2017 №04 (07) |
DOI of Article 10.15407/tdnk2017.04.08 |
2017 №04 (09) |
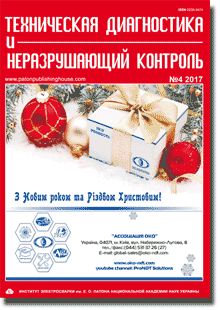
Technical Diagnostics and Non-Destructive Testing, №4, 2017 pp. 52-55
Control of parameters of heated wire in process of drawing
V. A. Porev, A. S. Tomashuk
NTUU “Igor Sikorsky KPI”. 37 Pobedy ave., Kiev-56, 03056. E-mail: a.tomashuk-2018@kpi.ua
The most important factor for drawing process, which is responsible for quality of manufactured products, is a temperature mode in the moment of its deformation. The wire is pre-heated in a melt furnace during hot drawing. Such an approach is necessary for manufacturing the products of the metals and alloys, which can not be subjected to cold drawing. Current methods and quality control devices for such products do not provide control of more than one parameter in process of their manufacture. Our control method allows controlling simultaneously two parameters of the heated wire, namely diameter and temperature in zone of its pre-heating. TV information-measurement system based on CMOS-matrix was proposed as an instrument. Such an approach is caused by wide spatial resolution and large possibilities of these systems. Prior art works of different authors were considered in short. Software for real-time measurements as well as experimental bench were developed and assembled in accordance with the proposed method and stated problems. The results were presented and the conclusions were made. 11 Ref., 1 Tabl., 2 Fig.
Keywords: non-destructive testing, TV information-measurement systems, drawing, wire, temperature field, diameter, shadow method
References
- Perlin, I.L., Ermanyuk, M.Z. (1971) Drawing theory. Moscow, Metallurgiya [in Russian].
- Hew, Y., Liu, X. et al. (2012) Rectifying control of wire diameter during dieless drawing by a deformation measuring method of interframe displacement. Int. J. of Minerals, Metallurgy and Materials, 19(7), 615-621.
- Supriadi, S., Furushima, T., Manabe, K. (2012) Real-time process control system of dieless tube drawing with an image processing approach. Mater. Transact., 53(5), 862-869. https://doi.org/10.2320/matertrans.MF201118
- Kumar, D.K., Aliaahmad, B. et al. (2013) A method for visualization of fine retinal vascular pulsation using nonmydriatic fundus camera synchronized with electrocardiogram. ISRN Ophtalmology, 2013, 1-9. https://doi.org/10.1155/2013/865834
- Ziabari, M., Mottaghitalab, V. et al. (2007) A new image analysis based method for measuring electrospun nanofiber diameter. Nanoscale Res. Lett. 2(12), 597-600. https://doi.org/10.1007/s11671-007-9093-1
- Oznergiz, E., Kiyak, Y.E. et al. (2014) Automated nanofiber diameter measurement in SEM images using a robust image analysis method. J. of Nanomaterials, 2014, 1-6. https://doi.org/10.1155/2014/738490
- Porev, V.A. (2015) Television information and measuring systems. Kyiv, NTUU KPI [in Ukrainian].
- Shredder, G., Trainer, H. (2006) Optical engineering. Moscow, Tekhnosfera [in Russian].
- Slavkov, V.M., Davidenko, O.P. (2015) Thermal non-destructive testing and method of formation of thermal fields on metal plates. Tekhn. Diagnost. i Nerazrush. Kontrol, 3, 39-45 [in Russian].
- Gonsalez, R.S., Woods, R.S. (2012) Digital image processing. 3rd ed. Moscow, Tekhnosfera [in Russian].
- Tomashuk, O.S., Fedorenko, A.V. et al. (2017) Improvement of method for measurement and control of wire by machine vision systems. In: All-Ukrainian Internet-Conf. on Information Society: technological, economical and technical aspects of formation, 20, Ternopil, Tajp, 95-98.