2018 №12 (03) |
DOI of Article 10.15407/tpwj2018.12.04 |
2018 №12 (05) |
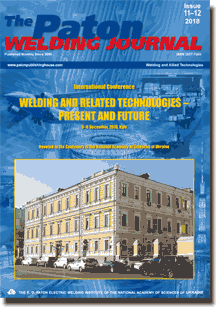
The Paton Welding Journal, 2018, #11-12, 41-51 pages
Journal The Paton Welding Journal
Publisher International Association «Welding»
ISSN 0957-798X (print)
Issue #11-12, 2018 (November)
Pages 41-51
Thin-walled welded transformable-volume structures of space purpose
L.M. Lobanov and V.S. Volkov
E.O. Paton Electric Welding Institute of the NAS of Ukraine 11 Kazimir Malevich Str., 03150, Kyiv, Ukraine. E-mail: office@paton.kiev.ua
The rational methods of construction of metal transformable shells with the aim of creation of the space-purpose structures were investigated. The mathematical modeling of the neutral shell surface movement of the transformable-volume structure (TVS) was performed, the result of which was used to set the reference surface at the kinematic modeling of its stress-strain states during a compact folding. The parameters of the process of welding thin shells of stainless steel were determined, guaranteeing the maximum approaching of physicomechanical properties of welded joints to similar properties of the base metal, thus providing their vacuum density. The methods of surface modification of thin metal shells of stainless steel, which allow improving the safety margin of TVS of space purpose without changing their mass and compactness were developed. The possibility was experimentally confirmed and the conditions of stability of complete reverse transformation of a multisectional conical-type TVS were formulated. 7 Ref., 12 Figures.
Keywords: deployable structures, thin shells, microplasma welding, microstructure and weld metal, surface engineering
Received: 26.10.18
Published: 23.11.18
References
1. (2017) Bigelow Aerospace. The Bigelow Expandable Activity Module (BEAM). https://bigelowaerospace/com/pages/beam/
2. Viquerat, A., Schenk, M., Sanders, B., Lappas, V.J. (2014) Inflatable rigidisable mast for end-of-life deorbiting system. In: Proc. of Europ. Conf. on Spacecraft Structures, Materials and Environmental Testing (SSMET) 2014 (April 1-4, 2014, Braunschweig, Germany).
3. Paton, B.E., Samilov, V.N., Gonchar, O.Yu. et al. (1999) Transformable all-welded metal structures. Avtomatich. Svarka, 10, 81-85 [in Russian].
4. Paton, B.E., Lobanov, L.M., Samilov, V.N. et al. (2006) Design and features of fabrication technology of a large-sized transformable shell structure. The Paton Welding J., 7, 2-10.
5. Lobanov, L.M., Volkov, V.S. (2015) Peculiarities in manufacture of thin-walled welded transformable-volume structures for space application. Ibid., 1, 29-34. https://doi.org/10.15407/tpwj2015.01.05
6. Lobanov, L.M., Volkov, V.S., Yakimkin, A.V., Savitsky, V.V. (2016) Functional characteristics improvement of metal transformable-volume structures for space applications. J. of Aerospace Technol. and Management, 8, 55-62. https://doi.org/10.5028/jatm.v8i1.529
7. Ario, I., Watson, A. (2009) Structural stability of multi-folding structures with contact problem. J. of Sound and Vibration, 1-2, 263-282. https://doi.org/10.1016/j.jsv.2009.01.057