2014 №05 (05) |
DOI of Article 10.15407/tpwj2014.05.06 |
2014 №05 (07) |
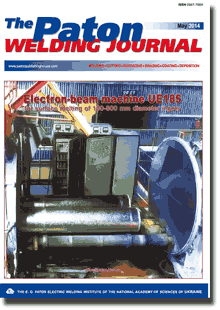
The Paton Welding Journal, 2014, #5, 33-39 pages
TECHNOLOGICAL PECULIARITIES OF LASER, MICROPLASMA AND HYBRID LASER-MICROPLASMA WELDING OF ALUMINIUM ALLOYS
V.D. SHELYAGIN1, A.M. ORISHICH2, V.Yu. KHASKIN1, A.G. MALIKOV2 and A.A. CHAJKA1
1E.O. Paton Electric Welding Institute, NASU. 11 Bozhenko Str., 03680, Kiev, Ukraine. E-mail: office@paton.kiev.ua
2S.A. Khristianovich Institute of Theoretical and Applied Mechanics, Siberian Branch of RAS. 4/1 Institutskaya Str., 630090, Novosibirsk, Russia. E-mail:admin@itam.nse.ru
Abstract
Actuality of application of laser, microplasma and hybrid laser-microplasma (HLMP) methods of aluminium alloys welding is shown. Technological schemes of laser and laser-microplasma welding are selected. Appropriate experiments have been carried out for study of technological peculiarities of three selected methods for producing butt and edge sheet joints. It was found that there are the following main drawbacks in microplasma welding: in case of complete penetration a weld sagging is observed, at welding currents of more than 30 A the tendency to undercut formation takes plase, with increase in speed for more than 40m/h the stability of process is decreased. It is characteristic of HLMP welding: stability of the process at high (above 60 m/h) speeds of welding, decrease (by 1.5-2 times as compared with microplasma welding) in width of welds, significant decrease (up to full removal) in residual deformations, absence of spattering. It was found that typical defects of laser and laser-microplasma welding of are the sagging of welds, made without backing, formation of undercuts and inner pores of 0.1-0.2 mm diameter. The following main ways of elimination of these defects can be taken into consideration: feeding of filler materials (for example, in the form of wire); use of steel backings (including those with grooves for lower bead formation); welding along raised edge (with edge welds); application of welding modes with modulation of sources power; overlap welding (requires careful preparation of surfaces). Optimum values of energy input in CO2-laser welding are 36-70 J/mm by the criteria of quality of joints formation, absence of pores and cracks. Reduction of energy input leads to disappearance of key hole and lack of penetration of metal, while increase in energy input - to hot crack formation. Typical macro- and microstructure of metal of welds and HAZ made by microplasma, hybrid and laser welding are given. 7 Ref., 11 Figures.
Keywords: welding, aluminium alloys, laser emission, microplasma, hybrid laser-microplasma welding, types of joints, experiments, modes, structures
Received: 07.02.14
Published: 28.05.14
References
1. Paton, B.E., Gvozdetsky, V.S., Dudko, D.A. et al. (1979) Microplasma welding. Kiev: Naukova Dumka.
2. Paton, B.E., Gvozdetsky, V.S., Krivtsun, I.V. et al. (2002) Hybrid laser-microplasma welding of thin sections of metals. The Paton Welding J., 3, 2-6.
3. Bondarev, A.A., Bondarev, Andr. A. (2001) Laser welding of aluminium alloys (Review). Ibid., 12, 19-25.
4. Krivtsun, I.V., Shelyagin, V.D., Khaskin, V.Yu. et al. (2007) Hybrid laser-plasma welding of aluminium alloys. Ibid., 5, 36-40.
5. Afonin, Yu.V., Golyshev, A.P., Ivanchenko, A.I. et al. (2004) Generation of radiation with quality of TEM00 mode in continuous CO2-laser of 8 kW power. Kvant. Elektronika, 31(4), 307-310. https://doi.org/10.1070/QE2004v034n04ABEH002671
6. Rabkin, D.M. (1986) Metallurgy of fusion welding of aluminium and its alloys. Kiev: Naukova Dumka.
7. Kovalenko, V.S. (1981) Metallographic reagents: Refer. Book. 3rd ed. Moscow: Metallurgiya.