2021 №01 (05) |
DOI of Article 10.37434/tpwj2021.01.06 |
2021 №01 (07) |
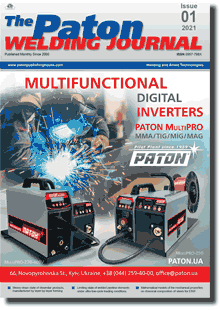
The Paton Welding Journal, 2021, #1, 29-34 pages
Numerical analysis of the features of limiting state of welded pipeline elements under ultra-low-cycle loading conditions
O.V. Makhnenko, O.S. Milenin, O.A. Velykoivanenko, G.P. Rozynka and N.I. Pivtorak
E.O. Paton Electric Welding Institute of the NASU. 11 Kazymyr Malevych Str., 03150, Kyiv, Ukraine. E-mail: office@paton.kiev.ua
Abstract
Expert analysis of the reliability and performance of welded pipelines with detected corrosion-erosion damage under ultra-low-cycle loading requires taking into account several interrelated physicomechanical phenomena, which determine the limiting state of a specific structure. For this purpose, integrated numerical procedure was developed in this study for finite-element assessment of subcritical fracture accumulation and prediction of the limiting state of typical pipelines with 3D defects of wall thinning. The ductile mechanism of subcritical fracture was considered as the main one. Moreover, material hardening and softening at plastic deformation (strain hardening, Bauschinger effect) was taken into account. This integrated approach allowed revealing the main regularities of failure of a typical pipeline element, depending on external loading. 14 Ref., 7 Figures.
Keywords: welded pipeline, corrosion-erosion defect, ultra-low-cycle loading, Bauschinger effect, ductile fracture, limiting state
Received 30.11.2021
References
1. (2004) Recommended Practice, DNV-RP-F101. Corroded Pipelines. Edited by O. Bjornoy. Hovik, Det Norske Veritas..2. Hertelé, S., Cosham, A., Roovers, P. (2016) Structural integrity of corroded girth welds in vintage steel pipelines. Engineering Structures, 124, 429-441. https://doi.org/10.1016/j.engstruct.2016.06.045
3. Milenin, A., Velikoivanenko, E., Rozynka, G., Pivtorak, N. (2019) Probabilistic procedure for numerical assessment of corroded pipeline strength and operability. Int. J. of Pressure Vessels and Piping, 171, 60-68. https://doi.org/10.1016/j.ijpvp.2019.02.003
4. Morin, L., Michel, J.-C., Leblond, J.-B. (2017) A Gurson-type layer model for ductile porous solids with isotropic and kinematic hardening. Int. J. of Solids and Structures, 118-119, July, 167-178. https://doi.org/10.1016/j.ijsolstr.2017.03.028
5. Chun, B.K., Jinn, J.T., Lee, J.K. (2002) Modeling the Bauschinger effect for sheet metals, part I: theory. International J. of Plasticity, 18, 571-595. https://doi.org/10.1016/S0749-6419(01)00046-8
6. Xue, L. (2008) Constitutive modeling of void shearing effect in ductile fracture of porous materials. Engineering Fracture Mechanics, 75, 3343-3366. https://doi.org/10.1016/j.engfracmech.2007.07.022
7. Chen, Z., Butcher, C. (2013) Micromechanics Modelling of Ductile Fracture. Dordrecht, Springer Netherlands. https://doi.org/10.1007/978-94-007-6098-1
8. Makhnenko, V. (2013) Problems of examination of modern critical welded structures. The Paton Welding J., 5, 21-28.
9. Zhang, Z.L. (2001) A complete Gurson Model. Nonlinear Fracture and Damage Mechanics. Edited by M. H. Alibadi. UK, WIT Press Southampton, 223-248.
10. Velikoivanenko, E., Milenin, A., Popov, A. et al. (2019) Methods of numerical forecasting of the working performance of welded structures on computers of hybrid architecture. Cybernetics and Systems Analysis, 55, 1, 117-127. https://doi.org/10.1007/s10559-019-00117-8
11. Cowper, G.R., Symonds, P.S. (1958) Strain Hardening and Strain Rate Effects in the Impact Loading of Cantilever Beams. Brown Univ, Applied Mathematics Report. https://doi.org/10.21236/AD0144762
12. Lemaitre, J., Chaboche, J.-L. (1990) Mechanics of Solid Materials. Cambridge, Cambridge University Press. https://doi.org/10.1017/CBO9781139167970
13. Makhnenko, V.I. (2006) Safe service life of welded joints and assemblies of modern structures. Kiev, Naukova Dumka [in Russian].
14. Milenin, O. (2017) Numerical prediction of the current and limiting states of pipelines with detected flaws of corrosion wall thinning. J. of Hydrocarbon Power Engineering, 4, 1, 26-37.