2018 №01 (02) |
DOI of Article 10.15407/tdnk2018.01.03 |
2018 №01 (04) |
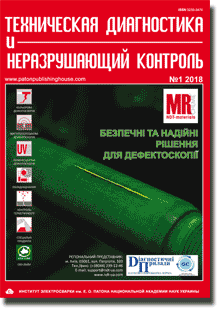
Technical Diagnostics and Non-Destructive Testing #1, 2018, pp. 21-26
Influence of mechanical stresses on the signal of eddy current transducer of magnetic anisotropy
V.M. Uchanin1, S. M. Minakov2
1G. V. Karpenko Physico-Mechanical Institute of the NAS of Ukraine, 5 Naukova str, 79060, Lviv. E-mail: uchanin@ipm.lviv.ua
2NTUU «Igor Sikorskii KPI», 17 Peremogy ave., 03056, Kyiv, Ukraine
The paper gives the results of studying the developed eddy current transducer of magnetic anisotropy with working diameter of 17 mm. Transducer sensitivity to tensile and compressive stresses in ferromagnetic steels is shown. It particular, shown is the shape of signal travel time curves at working frequencies of 5.0; 20.0; and 50.0 kHz, due to tensile and compressive stresses, induced during realization of loading-unloading cycle by four-point bend schematic. Opposite direction of travel time curves for tensile and compressive stresses from the balancing point is demonstrated that allows determination of the nature of stresses in the direction of travel time curves in a complex plane, or by the output signal sign after amplitude-phase transformation. Changes in the amplitude of eddy current transducer signal during realization of loading-unloading cycle were studied. Existence of magneto-elastic hysteresis for both the kinds of loading is shown. 24 Reference, 4 Figures.
Keywords: mechanical tensile and compressive stresses, magnetic anisotropy, eddy current sensor, travel time curves, magnetoelastic hysteresis
Received: 19.02.2018
Published: 20.03.2018
References
1. Nitschke-Pagel, T., Wohlfahrt, H. (2002) Residual stresses in welded joints – sources and consequences. Mat. Sci. Forum, 404-407, 215-226. https://doi.org/10.4028/www.scientific.net/MSF.404-407.215
2. Vinokurov, V.A., Grigoryants, A.G. (1984) Theory of welding strains and stresses. Moscow, Mashinostroenie [in Russian].
3. Lobanov, L.M., Poznyakov, V.D., Pivtorak, V.A. et al. (2009) Residual stresses in welded joints of high-strength steels. Fiz.-Khimich. Mekhanika Materialiv, 6, 13-22 [in Ukrainian].
4. Rossini, N.S., Dassisti, M., Benyounis, K.Y., Olabi, A.G. (2012) Method of measuring residual stresses in components. Materials and Design, 35, 572-598. https://doi.org/10.1016/j.matdes.2011.08.022
5. (2008) ASTM Standard E 837-08: Standard test method for determining residual stresses by the hole-drilling strain-gage method. USA, Philadelphia.
6. Lobanov, L.M., Pivtorak, V.A., Savitsky, V.V., Tkachuk, G.I. (2006) Procedure for determination of residual stresses in welded joints and structural elements using electron speckle-interferometry. The Paton Welding J., 1, 24-29.
7. Bulte, D.P., Langman, R.A. (2002) Origins of magnetomechanical effect. J. of Magnetism and Magnetic Materials, 251, 229-243. https://doi.org/10.1016/S0304-8853(02)00588-7
8. Ostash, O., Voldmarov, O., Uchanin, V., Bezlyudko, G. (2004) Diagnostics of stress-strain state and damage accumulation in steel structure components by magnetic method. In: Proc. of Int. Conf. on Fracture Mechanics and Strength of Structures. Lviv, PMI, 749-753.
9. Zavalnyuk, O.P., Uchanin, V.M. (2013) Monitoring of stress-strain state of load-carrying elements of ship structures. Vidbir i Obrobka Informatsii, 38(114), 13-16 [in Ukrainian].
10. Stuecker, E., Hofer, G., Koch, D., Guenes, U. (1988) Method and apparatus for measuring and precisely locating internal tensile stresses in hardened regions of components by measuring coercive field strength and Barkhausen noise amplitude. Appl. USA, Pat. 4881030, Int. Cl. G01B7/24, G01N27/72. 182845. Fil. 18.04.1988; publ. 14.11.1989.
11. Gur, H., Erlan, G., Bateglin, C. (2016) Investigating the effect of subsequent weld passes on surface residual stresses in steel weldments by magnetic Barkhausen noise technique. Materials Evaluation, 3, 408-423.
12. Mekhontsev, Yu.Ya. (1966) On magnetic methods of evaluation of internal stresses. Defektoskopiya, 2, 94-95 [in Russian].
13. Orekhov, G.T. (1974) Determination of residual welding stresses by magneto-elastic method. Avtomatich. Svarka, 4, 30-32 [in Russian].
14. Abuku, S. (1977) Magnetic studies of residual stress in Iron and steel induced by uniaxial deformation. Jap. J. Appl. Phys., 16(7), 1161-1170. https://doi.org/10.1143/JJAP.16.1161
15. Yamada, H., Uchiyama, S., Takeuchi, et al. (1987) Noncontact measurement of bending stress using a magnetic anisotropy sensor. IEE Transact. on Magnetics, 23(5), 2422-2424. https://doi.org/10.1109/TMAG.1987.1065329
16. Minakov, S.N., Yurchenko, V.A., Anosov, A.P. (1992) Method for determination of stress intensity in products of ferromagnetic materials. USSR author's cert., Int. Cl. G011/12. Publ. 23.09.92 [in Russian].
17. Fomichev, S.K., Minakov, S.N., Mikhalko, S.V. et al. (2009) Determination of force impacts on a pipeline by analysis of longitudinal stress distribution epures. Tekh. Diagnost. i Nerazrush. Kontrol, 2, 11-14 [in Russian].
18. Zhukov, S.V., Zhukov, V.S., Kopitsa, N.N. (2002) Method of determination of mechanical stresses and device for its realization. Pat. 2195636 RF, publ. 27.12.02 [in Russian].
19. Lo, C.C.H. (2011) Characterization of residual stresses in ferrous components by magnetic anisotropy measurements using a Hall effect sensor array probe. Ed. by D.O. Thompson. Review of Progress in Quantitative Nondestructive Evaluation, 30, 1249-1255. https://doi.org/10.1063/1.3592077
20. Uchanin, V., Minakov, S., Nardoni, G. et al. (2017) Eddy current method for evaluation of stresses in steel components. In: Proc. of 14th Intern. Conf. on Application of Contemporary Non-Destructive Testing in Engineering (September 4-6, 2017, Bernardin, Slovenia), 207-212.
21. Tumanski, S. (2011) Handbook of magnetic measurements. Boca Raton Florida, CRS Press. https://doi.org/10.1201/b10979
22. Uchanin, V.M., Minakov, S.M., Ostash, O.P. et al. (2015) Method of complex electromagnetic control of structural and strain-stress state of ferromagnetic materials. Pat. 100379 Ukraine, Int. Cl. G01L1/12, G01N27/72 [in Ukrainian].
23. Uchanin, V.M. (2013) Eddy current put-on transducers of double differentiation. Lviv, Spolom [in Ukrainian].
24. Uchanin, V., Lutsenko, G., Opanasenko, A., Dzhaganian, A. (2016) PROMPRYLAD Family of eddy current flaw detectors – from simple to more complicated. In: Proc. of 19th World Conf. on NDT, 2016, Munich.