2016 №11 (03) |
DOI of Article 10.15407/tpwj2016.11.04 |
2016 №11 (05) |
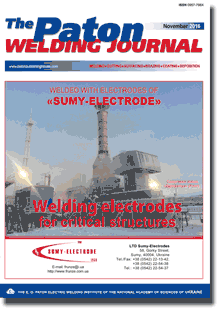
The Paton Welding Journal, 2016, #11, 23-30 pages
Peculiarities of bead shape regulation in single-layer microplasma surfacing on edges of aircraft gas turbine engine blades
P.D. Zhemanyuk1, I.A. Petrik1, S.L. Chigilejchik1, A.V. Yarovitsyn2 and G.D. Khrushchov2
1JSC «Motor Sich» 15 Motorostroiteley Str., 69068, Zaporozhe, Ukraine. E-mail:motor@motorsich.com
2 E.O. Paton Electric Welding Institute, NASU 11 Kazimir Malevich Str., 03680, Kiev, Ukraine. E-mail: office@paton.kiev.ua
Abstract
It is a necessary to specify the dependencies of deposited metal shaping due to the need of 5–15 mm height increase of the dimensions of surfacing-repaired damaged areas of blade edges of aircraft GTE of high-temperature nickel alloys in microplasma bead surfacing on narrow substrate of less than 3 mm. A range of change of the process energy indices in «effective heat power of arc–heat input–cross-section area of deposited bead» system was investigated for conditions of corresponding single-layer surfacing, and effectiveness of process regulation of deposited layer cross-section was evaluated. It is determined that heat input change in 100–1600 J/mm range is the most effective regulation of cross-section area of the deposited bead under conditions of base metal limited penetration depth. It is assumed that the determined process relationship between heat input energy, height and cross-section area of the deposited bead will promote for formation of the additional criteria preventing crack formation in the «base–deposited metal» welded joint in repair of the parts of aircraft engines of high-temperature nickel alloys using multi-layer microplasma powder surfacing. 18 Ref., 4 Tables, 8 Figures.
Keywords: microplasma powder surfacing, high-temperature nickel alloy and heat-resistant cobalt alloy, narrow substrate, effective heat power of arc, heat input, thermal efficiency, cross-section area of deposited bead
Received: 06.07.16
Published: 14.12.16
References
- Gladky, P.V., Pereplyotchikov, E.F., Ryabtsev, I.A. (2007) Plasma surfacing. Kiev: Ekotekhnologiya.
- Peremilovsky, I.A., Gejchenko, V.S., Frumin, I.I. (1976) Surfacing repair of turbine blades of aircraft engines. Svarka, 5, 54–56.
- Petrik, I.A., Peremilovsky, I.A. (2001) Further development of technology for hardening of flange platform faces of turbine blades from high-temperature alloys. Tekhnologicheskie Sistemy, 3, 90–92.
- Yarovytsyn, O.V. (2009) Microplasma powder surfacing of high-temperature nickel alloys containing 45–65 % of γ-phase: Syn. of Thesis for Cand. of Techn. Sci. Degree. Kiev: PWI.
- (2010) Technological Seminar Deloro Stellite in Zaporozhie. The Paton Welding J., 1, 46–49.
- Yushchenko, K.A., Savchenko, V.S., Yarovitsyn, A.V. et al. (2010) Development of the technology for repair microplasma powder cladding of flange platform faces of aircraft engine high-pressure turbine blades. Ibid., 8, 21–24.
- Yushchenko, K.A., Yarovitsyn, A.V. (2012) Improvement of technology of repair of upper flange platform faces of aircraft engine blades. In: Complex Program of NASU on Problems of Service Life and Service Safety of Constructions, Structures and Machines. on Results of 2010–2012. Kiev: PWI.
- Zhemanyuk, P.D., Petrik, I.A., Chigilejchik, S.L. (2015) Experience of introduction of the technology of reconditioning microplasma powder surfacing at repair of high-pressure turbine blades in batch production. The Paton Welding J., 8, 39–42. https://doi.org/10.15407/tpwj2015.08.08
- Boguslaev, V.A., Muravchenko, V.M., Zhemanyuk, P.D. et al. (2003) Technological support of service characteristics of gas turbine engine parts. Turbine blades. Pt 2. Zaporozhie: JSC Motor Sich.
- Sorokin, L.I., Lukin, V.I., Bagdasarov, Yu.S. (1997) Weldability of cast high-temperature alloys of ZhS6 type. Proizvodstvo, 6, 12–17.
- Yarovitsyn, A.V. (2015) Energy approach in analysis of microplasma powder surfacing modes. The Paton Welding J., 5/6, 22–25. https://doi.org/10.15407/tpwj2015.06.03
- Popov, S.A. (1987) Grinding operations. Moscow: Vysshaya Shkola.
- Kondratyuk, E.V., Leontiev, V.A., Shusha, A.V. et al. (2013) Profile deep grinding of gas turbine engine parts. Promyshlennost v Fokuse, 5, 22–24.
- Yushchenko, K.A., Yarovitsyn, A.V., Khrushchov, G.D. et al. (2015) Analysis of process of bead shaping in cladding on narrow substrate. The Paton Welding J., 9, 20–27. https://doi.org/10.15407/tpwj2015.09.03
- Wang, H., Jiang, W., Vallant, M. et al. (2003) Microplasma powder deposition as a new solid freeform fabrication process. Inst. Mech. Engrs., 217(Pt B.J.), 1641–1650. https://doi.org/10.1243/095440503772680578
- Suyog Jhavar, Jain, N.K., Paul, C.P. (2014) Development of microplasma transferred arc (µ-PTA) wire deposition process for additive layer manufacturing applications. of Materials Processing Technology, 214(5), 1102–1110. https://doi.org/10.1016/j.jmatprotec.2013.12.016
- Gharbi, M., Peyre P., Gorny, C. et al. (2012) Influence of various process conditions on surface finishes induced by direct metal deposition laser technique on a Ti–6Al–4V alloy. , 213(5), 791–800.
- (1988) Mathematical dictionary. Ed. by Yu.V. Prokhorov. Moscow: Sovremennaya Encyclopediya.