2022 №04 (08) |
DOI of Article 10.37434/sem2022.04.01 |
2022 №04 (02) |
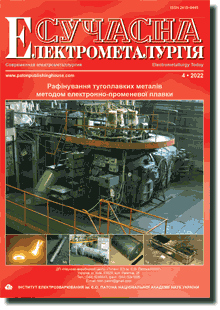
"Suchasna Elektrometallurgiya" (Electrometallurgy Today), 2022, #4, 3-8 pages
Niobium refining by the method of cold-hearth electron beam melting
S.V. Akhonin, V.O. Beresos, O.M. Pikulin, O.O. Kotenko, Yu.T. Ishchuk
E.O. Paton Electric Welding Institute of the NAS of Ukraine. 11 Kazymyr Malevych Str., 03150, Kyiv, Ukraine. E-mail: office@paton.kiev.ua
Abstract
The technology of cold-hearth electron beam melting was used to perform a package of research work to produce quality ingots of high-purity metallic niobium with improved technical and economic parameters of the process. Proceeding from the results of the performed work, it was established that of all the interstitial impurities nitrogen is removed the worst from niobium during cold-hearth electron beam melting. This is the impurity which limits the refining process. Experimental data, obtained during operation, showed that the proposed modes of cold-hearth double electron beam remelting of niobium ensure rather uniform distribution of impurity elements in the ingot volume, whereas their content does not exceed the values specified by the standard requirements. It is found that application of the technology of electron beam melting of the ingot surface ensures removal of defects from the surface layer of niobium ingots, surface roughness being in the range of Rz20…Rz80 at surface relief waviness equal to 0.2…0.6 mm, respectively. Ref. 20, Tabl. 1, Fig. 6.
Keywords: niobium; electron beam melting; cold hearth; ingot; chemical composition
Received 26.09.2022
References
1. Inshewat, Yazan (2020) ECM and EDM of tantalum and niobium alloys for use in the space industry. DOI: https://doi.org/10.13140/RG.2.2.11005.593662. Hebda, John (2001) Niobium alloys and high temperature applications. Niobium Science & Technology: Proc. of Inter. Sym. Niobium, Orlando, Florida, USA.
3. Paul Aimone, Mei Yang (2018) Niobium alloys for the chemical process industry. Inter. J. of Refractory Metals and Hard Materials, 71, 335-339. https://doi.org/10.1016/j.ijrmhm.2017.11.036
4. Ciovati, Gianluigi, Dhakal, Pashupati, Kneisel, P., Myneni, Ganapati (2015) Summary of performance of superconducting radio-frequency cavities built from CBMM niobium ingots. AIP Conf. Proc., 1687, 030001. https://doi.org/10.1063/1.4935322
5. Patel, D., Kim, SH., Qiu, W. et al. (2019) Niobium-titanium (Nb-Ti) superconducting joints for persistent-mode operation. Sci., 9, 14287. https://doi.org/10.1038/s41598-019-50549-7
6. Banno, N., Kobayashi, K., Uchida, A. et al. (2021) High-temperature-tolerable superconducting Nb-alloy and its application to Pb- and Cd-free superconducting joints between NbTi and Nb3Sn wires. J. Mater. Sci., 56, 20197-20207. https://doi.org/10.1007/s10853-021-06585-8
7. Om Pal Singh, Umasankari K. (2021) Chapter 12: Nuclear reactors of the future. Ed. by P. Mohanakrishnan. Physics of Nuclear Reactors. Academic Press, 695-746. https://doi.org/10.1016/B978-0-12-822441-0.00003-0
8. Nikulina, A.V. (2003) Zirconium-niobium alloys for core elements of pressurized water reactors. Metal Sci. and Heat Treatment, 45, 287-292. https://doi.org/10.1023/A:1027388503837
9. Pink, Erwin, Eck, Ralf. (2006) Refractory metals and their alloys. https://doi.org/10.1002/9783527603978.mst0088
10. Lance L. Snead, David T. Hoelzer, Michael Rieth, Andre A.N. Nemith (2019) Chapter 13: Refractory Alloys: Vanadium, niobium, molybdenum, tungsten. Eds by G. Robert Odette, Steven J. Zinkle. Structural Alloys for Nuclear Energy Applications. Elsevier, 585-640. DOI: https://doi.org/10.1016/B978-0-12-397046-6.00013-7
11. Zelikman, A.N., Korshunov, B.G. (1991) Metallurgy of rare metals. Moscow, Metallurgy.
12. Zinoviev, V.E. (1984) Kinetic properties of metals at high temperatures: Refer. book. Moscow, Metallurgiya [in Russian].
13. Greenwood, N.N., Earnshaw, A. (1997) Vanadium, niobium and tantalum. Chemistry of the elements. Second Edition. Butterworth-Heinemann, 976-1001. https://doi.org/10.1016/B978-0-7506-3365-9.50028-6
14. Juneja, J.M. (2005) Preparation of niobium-aluminium alloys by aluminothermic reduction of Nb2O5. High Temperature Materials and Processes, 24(1), 1-6. https://doi.org/10.1515/HTMP.2005.24.1.1
15. Mitchell, A., Wang, T. (2000) Electron beam melting. Technology review. Proc. of Conf. on Electron Beam Melting and Refining - State of the Art 2000. Millennium Conf., Englewood, September 23-25, 2000, N.-J. Bakish Materials Corporation, 2−11.
16. Nakajima, T., Morimoto, Y., Takaki, S., Abiko, K. (1998) Preparation of ultra-pure Ti-Al alloys. Phys. Status Solidi. A, 2, 411-418. https://doi.org/10.1002/(SICI)1521-396X(199806)167:2<411::AID-PSSA411>3.0.CO;2-9
17. Paton, B.E., Trigub, M.P., Akhonin, S.V. (2008) Electron beam melting of refractory and highly reactive metals. Kyiv, Naukova Dumka [in Ukrainian].
18. Akhonin, S.V., Berezos, V.O., Pikulin, O.M. et al. (2022) Producing high-temperature titanium alloys of Ti-Al-Zr-Si-Mo- Nb-Sn system by electron beam melting. The Paton Welding J., 7, 39-45. https://doi.org/10.37434/tpwj2022.07.07
19. Trigub, N.P., Zhuk, G.V., Kalinyuk, A.N. et al. (2003) Electron beam installation UE-121. Advances in Electrometallurgy, 2, 15-17.
20. Trigub, N.P., Zhuk, G.V., Pikulin, A.N. et al. (2003) Electron beam installation UE-185 for fusion of surface layer of ingots. Ibid., 3, 10-12.