2019 №02 (07) |
DOI of Article 10.15407/sem2019.02.08 |
2019 №02 (01) |
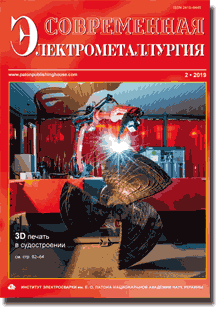
Electrometallurgy Today (Sovremennaya Elektrometallurgiya), 2019, #2, 50-58 pages
Journal Современная электрометаллургия
Publisher International Association «Welding»
ISSN 2415-8445 (print)
Issue № 2, 2019 (June)
Pages 50-58
Computer modeling of structural transformations in shape memory alloys
V.A. Kostin , G.M. Grigorenko
E.O. Paton Electric Welding Institute of the NAS of Ukraine. 11 Kazimir Malevich Str., 03150, Kyiv, Ukraine. E-mail: office@paton.kiev.ua
Computer 3D modeling of medical stents, made of shape memory materials, was made, kinetics of structural transformations in the process of γ↔α′ transformations was analyzed, their effect on stress-strain state was investigated. Calculations were made for shape memory alloys: nitinol (NiTi) and Cu–Zn–Al, used in medicine. The mathematical model was suggested for description of shape memory effects and hyperelasticity. Numerical modeling of structural transformations, stress-strain state of the stent, shape memory effects and hyperelasticity was carried out by using the calculation multiphysical package COMSOL Multiphysics. Peculiar features of martensite formation in the stent during deformation were established. Ref. 12., Tabl. 2, Fig. 10.
Key words: shape memory materials; nitinol; stent; phase transformations; austenite; stress-strain state
Received: 22.04.19
Published: 13.06.19
References
1. Otsuka, K., Wayman, C.M. (1998) Shape Memory Materials. Cambridge University Press, Cambridge, UK, 1-267.2. Mohd, J., Leary, J, Subic, М., Gibson, A. (2014) A review of shape memory alloy research, applications and opportunities. Materials and Design, 56, 1078-1113. https://doi.org/10.1016/j.matdes.2013.11.084
3. Kurdyumov, G.V., Khandros, L.G. (1949) On «thermoelastic» equilibrium in martensite transformations. DAN SSSR, 66(2), 211-220 [in Russian].
4. Koval, Yu.N., Lobodyuk, V.A, (2010) Deformation and relaxation phenomena in transformations of martensite type. Kiev, Naukova Dumka [in Russian].
5. Otsuka, K., Wayman, C.M (1998) Mechanism of shape memory effect and superelasticity. Shape Memory Materials. Cambridge University Press, Cambridge, 27-48.
6. Patoor, E., Eberhardt, A., Berveiller, M. (1996) Micromechanical modelling of superelasticity in shape memory alloys. J. de Physique IV, Coll. C1, 6, 277-292. https://doi.org/10.1051/jp4:1996127
7. Auricchio, F., Sacco, E. (1999) A temperature-dependent beam for shape-memory alloys: Constitutive modelling, finite element implementation and numerical simulations. Computer Methods in Applied Mechanics and Engineering, 174, 171-190. https://doi.org/10.1016/S0045-7825(98)00285-0
8. Lagoudas, D.C., Boyd, J.G., Bo, Z. (1994) Micromechanics of active composites with SMA fibers. J. Engineering Materials, 116, 337-347. https://doi.org/10.1115/1.2904297
9. Movchan, A.A., Movchan, I.A. (2008) Model of nonlinear deformation of shape memory alloys in active processes of direct transformation and structural transition. Mekhanika Kompozitsionnykh Materialov i Konstruktsij, 14(1), 75-87 [in Russian].
10. Chemisky, Y., Duval, A., Patoor, E., Ben Zineb T. (2011) Constitutive model for shape memory alloys including phase transformation, martensitic reorientation and twins accommodation. Mechanics of Materials, 43(7), 361-376. https://doi.org/10.1016/j.mechmat.2011.04.003
11. https://www.comsol.com
12. Barbarino, S., Saavedra Flores, E.I., Ajaj, R.M. et al. (2014) A review on shape memory alloys with applications to morphing aircraft. Smart Materials and Structures, 23(6). https://doi.org/10.1088/0964-1726/23/6/063001