2021 №11 (06) |
DOI of Article 10.37434/tpwj2021.11.07 |
2021 №11 (08) |
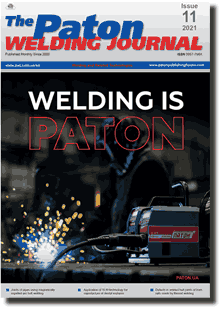
The Paton Welding Journal, 2021, #11, 38-47 pages
Composite powders based on FeMoNiCrB amorphizing alloy with additives of refractory compounds for thermal spraying of coatings
Yu.S. Borysov1, A.L. Borysova1, O.M. Burlachenko1, T.V. Tsymbalista1, M.A. Vasylkivska2, E.G. Byba3
1E.O. Paton Electric Welding Institute of the NASU. 11 Kazymyr Malevych Str., 03150, Kyiv, Ukraine. E-mail: borisov@paton.kiev.ua
2I.M. Frantsevich Institute for Problems of Materials Science of the NASU 3 Krzhizhanovskiy Str., 03142, Kyiv
3E.O. Paton Institute of Materials Science and Welding of “Igor Sikorsky Kyiv Polytechnic Institute” 37 Peremohy Ave., 03056, Kyiv, Ukraine
Abstract
The process of producing by mechanical alloying method composite powders based on FeMoNiCrB amorphizing alloy with additives of refractory compounds (ZrB2, (Ti,Cr)C and FeTiO3) by processing a mixture of powder components in planetary mill “Activator 2SL” was studied. It was found that after 1.5 h of processing its products are homogeneous conglomerates with average particle size, depending on the composition of composite powders, which was 23 μm in the case of FeMoNiCrB + ZrB2, 15 μm in the case of FeMoNiCrB+(Ti, Cr)C, and 25 μm in the case of FeMoNiCrB + FeTiO3. XRD analysis results reveal formation of an amorphous-nanocrystalline structure in the produced composite powders, which consists of Fe(Ni, Cr), Mo2FeB2 solid solution and disperse phase of additives of refractory compounds (ZrB2, (Ti, Cr)C and FeTiO3) with indications of certain interphase interaction of FeMoNiCrB and (Ti, Cr)C. Here, the amorphous phase appears as a result of the process of mechanical alloying. The values of measured microhardness in the composite powders were as follows: FeMoNiCrB + ZrB2 – 6.2±1.6 MPa, FeMoNiCrB + (Ti, Cr)C – 5.5±1.1 MPa, FeMoNiCrB‒FeTiO3 – 5.1±0.7 MPa. For application in thermal spraying of coatings with an amorphous structure, the produced composite powders from mechanical alloying products are used to form conglomerate powders with particle size and degree of flowability, meeting the requirements of thermal spray coating technology.
Keywords: amorphizing alloy, refractory compounds, composite powder, mechanical alloying, structure, phase composition, granulometric composition
Received 05.08.2021
Accepted: 29.11.2021
References
1. Suzuki, K., Fujimori, H., Hasimoto, K. (1987) Amosphous metals. Ed. by Ya.I. Polyak, B.I. Kekalo. Moscow, Metallurgiya [in Russian].2. Kunitsky, Yu.A., Korzhik, Yu.S. (1988) Noncrystalline metal materials and coatings in engineering. Kiev, Tekhnika [in Russian].
3. Kalita, V.I., Komlev, D.I. (2008) Plasma coatings with nanocrystalline and amorphous structure. Moscow, Lider M [in Russian].
4. Yongjiang, H., Yuanzhi, G., Hongbo, F., Jun, S. (2012) Synthesis of Fe-Cr-Mo-C-B amorphous coating with high corrosion resistance. Materials Letters, 89, 229-232. https://doi.org/10.1016/j.matlet.2012.08.114
5. Terajima, T., Takeuchi, F., Nakata, K. et al. (2010) Composite coating containing WC/12Co cermet and Fe-based metallic glass deposited by high-velocity oxygen fuel spraying. J. of Alloys and Compounds, 504(1), 288-291. https://doi.org/10.1016/j.jallcom.2010.03.209
6. Yugeswaran, S., Kobayashi, A., Suresh, K., Subramanian, B. (2013) Characterization of gas tunnel type plasma sprayed TiN reinforced Fe-based metallic glass coatings. Ibid., 551, 168-175. https://doi.org/10.1016/j.jallcom.2012.09.111
7. Movahedi, B. (2018) Mechanical investigation approach to optimize the high-velocity oxygen fuel Fe-based amorphous coatings reinforced by B4C nanoparticles. World Academy of Sci., Engineering and Technology Int. J. of Materials and Metallurgical Engineering, 12(9), 460-465. DOI: https://doi. org/10.5281/zenodo.1474539'); ?>
8. Korzhik, V.N., Borisova, A.L., Popov, V.V. et al. (2014) Cermet coatings of chromium carbide-nichrome system produced by supersonic plasma gas air spraying. The Paton Welding J., 12, 23-28. https://doi.org/10.15407/tpwj2014.12.05
9. Borisov, Yu.S., Borisova, A.L., Astakhov, E.A. et al. (2017) Detonation coatings of intermerallic powders of Fe-Al system produced using mechanical alloying. Ibid., 4, 25-31. https://doi.org/10.15407/as2017.04.05
10. Borisov, Yu.S., Borisova, A.L. (1986) Plasma powder coatings. Kiev, Tekhnika [in Russian].
11. Vityaz, P.A., Lovshenko, F.G., Lovshenko, G.F. (1998) Mechanically- doped alloys based on aluminium and copper. Minsk, Belarusskaya Nauka [in Russian].
12. Grigorieva, T.F., Barinova, A.P., Lyakhov, N.Z. (2008) Mechanochemical synthesis in metallic systems. Ed. by E.G. Avvakumov. Novosibirsk, Parallel [in Russian].
13. Lebedeva, S.I. (1977) Microhardness of minerals. Ed. by S.A.Yushko. Moscow, Nedra [in Russian].
14. Surzhenkov, A., Antonov, M., Goljandin, D. et al. (2013) Sliding wear of TiC-NiMo and Cr3C2-Ni cermet particles reinforced FeCrSiB matrix HVOF sprayed coatings. Estonian J. of Engineering, 19(3), 203-211. https://doi.org/10.3176/eng.2013.3.03