2015 №06 (04) |
DOI of Article 10.15407/tpwj2015.06.05 |
2015 №06 (06) |
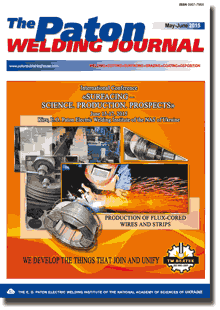
The Paton Welding Journal, 2015, #5-6, 26-29 pages
Modern state and challenges for development of laser and hybrid surfacing technologies (Review)
V.Yu. Khaskin, V.D. Shelyagin And A.V. Bernatsky
E.O. Paton Electric Welding Institute, NASU. 11 Bozhenko Str., 03680, Kiev, Ukraine. E-mail: office@paton.kiev.ua
Abstract
The paper deals with development of the processes of laser and combined (for instance, laser-plasma) surfacing. It is shown that in these processes feeding the surfacing material (mainly, in the form of powder, less often - as wire) into the zone of impact of laser radiation focused into a spot of 1-5 mm diameter results in formation of a deposited layer of a certain height with the specified physico-chemical characteristics on the treated surface. The considered processes have a number of advantages and disadvantages. The advantages include: possibility of deposition of layers of 0.1-3.0 mm height with specified properties; considerable weakening of the effect of redistribution of components from base material into the deposited layer, promoting an increase of the accuracy of forecasting the results and making the deposited layer properties as close as possible to initial properties of the material being surfaced; producing equiaxed fine-crystalline (highly-dispersed) structures of the deposited metal and small (up to 0.1-0.5 mm) heat-affected zone; minimizing the allowance for finish machining to values of 0.3-0.5 mm to the side due to low roughness (up to Ra 200-300 mm) of the deposited surfaces. The disadvantages include: presence of transverse initial cold microcracks in the deposited layers, appearance of which is the result of relaxation of high internal tensile stresses; possibility of formation of both internal and external pores associated with non-metallic inclusions and residual humidity of the surfacing powder, as well as presence of treated surface contamination; relatively high cost of the process associated with comparatively high cost of laser equipment. It is shown that the main tendencies in development of laser surfacing technology in industrialized countries are as follows: producing corrosion- and wear-resistant coatings with improved physico-mechanical properties; synthesis of 3D objects; producing thin deposited layers with special properties. The prospects for further development of laser and laser-plasma (laser-arc) surfacing processes are associated with the ability to eliminate the drawbacks inherent to each of the components separately, due to interaction of these components. 16 Ref., 3 Figures.
Keywords: laser technologies, hybrid and combined processes, commercial application, equipment, materials, prospects
Received: 08.04.15
Published: 28.07.15
References
1. Grigoriants, A.G., Safonov, A.N. (1987) Laser engineering and technology: Manual for higher education institutions. Vol. 3: Methods of surface laser treatment. Ed. by A.G. Grigoriants. Moscow: Vyschaya Shkola.
2. Velichko, O.A., Avramchenko, P.F., Molchan, I.V. et al. (1990) Laser powder cladding of cylindrical parts. Avtomatich. Svarka, 1, 59-65.
3. (2007) Laserstrahlschweissen mit pulverfoermigem Schweisszusatz. Edelstahl-Mechanik GmbH. Praktiker, 3, 68-69.
4. Zeng Xaoyan, Zhu Beidi, Tao Zengyi et al. (1993) Automatic powder feeder and technology of laser cladding. Chin. J. Lasers, 20(3), 210-214.
5. Pokhmurska, G.V. (2003) Crack formation in thermal coatings depending on laser remelting conditions. Fizyko-Khimichna Mekhanika Materialiv, 1, 59-62.
6. Chekurin, V.F., Pokhmurska, G.V. (2004) Mathematical model of cracking of laser-modified metal powder coatings. Ibid., 5, 18-22. https://doi.org/10.1007/s11003-005-0086-x
7. Hoffman, J. (2001) Reconditioning of exchangeable parts using laser technologies. The Paton Welding J., 12, 33-34.
8. Konyushin, A., Manyak, V., Holz, R. et al. (2009) Technical capabilities of modern solid-state lasers. Fotonika, 2, 22-23.
9. Birger, E.M., Moskvitin, G.V., Polyakov, A.N. et al. (2009) Industrial laser surfacing: State-of-the-art and tendencies. Svarochn. Proizvodstvo, 9, 3-8.
10. Gvozdetsky, V.S., Krivtsun, I.V., Chizhenko, M.I. et al. (1995) Laser-arc discharge: Theory and applications. In: Welding and Surfacing Rev., Vol. 3. Amsterdam: Harwood Acad. Publ.
11. Hai-ou Zhang, Ying-ping Qian, Gui-lan Wang (2006) Study of rapid and direct thick coating deposition by hybrid plasma-laser manufacturing. Surface & Coatings Technology, 201, 1739-1744. https://doi.org/10.1016/j.surfcoat.2006.02.049
12. Chashchin, E.A., Fedin, A.V., Mitrofanov, A.A. et al. (2007) Increase of the efficiency of plasma treatment of materials at using of additional power source as laser radiation. In: Proc. of 3rd Int. Sci.-Pract. Conf. on Study, Development and Application of High Technologies in Industry (14-17 March 2007, St.-Petersburg, Russia), Vol. 8: High technologies, fundamental and applied researche, 119-120. SPb: SPbPU.
13. Shelyagin, V.D., Khaskin, V.Yu., Pereverzev, Yu.N. (2006) Laser-microplasma alloying and coating of steel. The Paton Welding J., 2, 2-5.
14. Wilden, J., Bergman, J.P., Dolles, M. (2005) Riporti superficiali laser: aumento di efficienza e flessibilita tramite processi ibridi. Riv. Ital. Saldatura, 6, 809-816.
15. Zabelin, A.M., Shiganov, I.N. Chirkov, A.M. et al. (2007) Hybrid technologies of laser surfacing: Turorial. Moscow: MGOU.
16. Melyukov, V.V., Chirkov, A.M. (2006) Laser-plasma technologies for surface treatment. In: Proc. of 5th Int. Conf. on Beam Technologies. Laser Application (23-28 Sept., 2006, St.-Petersburg, Russia), 236-240.