2019 №01 (02) |
DOI of Article 10.15407/tdnk2019.01.03 |
2019 №01 (04) |
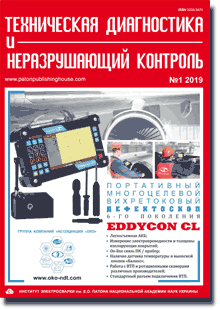
Technical Diagnostics and Non-Destructive Testing №1, 2019, стр. 26-31
New method and means of phase shifting interferometry for reproduction and control of structural material surface evolution
L.I. Muravsky, T.I. Voronyak, I.V. Stasyshyn
Karpenko Physico-Mechanical Institute of the NAS of Ukraine. 5 Naukova Str., 79060, Lviv, Ukraine. E-mail: murav@ipm.lviv.ua 31
Abstract:
A fast method of three-step phase shifting interferometry with arbitrary phase shifts of the reference beam was developed. This method has a number of advantages, compared to similar methods of phase shifting interferometry, and, first of all, it does not require precise calibration of the phase-shifting device or additional recording of the reference and object beams in the interferometer, and also ensures a smooth shifting of reference beam phase. The method of three-step phase shifting interferometry was the base to create an experimental model of 3D profile meter. It was used to test new procedures of reproducing the surface relief, extraction of 3D roughness and waviness, establishing the most probable point of initiation of a fatigue microcrack in notched samples of aluminium alloy D16T under cyclic loading and monitoring the evolution of the surface of U8 steel samples after hydrogenation. It is shown, in particular, that the microcrack starts with the highest probability on the boundary of the fatigue zone of prefracture from the site, where the greatest increment of surface roughness occurs during fatigue loading. When studying the influence of hydrogen on the relief of U8 steel samples, it was found that during saturation with hydrogen its surface is deformed and develops blisters. When hydrogen escapes from the material, the deformational changes of the surface go on, the most intensive of them occurring during the first two hours after hydrogenation, and essentially slow down after two weeks, while blisters increase in size and change their shape. 12 Ref., 6 Fig. 31
Keywords: phase shifting interferometry, reference beams, surface roughness, fatigue macrocrack, blisters 31
Надійшла до редакції 19.02.2019
Published: 06.03.2019
1. Schreiber H., Brunning J.H. (2007) Phase shifting interferometry. Optical Shop Testing. D. Malacara (Ed.). Hoboken, NJ, John Wiley & Sons. Chapter 14, рр. 547–666. https://doi.org/10.1002/9780470135976.ch14
2. Lobanov, L.M., Muravsky, L.I., Pivtorak, V.A., Voronyak, T.I. (2017) Monitoring the stressed state of structural elements with application of electromagnetic waves of the optical range. Vol. 3: Technical diagnostics of materials and structures. In: Refer. book, 8 Vol. Ed. by Z.T. Nazarchuk. Lviv, Prostir-M [in Ukrainian].
4. Muravsky L.I., Kmet' A.B., Stasyshyn I.V. et al. (2018) Three-step interferometric method with blind phase shifts by use of interframe correlation between interferograms.Opt. Lasers Eng., 105, 27–34. https://doi.org/10.1016/j.optlaseng.2017.12.011
5. Ostash O.P., Panasyuk V.V. (2001) Fatigue process zone at notches. Int. J. Fatigue, 23, 7, 627–636. https://doi.org/10.1016/S0142-1123(01)00004-4
6. Ostash O.P. (2006) New approaches in fatigue fracture mechanics. Materials Science, 42, 1, 5–19. https://doi.org/10.1007/s11003-006-0053-1
7. Muravsky L.I., Picart P., Kmet' A.B. et al. (2016) Evaluation of fatigue process zone dimensions in notched specimens by two-step phase shifting interferometry technique. Opt. Eng., 55, 10, 104108 – 1–9. https://doi.org/10.1117/1.OE.55.10.104108
8. Arola D., Williams C.L. (2002) Estimating the fatigue stress concentration factor of machined surfaces. Int. J. Fatigue, 24, 9, 923–930. https://doi.org/10.1016/S0142-1123(02)00012-9
9. Suraratchai M., Limido J., Marbu C., Chieragatti R. (2008) Modelling the influence of machined surface roughness on the fatigue life of aluminium alloy. Ibid, 30, 12, 2119–2126. https://doi.org/10.1016/j.ijfatigue.2008.06.003
10. Chan K.S., Tian J.W., Yang B., Liaw P.K. (2009) Evolution of slip morphology and fatigue crack initiation in surface grains of Ni200. Metall. Mater. Trans. A, 40, 11, 2545–2556. https://doi.org/10.1007/s11661-009-9980-4
11. Mitsushima S., Takakuwa Y., Nagasava K. et al. (2016) Membrane electrolysis of toluene hydrogenation with water decomposition for energy carrier synthesis. Electrocatalysis, 7, 2, 127–131. https://doi.org/10.1007/s12678-015-0289-3
12. Kanezaki T., Narazaki C., Mine Y. et al. (2008) Effects of hydrogen on fatigue crack growth behavior of austenitic stainless steels. Int. J. Hydrog. Energy, 33, 10, 2604–2619. https://doi.org/10.1016/j.ijhydene.2008.02.067