2016 №10 (03) |
DOI of Article 10.15407/tpwj2016.10.04 |
2016 №10 (05) |
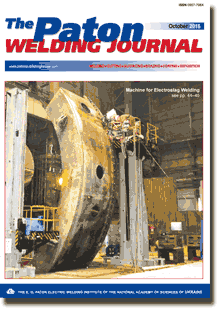
The Paton Welding Journal, 2016, #10, 20-25 pages
Influence of high-frequency mechanical vibrations of the item on structure and wear resistance of Kh10R4G2S deposited metal
G.V. Pokhmurskaya1, M.M. Student2, A.A. Vojtovich3, A.Z. Student2 and A.R. Dzyubik
1Technical University of Chemnitz 09107, Chemniz. E-mail: pokhmurska@mb.tu-chemnitz.de
2G.V. Karpenko Physico-Mechanical Institute, NASU 5 Nauchnaya Str., 79601, Lviv, Ukraine. E-mail: student-m-m@ipm.lviv.ua
3«Lviv Polytechnic» National University 12 Stepan Bandera Str., 79013, Lviv, Ukraine. E-mail: andrsibox@gmail.com
Abstract
The paper presents the results of studies of the effect of high-frequency (100 Hz) mechanical vibrations on microstructure and wear resistance of metal, deposited with PP Kh10R4G2S wire and OSTs45M flux. It established that when horizontal vibration is used, deposited metal solid solution, uniformly saturated with fine iron-chromium borides (FeCr)B, prevails in the structure. Homogeneous structure improves wear resistance by 2.0–2.5 times. 9 Ref., 1 Table, 5 Figures.
Keywords: surfacing, flux-cored wire, vibration, microstructure, fatigue life, wear pattern
Received: 11.03.16
Published: 23.10.16
References
1. Zhou, Y., Yang, Y., Qi, X. et al. (2012) Influence of La2O3 addition on microstructure and wear resistance of Fe–Cr–C cladding formed by arc surface welding. J. of Rare Earths, 30(10), 1069. https://doi.org/10.1016/s1002-0721(12)60180-x
2. Yuksel, N., Sahin, S. (2014) Wear behavior-hardness-microstructure relation of Fe–Cr–C and Fe–Cr–C–B based hardfacing alloys. Materials and Design, 58, 491–498. https://doi.org/10.1016/j.matdes.2014.02.032
3. Katsicha, C., Badisch, E., Manish, R. et al. (2009) Erosive wear of hardfaced Fe–Cr–C alloys at elevated temperature. Wear, 267, 1856–1864. https://doi.org/10.1016/j.wear.2009.03.004
4. Pokhmurska, G.V., Student, M.M., Lanets, O.S. et al. (2015) Effect of vibration during surfacing of protective layer on its macrostructure and shock-abrasive wear. Fizyko-Khimichna Mekhanika Materialiv, Issue 3.
5. Govindarao, P., Srinivasarao, P., Gopalakrishna, A. et al. (2012) Effect of vibratory welding process to improve the mechanical properties of butt welded joints. Int. J. of Modern Engineering Research (IJMER), 2(Issue 4), 2766–2770.
6. Husein, A.R., Abdul, N.A., Talib, R.A. (2011) Improvement of mechanical welding by using induced harmonic vibration. J. of Applied Sci., 11(2), 348–353. https://doi.org/10.3923/jas.2011.348.353
7. Wanga, S., Li, H., Chenb, X. et al. (2010) Improving microstructure and wear resistance of plasma clad Fe-based alloy coating by a mechanical vibration technique during cladding. Materials Sci. and Engineering, A, 528, 397–401. https://doi.org/10.1016/j.msea.2010.09.021
8. Pulka, Ch.V., Shably, O.N., Senchishin, V.S. et al. (2012) Influence of vibration of parts on structure and properties of metal in surfacing. The Paton Welding J., 1, 23–25.
9. Vojtovich, A.A., Pokhmurska, G.V., Student, M.M. et al. (2015) Peculiarities of formation and fracture of deposited layers from flux-cored wires of Fe–Cr–B–C system at shock loads. Problemy Trybologii, 4, 114–123.