2018 №01 (03) |
DOI of Article 10.15407/tdnk2018.01.04 |
2018 №01 (05) |
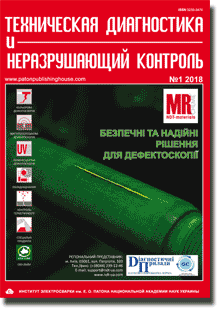
Technical Diagnostics and Non-Destructive Testing #1, 2018, pp. 27-33
High-performance methods of numerical studies for solving the problems of evaluation of defective structure serviceability
A.S.Milenin1, E.A.Velikoivanenko1, G.F.Rozynka1, N.I.Pivtorak1, A.N.Khinich2, V.A.Sidoruk2
1 E.O.Paton Electric Welding Institute of the NAS of Ukraine 11 Kazimir Malevich str., 03150, Kiev. E-mail: office@paton.kiev.ua
2 V.M.Glushkov Institute of Cybernetics of the NAS of Ukraine, 40 Akad. Glushkov prosp., 03187, Kiev. E-mail: incyb@incyb.kiev.ua
A set of models was developed for assessment of the limit state under the conditions of complex temperature-force service impact by the method of numerical prediction of multidimensional stress-strain state, subcritical and critical damage of structure materials, allowing for different deformation mechanisms at external loading for the case of characteristic problems of evaluation of serviceability of pipeline elements with detected defects of local corrosion-erosion metal loss. Software implementation of the model was performed by applying finite-element solution of joint problems of kinetics of the state of a specific defective pipeline by applying new high-efficient methods of parallel computation, based on multiprocessor and hybrid computer technologies. Features of the influence of local surface losses of metal on development of their subcritical damage, limit state and serviceability, were studied in the cases of service-induced damage of pipeline elements of the main and process systems. It is also shown that the efficiency of a specific algorithm of numerical calculations is significantly affected by the structure of the defining matrix of the system of linear equations. 10 References, Table 1, Fig. 9.
Keywords: acoustic emission, 103-D reactor, propagating defects, continuous monitoring, residual life
Received: 10.01.2018
Published: 20.03.2018
References
- Escoe, A.K. (2006) Piping and pipelines.Assessment guide. Texas, Gulf Professional Publishing.
- Strelnikova, E.A., Kovch, O.I. (2015) Examination of reciprocal influence of pores in weld under impact of thermal force load. East-European J. of Advanced Technologies, 5, 59-63 [in Russian]. https://doi.org/10.15587/1729-4061.2015.51869
- Lemaitre, J., Desmorat, R. (2005) Engineering damage mechanics. Ductile, creep, fatigue and brittle failures. Berlin, Springer-Verlag.
- Radaj, D. (1992) Heat effects of welding. Temperature field, residual stress, distortion. Berlin, Springer-Verlag.
- Xue, L. (2007) Damage accumulation and fracture initiation in uncracked ductile solids subject to triaxial loading. Int. J. of Solids and Structures, 44, 5163-5181. https://doi.org/10.1016/j.ijsolstr.2006.12.026
- Velikoivanenko, E.A., Rozynka, G.F., Milenin, A.S. et al. (2013) Modelling of processes of nucleation and development of ductile fracture pores in welded structures. The Paton Welding J., 9, 24-29.
- Karzov, G.P., Margolin, B.Z., Shvetsova, V.A. (1993) Physical-mechanical modeling of fracture processes. St.-Petersburg, Politekhnika [in Russian].
- Velikoivanenko, E.A., Milenin, A.S., Pozynka, G.F. et al. (2016) Simulation of processes of initiation and propagation of subcritical damage of metal in welded pipeline elements at low-cycle loading. Tekh. Diagnost. i Nerazrush. Kontrol, 4, 14-20 [in Russian].
- Makhnenko, V.I. (2006) Resource of safety operation of welded joints and components of modern structures. Kyiv, Naukova Dumka [in Russian].
- Velikoivanenko, E.A., Rozynka, G.F., Milenin, A.S. et al. (2014) Probabilistic estimate of the condition of pipeline elements with detected thinning defects. Tekh. Diagnost. i Nerazrush. Kontrol, 2, 12-18 [in Russian].