presented, which prove influence of temperature conditions in the mould on structure of the ingots. Technological conditions, which enable achievement of improved structure of titanium ingots, have been established.
Ustinov A.I., Olikhovskaya L.A., Melnichenko T.V., Shishki A.E. and Matvienko Ya.I. Solid-phase reactions in heating of multilayer Al/Ti foils produced by electron beam deposition method 19
Structural transformations proceeding in heating of thick multilayer Al/Ti foils, produced by electron beam layer-by-layer deposition of components from the vapor phase, have been studied using methods of differential thermal analysis, X-ray diffraction methods, and scanning electron microscopy. By means of temperature increase from 350 to 650 °C successive formation of intermetallic compounds of Al--Ti system, enriched with titanium, occurs in the foil. At all stages of transformation (up to 650 °C) structure of the foil is heterophase one.
Mogilnikova T.G., Nerodenko L.M. and Movchan B.A. Interaction of structure, microscopic limit of elasticity and internal friction of composite materials produced by methods of electron beam technology 27
Results of determination of microscopic limit of elasticity and characteristics of internal friction of pure metals and dispersion-strengthened and microlayer materials, produced by methods of electron beam evaporation and condensation in vacuum, are presented. Existence of non-monotonous dependence of the energy dissipation characteristics and microscopic limit of elasticity upon a structure, formed in the process of production and subsequent processing of the material, is established.
PLASMA-ARC TECHNOLOGY
Zhadkevich M.L., Shapovalov V.A., Melnik G.A., Torkhov G.F., Zhirov D.M., Vislobokov O.M., Prikhodko M.S., Revyakin E.Yu. and Peshkov A.N. Investigation of electric arc under conditions of its interaction with air-pulverized coal mixture 32
Electric and energy parameters of three-phase system of AC arcs within wide range of technological conditions of air plasma conversion of the pulverized-coal fuel were investigated. Composition of the gas, formed in the process of conversion, was determined. It was revealed that to increase combustion heat of the converted gas (increase of hydrogen content and reduction of nitrogen content in mixture of the withdrawn from plasma reactor gases) it is necessary to perform air-vapor plasma conversion of the pulverized-coal fuel.
VACUUM-INDUCTION MELTING
Shejko I.V., Shapovalov V.A. and Yakusha V.V. Induction melting in sectional mould, its possibilities and prospects of application for production of cast items 38
Peculiarities of the melting process in a sectional mould with application of an induction source of heating, possible methods of molten metal accumulation in a sectional mould and its casting are considered. Ways of intensification of the molten metal melting and overheating and possible assortment of cast items are shown.
GENERAL PROBLEMS OF METALLURGY
Grigorenko G.M., Pomarin Yu.M. , Orlovsky V.Yu., Lakomsky V.V., Kalinyuk N.N. and Alekseenko I.I. On dissolution of TiN solid particles in molten titanium during melting 45
Interaction of molten titanium with crucible from titanium nitride at temperatures 2000 and 2100 °C was investigated. It is shown that at these temperatures occurs intensive interaction of the crucible material with the molten pool. The results obtained give basis to assume possibility of dissolution of the titanium nitride solid particles in the molten titanium.
Pomarin Yu.M. , Khizhnyak V.G., Degula A.I. and Smiyan O.D. Diffusion complex coatings with addition of titanium on hard VK8 and T15K6 alloys 48
Results of investigation of phase and chemical compositions, structure and microhardness of the carbide-base complex coatings with addition of chromium, nitrogen and oxygen on hard VK8 and T15K6 alloys are presented. It is shown that depending upon the method of diffusion saturation multilayer carbide (Cr23C6, TiC) or carbooxide (TiC, TixO) coatings are formed on surface of hard alloys. It is established that stability of multifaceted non-resharpenable plates with complex coatings increases in cutting in comparison with the serial ones 1.4--1.5 times.
ENERGY AND RESOURCE SAVING
Kostyakov V.N., Poletaev E.B., Grigorenko G.M., Filozof V.N. and Shevchuk E.A. Influence of technological factors on economic parameters of liquid-phase reduction 52
Results of influence of content of oxide materials in a charge on economic parameters of a melt are presented. It is analytically proved that the main factor, which exerts influence on additional costs in liquid-phase reduction, is content of metal oxides in the charge.
Developed at PWI 18, 31, 51
(You are viewing the simplified file contents)