2013 №07 (03) | 2013 №07 (05) |
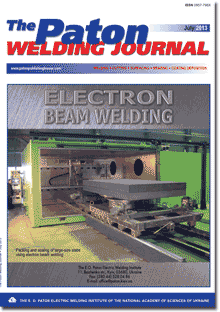
The Paton Welding Journal, 2013, #7, 24-30 pages
MAGNETRON-SPUTTERED NANOCOMPOSITE nc-TiC/a-C COATINGS
Yu.S. BORISOV1, M.V. KUZNETSOV1, A.V. VOLOS1, V.G. ZADOYA1, L.M. KAPITANCHUK1, V.V. STRELCHUK2, V.P. KLADKO2 and V.F. GORBAN3
1E.O. Paton Electric Welding Institute, NASU. 11 Bozhenko Str., 03680, Kiev, Ukraine. E-mail: office@paton.kiev.ua2V.E. Lashkaryov Institute of Semiconductor Physics, NASU. 41 Nauka Ave., 03028, Kiev, Ukraine. E-mail: info@isp.kiev.ua
3I.M. Frantsevich Institute of Problems of Materials Science, NASU. 3 Krzhizhanovsky Str., 03142, Kiev, Ukraine. E-mail: root@ipms.kiev.ua
Abstract
One of the main directions in current progress of surface engineering is development of a nanocomposite structure, with at least one phase with less than 100 nm size of structural element among its components. Presence of a multiphase structure with dissimilar grain boundaries creates a barrier for their coarsening, thus providing stability of the formed coating structure. This work is devoted to investigation of the process of formation of a nanocomposite nc-TiC/a-C coating on substrates from 08Kh18N10T, Kh12M steels and VT1-0 titanium by the method of magnetron sputtering of graphite and titanium targets. In order to control the coating composition, a design procedure was developed, which envisages a change of power of magnetron discharge with titanium target at constant power of discharge with graphite target, that would allow producing coatings in the range of compositions of 42.5-70 at.% C and 57.5-30 at.% Ti. Coatings were studied by the methods of X-ray diffraction, Raman spectroscopy, X-ray photoelectron spectroscopy and microindentation. It is established that nanocrystalline TiC phase takes up 80 % and amorphous carbon matrix is 20 % of the coating structure. It is found that the degree of carbon ordering depends on coating composition. It is shown that the size of TiC grain and coating hardness depend on Ti/C ratio. Minimum size of TiC grain (2.9-4.3 nm) and maximum hardness (up to 30-38 GPa) are achieved at Ti/C ratio (in at.%) of 46/54. Maximum normalized hardness H/E* = 0.134, which is the characteristic of coating material resistance to plastic deformation, is achieved on the substrate of 08Kh10N10T steel. 19Ref., 3 Tables, 7 Figures.
Keywords: nanocomposite coating, magnetron sputtering, titanium carbide, amorphous carbon, grain size, structure, hardness
Received: 28.05.13
Published: 28.07.13
References
1. Andrievsky, R.A. (2001) Nanostructural materials: State, development and prospects. Poroshk. Metallurgiya, 6, 5-11.
2. Andrievsky, R.A., Glezer, A.M. (1999) Dimensional effects in nanocrystalline materials. Pt 1: Peculiarities of structures. Thermodynamics. Kinetic phenomena. Fizika Metallov i Metallovedenie, 88(1), 50-73.
3. Andrievsky, R.A., Glezer, A.M. (2000) Dimensional effects in nanocrystalline materials. Pt 2: Mechanical and physical properties. Ibid., 89(1), 91-112.
4. Ragulya, A.V., Skorokhod, V.V. (2007) Consolidated nanostructural materials. Kiev: Naukova Dumka.
5. Reshetnyak, E.N., Strelnitsky, V.E. (2008) Synthesis of reinforced nanostructural coatings. In: Voprosy Atomnoj Nauki i Tekhniki. Series Physics of radiation damages and radiotive materials sci., 92(2), 119-130.
6. Shtansky, D.V., Levashov, E.A. (2009) Multicomponent nanostructural thin films: Problems and solutions (Review). Izvestiya Vuzov. Tsv. Metallurgiya, 9, 12-15.
7. Veprek, S., Zhang, R.F., Veprek, M.J.G. et al. (2010) Superhard nanocomposites: Origin of hardness enhancement properties and applications. Surf. and Coat. Technol, 204, 1898-1906.
8. Zhang, S., Sun, D., Fu, Y. et al. (2003) Recent advances of superhard nanocomposite coatings: a review. Ibid., 167, 113-119.
9. Zehnder, T., Patscheider, J. (2000) Nanocomposite TiC/a-C:H hard coatings deposited by reactive PVD. Ibid., 133/134, 138-144.
10. Voevodin, A.A., Zabinski, J.S. (2000) Supertough wear-resistant coating with «chameleon» adaptation. Thin Solid Films, 370, 223-231.
11. Galvan, D., Pei, Y.T., de Hosson, J.Th. (2006) Influence of deposition parameters on the structure and mechanical properties of nanocomposite coatings. Surf. and Coat. Technol., 201, 590-598.
12. Patscheider, J., Zehnder, T., Dieseren, M. (2001) Structure-performance relations in nanocomposite coatings. Ibid., 146/147, 201-208.
13. Stuber, M., Leiste, H., Ulrich, S. (2002) Microstructure and properties of low friction TiC-C nanocomposite coatings deposited by magnetron sputtering. Ibid., 150, 218-226.
14. Martinez-Martinez, D., Lopez-Cartes, C., Fernandez,A. (2009) Influence of microstructure on the mechanical and tribological behavior of TiC/a-C nanocomposite coatings. Thin Solid Films, 517, 1662-1671.
15. Sanchez-Lopez, J.C., Martinez-Martinez, D., Abad, M.D. et al. (2009) Metal carbide/amorphous C-based nanocomposite coatings for tribological application. Surf. and Coat. Technol., 204, 947-953.
16. Zhang, S., Lamb Bui, X., Jiang, J. et al. (2005) Microstructure and tribological properties of magnetron sputtered nc-TiC/a-C nanocomposite. Ibid., 198, 206-211.
17. Pei., Y.T., Galvan, D., de Hosson, J.Th. et al. (2005) Nanostructured TiC/a-C coatings for friction and wear resistant applications. Ibid., 198, 44-50.
18. Firstov, S.A., Gorban, V.F., Pechkovsky, E.P. (2009) New methodology of processing and analysis of results of automatic material indentation. Kiev: Logos.
19. Ferrari, A., Robertson, J. (2000) Interpretation of Raman spectra of disordered and amorphous carbon. Phys. Rev. B, 61(20), 14095-14107.