2022 №12 (04) |
DOI of Article 10.37434/as2022.12.05 |
2022 №12 (06) |
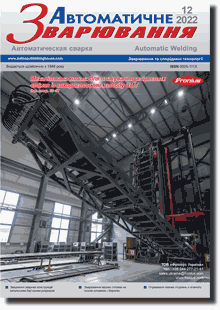
"Avtomatychne Zvaryuvannya" (Automatic Welding), #12, 2022, pp. 38-44
Influence of heat treatment on improvement of mechanical properties of welded joints of sparsely-doped titanium alloy Ti–2.8Al–5.1Mo–4.9Fe
S.V. Akhonin, V.Yu. Bilous, V.A. Kostin, S.G. Hrygorenko, O.L. Puzrin, E.L. Vrzhyzhevskyi
E.O. Paton Electric Welding Institute of the NAS of Ukraine. 11 Kazymyr Malevych Str., 03150, Kyiv, Ukraine. E-mail: office@paton.kiev.uaThe most important advantage of pseudo-β-titanium alloys is their high strength, and the disadvantages include the high cost of alloying elements. Sparsely-doped alloys, such as LCB, Timetal 125, etc. were developed to lower the titanium alloys cost. This class of titanium alloys is promising for application in inexpensive structures. Development of welding technology and modes of heat treatment of such alloy joints is an important task. In this work investigations were performed of the surface of fractures in welded joints of titanium alloy of Ti–2.8Al–5.1Mo–4.9Fe system, obtained after impact toughness testing. It was found that local heat treatment in the vacuum chamber of specimens of welded joints of test titanium alloy Ti–2.8Al–5.1Mo–4.9Fe produced by EBW by mode 4 (LHT in a vacuum chamber at the temperature of 750 °С for 5 min) allows producing higher ductility properties of welded joints, and preventing post-weld cold cracking. Such heat treatment leads to a more uniform arrangement of ductile fracture areas on fracture surfaces. 12 Ref., 3 Tabl., 6 Fig.
Keywords: titanium, pseudo-β-titanium alloys, sparsely-doped titanium alloys, welded joints, welding, electron beam welding, local heat treatment, tungsten electrode, heat treatment, mechanical properties, fractures surfaces, quality criterion
Received: 08.12.2022
References
1. Lütjering, G., Williams, J.C. (2003) Titanium (engineering materials and processes). Berlin, Springer-Verlag, 3. https://doi.org/10.1007/978-3-540-71398-22. (2002) EHKTechnologies: «Opportunities for low cost titanium in reduced fuel consumption, improved emissions, and enhanced durability heavy-duty vehicles», Subcontract 4000013062, EHKTechnologies, Vancouver, WA, USA.
3. Lavender, C.A. (2004) Low-cost titanium evaluation. Pacific Northwest National Laboratory, Richland, WA, USA.
4. (2004) EHKTechnologies: «Summary of emerging titanium cost reduction technologies. A study performed for US Department of Energy and Oak Ridge National Laboratory», Subcontract 4000023694, EHKTechnologies, Vancouver, WA, USA.
5. Nochovnaya, N.A., Antashev, V.G. (2007) Titanium alloys of «LOW-COST» series and possibilities of their application. In: Proc. of Int. Conf. on Ti-2007 in CIS (Kyiv, IMP), 191-192.
6. Bania, P.J. (1993) Beta titanium alloys and their role in the titanium industry. In: Beta Titanium Alloys in the 90`s, TMS Publications, Warrendale, PA, 3-14.
7. Weiss, I., Semiatin, S.L. (1998) Thermomechanical processing of beta titanium alloys on overview. Mat. Sci. Eng. A, 243, 46-65. https://doi.org/10.1016/S0921-5093(97)00783-1
8. Akhonin, S.V., Bilous, V.Yu., Berezos, V.O. et al. (2020) Structure and properties of structural sparcely-doped titanium-based alloys produced by EBM. Suchasna Elektrometal., 4, 7-15 [in Ukrainian]. https://doi.org/10.37434/sem2020.04.02
9. Akhonin, S.V., Belous, V.Yu., Selin, R.V. et al. (2018) Electron beam welding and heat treatment of welded joints of high-strength pseudo-β titanium alloy VT19. The Paton Welding J., 7, 10-14. https://doi.org/10.15407/as2018.07.02
10. Akhonin, S.V., Belous, V.Yu., Selin, R.V. et al. (2021) Influence of heat treatment on the structure and properties of welded joints of high-strength titanium alloys based on β-phase. Suchasna Elektrometal., 4, 51-58 [in Ukrainian]. https://doi.org/10.37434/sem202.04.11
11. Grigorenko, S.G., Taranova, T.G.,Kostin, V.A. et al. (2021) Influence of heat treatment on the structure and fracture mode of welded joints of sparsely-alloyed titanium alloy. Suchasna Elektrometal., 3, 42-48 [in Ukrainian]. https://doi.org/10.37434/sem2021.03.07
12. Fellows, J. (1982) Fractography and atlas of fractograms. Ed. by Bernshtejn, M.L., Moscow, Metallurgiya [in Russian].