2019 №11 (05) |
DOI of Article 10.15407/as2019.11.06 |
2019 №11 (07) |
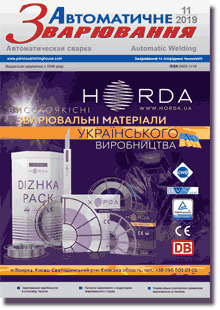
"Avtomatychne Zvaryuvannya" (Automatic Welding), #11, 2019, pp.40-45
Modeling the technology of deposition of a layer of variable chemical composition
V.P. Ivanov, L.K. Leshchinskiy, S.V. Scherbakov
SHEI «Pryazovskyi State Technical University» of MES of Ukraine. 7 Universitetska Str., 87500 Mariupol. E-mail: ivanov_v_p@pstu.edu
It is shown that the nature of the change of chemical composition of the weld (deposited metal) is determined by the law of control of volume feed rate of the alloying electrode, which was derived by mathematical modeling of the effect of surfacing technology on the process of weld pool alloying. It is found that the high gradient of variation of chemical composition along the weld length is ensured by a discrete change of the volume feed rate of the alloying electrode. At a rectangular waveform of the electrode feed pulse, the alloying element distribution in the weld metal is asymmetrical at the stage of increase and decrease of the concentration that is manifested to a greater extent with increase of weld pool volume. Experimentally confirmed calculation results are presented, which show that the trapezoidal shape of the pulse allows reducing the asymmetrical nature of variation of the composition. It is found that the nature and gradient of alloying element distribution in the weld can be changed at pulsed feed of the alloying electrode by a sinusoidal law. Conditions of forming a deposited layer of variable composition and hardness along the length of the barrel of a rolling roll of continuous billet mill were determined. 12 Ref., Tabl. 1, 7 Fig.
Keywords: mathematical modeling, weld pool, deposited metal, variable chemical composition, alloying electrode, feed pulse shape, rolling roll, variable hardness along the barrel length
Received: 11.07.2019
Published: 20.11.2019
References
1. Peremitko, V.V., Panfilov, A.I., (2017) Arc surfacing of layers of metal of varying composition and hardness. The Paton Welding J., 7, 38-42. https://doi.org/10.15407/tpwj2017.07.082. Shebanits, E.N., Omelyanenko, N.I., Kurakin, Yu.N. et al. (2013) Improving the fracture toughness and wear resistance of hard-faced hot-rolling-mill rolls. Metallurgist, 56(7-8), 613-617. https://doi.org/10.1007/s11015-012-9623-7
3. Leshchinsky, L.K., Matvienko, V.M., Mazur, V.O. Method of manufacture of roll of billet continuous casting machine. Ukraine Pat. 119373 [in Ukrainian].
4. Ryabtsev, I.A., Senchenkov, I.K. (2013) Theory and practice of surfacing works. Kiev, Ekotekhnologiya [in Russian].
5. Bennett, A.P. (1972) Prediction and control of composition profiles in graded transition joints. Metals and Materials, 3/4, 146-149.
6. Leshchinsky, L.K., Litvin, N.N., Ivanov, S.G. et al. (1983) Procedure for calculation of alloying process of varying composition welds. Avtomatich. Svarka, 11, 27-29 [in Russian].
7. Gulakov, S.V., Nosovsky, B.I. (2005) Surfacing of working layer with regulated distribution of properties. Mariupol, Novyj Mir [in Russian].
8. Leshchynsky, L.K., Ivanov, V.P. Method of surfacing of varying composition layer. Ukraine Pat. 124035 [in Ukrainian].
9. Lebedev, V.A. (2007) Dependence between the rates of pulsed wire feed and wire melting in welding with short-circuiting. The Paton Welding J., 4, 17-20.
10. Ivanov, V., Lavrova, E. (2014) Improving the efficiency of strip cladding by the control of electrode metal transfer. Applied Mechanics and Materials. Transact. Tech. Publications, 682. Switzerland, 266-269. https://doi.org/10.4028/www.scientific.net/AMM.682.266
11. Shchetinin, S.V., Shchetinina, V.I., Stepnov, K.K. et al. (2010) Improvement of crack resistance of shrouded backup rolls. Breakage protection of metallurgical machines. Zb. Nauk. Prats PDTU, Mariupol, 12, 226-230 [in Ukrainian].
12. Leshchinsky, L.K., Stepnov, K.K., Matvienko, V.M. Method of manufacture of forming rolls. Ukraine Pat. 92559 [in Ukrainian].