2016 №06 (19) |
DOI of Article 10.15407/tpwj2016.06.20 |
2016 №06 (21) |
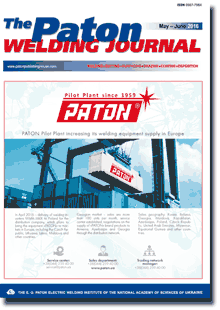
The Paton Welding Journal, 2016, #5-6, 117-123 pages
3D-printing of metallic volumetric parts of complex shape based on welding plasma-arc technologies (Review)
V.N. Korzhik1, V.Yu. Khaskin1, A.A. Grinyuk1, 2, V.I. Tkachuk1, S.I. Peleshenko3, V.V. Korotenko1, 2 and A.A. Babich1
1E.O. Paton Electric Welding Institute, NASU, 11 Kazimir Malevich Str., 03680, Kiev, Ukraine. E-mail: office@paton.kiev.ua
2NTUU «Kiev Polytechnic Institute», 37 Pobeda Ave., 03056, Kiev, Ukraine. E-mail: mail@KPI.ua
3South China University of Technology, 510641, Guangzhou, PRC. E-mail: sviatoslav@qq.com
Abstract
Manufacturing complex-shaped metal products by 3D-printing is becoming ever more urgent in modern industry. Laser technologies (SLS- and SLM-processes) are most often applied for this purpose, while electron beam technologies (EBF3) are used less often. Both of them are characterized by quite high cost and low efficiency. This paper deals with new tendencies in application of welding technology for 3D-printing of complex metallic products, including those complemented by concurrent or subsequent machining. It is shown that application of welding technologies to produce volumetric metallic products significantly lowers their manufacturing cost at simultaneous increase in productivity, compared to SLS- and SLM-processes. The most promising welding technology of 3D-printing is plasma-arc process with application of wires or powders. It allows at comparatively low heat input creating quality volumetric products with 3–50 mm thickness from Fe, Ni, Co, Cu, Ti, Al alloys, as well as composite materials containing refractory components. Application of welding technologies allows producing both comparatively small and long products, not requiring any finish machining (for instance, growing stiffeners on large-sized panels, manufacturing honeycomb panels, building structures, etc.). Combination of welding technologies of 3D-printing with concurrent or finish machining (mostly, by CNC milling) allows manufacturing ready for use metal products of complex profile. 19 Ref., 2 Tables, 8 Figures.
Keywords: 3D-printing, metal products, welding technologies, machining, materials, equipment
Received: 22.03.16
Published: 19.07.16
References
- Kruth, J.P., Leu, M.C., Nakagawa, T. (1998) Progress in additive manufacturing and rapid prototyping. CIRP Annals-Manufact. Techn., 47(2), 525–540. https://doi.org/10.1016/S0007-8506(07)63240-5
- (2009) Laser technologies for treatment of materials: Current problems of fundamental studies and applied developments: Monograph, Chapter: Laser technologies of rapid prototyping and direct fabrication of 3D objects. Moscow: Fizmatlit.
- Slyusar, V.I. (2003) Fabber-technologies. New tool for 3D modeling. Elektronika: Nauka, Tekhnologiya, Biznes, 5, 54–60.
- Deckard, C.R., Beaman, J.J. (1987) Recent advances in selective laser sintering. In: of 14th Conf. on Production Research and Technology (Michigan, 1987), 447–451.
- Kablov, E.N. (2015) Additive technologies as the dominant of national technology initiative. Intellekt & Tekhnologii, 2(11), 52–55.
- Bruce, M.R., Riley, S.F., Cola, M.J. et al. (2012) Measurement and simulation of titanium alloy deposit temperature in electron beam additive manufacturing. In: Trends in Welding Research: of 9th Int. Conf. (Chicago, USA, 4–8 June 2012), 963–969.
- Kruth, J.P. (2004) Selective laser melting of iron-based powder. Mater. Process. Technol., Vol. 149, 616–622.
- Karunakaran, K.P., Suryakumar, S., Vishal Pushpa et al. (2010) Low cost integration of additive and subtractive processes for hybrid layered manufacturing. Robotics and Computer-Int. Manufact., 26(5), 490–499. https://doi.org/10.1016/j.rcim.2010.03.008
- Colegrove, P., Williams, S. (2013) High deposition rate high quality metal additive manufacture using wire + arc technology. http://xyzist.com/wp-content/uploads/2013/12/Paul-Colegrove-Cranfield-Additivemanufacturing.pdf
- Venuvinod, P.K., Weiyin Ma (2004) Rapid prototyping: laser-based and other technologies. In: Springer Science + Buisness Media. New York.
- Doyle, T.E., Ryan, P.M. Cooling workpieces being manufactured by shape melting. Pat. EP0340939A1 (US4857694). Int. Cl. B23K9/04, B23K37/003, B23K37/00F. Publ. 8.11.89.
- Martina, F. (2014) Investigation of methods to manipulate geometry, microstructure and mechanical properties in titanium large scale wire + arc additive manufacturing. In: School of Aerospace, Transport and Manufacturing. Cranfield University.
- Kovacevic, R. (2003) Development of machine for rapid manufacturing/repair. In: The 2003 CTMA Symp. (Salt Lake City, USA, March 31–April 3,2003), www.engr.smu.edu/rcam
- Alhuzaim, A.F. (2014) Investigation in the use of plasma arc welding and alternative feedstock delivery method in additive manufacture: Thesis submitted in partial fulfillment of the requirements for the degree of Master of Sci. General Engineering. University of Motana.
- Baufeld, B., Van der Biest, O., Gault, R.S. (2010) Additive manufacturing of Ti–6Al–4V components by shaped metal deposition: Microstructure and mechanical properties. Materials & Design., Vol. 31, 106–111. https://doi.org/10.1016/j.matdes.2009.11.032
- Clark, D., Bache, M.R., Whittaker, M.T. (2008) Shaped metal deposition of a nickel alloy for aero engine applications. Materials Proc. Techn., Vol. 203, 439–448.
- Chad, H. (2014) Metallic additive manufacturing: Comprehensive overview and findings on 3D-printing for construction. http://www2.iceaustralia.com/ei/images/cmic14/cmicpresentations/plenary/henry.pdf
- (2015) Art of Grigory Dochkin. In: CWELD — equipment and materials for welding and cutting,08.2015; http://adiosgroup.ru/?p=242
- (2015) 3D-welding from MX3D will print-out the bridge above the water, 17.06.2015; http://weldworld.ru/news/razraborki/5583-3d-svarka-ot-mx3d-raspechataet-most-nad-vodoy.html