2020 №10 (04) |
DOI of Article 10.37434/as2020.10.05 |
2020 №10 (06) |
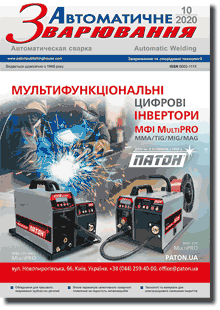
"Avtomatychne Zvaryuvannya" (Automatic Welding), #10, 2020, pp. 26-33
Influence of amplitude and frequency of oscillations of electrode wire in arc surfacing on the formation and structure of the deposited metal and penetration of basic metal
A.A. Babinets, I.O. Ryabtsev, I.P. Lentyugov, I.I. Ryabtsev, T.V. Kayda, I.L. Bogaychuk
E.O. Paton Electric Welding Institute of the NAS of Ukraine. 11 Kazymyr Malevych Str., 03150, Kyiv, Ukraine. E-mail: office@paton.kiev.ua
The influence of the amplitude and frequency of oscillations of the electrode wire during arc surfacing on the formation of deposited beads, nature of the base metal penetration, as well as structural and chemical heterogeneity in the area of the joint of deposited and base metals were studied. It was established that with an increase in the frequency of oscillations of the electrode wire, at the same amplitude of oscillations and the rate of surfacing, an improvement in the formation of the deposited metal and mixing of the layers in the deposited metal; formation of a more dispersed structure; reducing the width of the transition zone; more uniform distribution of alloying elements; more uniform melting and «smoothing» of the fusion boundary of the deposited and base metals occur. The mentioned regularities almost do not change with an increase in the amplitude of oscillations. It was established that the best formation of the deposited metal occurs at the maximum frequency N = 45 min–1 and the amplitude A = 25 mm of oscillations of the electrode wire and the surfacing rate Vs = 7 m/h. 8 Ref., 2 Tabl., 10 Fig.
Keywords: arc surfacing, electrode wire oscillations, amplitude and frequency of oscillations, base metal penetration, deposited metal formation, deposited metal structure, structure heterogeneity
Received: 09.09.2020
References
1. Danilchenko, B.V., Shimanovsky, V.P., Voronchuk, A.P., Terpilo, V.N. (1989) Hard-facing of rapidly wearing parts by self-shielded flux-cored strips. Avtomatich. Svarka, 5, 38–41 [in Russian].2. Zhudra, A.P., Voronchuk, A.P., Fomakin, A.A., Veliky, S.I. (2009) New equipment fir hard-facing of charging device bells and cups. The Paton Welding J., 9, 44-46.
3. Zhudra, A.P., Krivchikov, S.Yu., Petrov, V.V. (2010) Technology for wide-layer hard-facing of crankshafts. Ibid., 2, 32-35.
4. Gulakov, S.V., Burlaka, V.V. (2010) Mechanism of electrode oscillation for formation of deposited beads of complex shape. Vestnik Priazov. GTU. Tekhnicheskie Nauki, 20, 181– 186 [in Russian].
5. Spiridonov, N.V., Kudina, A.V., Kurash, V.V. (2013) Electric arc shielded-gas hard-facing of metal surfaces with oscillating electrode. Nauka i Tekhnika, 4, 3–8 [in Russian].
6. Goloborodko, Zh.G., Dragan, S.V., Simutenkov, I.V. (2013) Automatic submerged-arc surfacing of structural steels with transverse high-frequency movements of electrode. The Paton Welding J., 6, 34-37.
7. Babinets, A.A., Ryabtsev, I.A., Kondratiev, I.A. et al. (2014) Investigation of thermal resistance of deposited metal designed for restoration of mill rolls. Ibid., 5, 16-20. https://doi.org/10.15407/tpwj2014.05.03
8. Ryabtsev, I.A., Babinets, A.A. (2015) Fatigue life of multilayer deposited specimens. Svarochn. Proizvodstvo, 4, 15–19 [in Russian].