2017 №03 (03) |
DOI of Article 10.15407/tpwj2017.03.04 |
2017 №03 (05) |
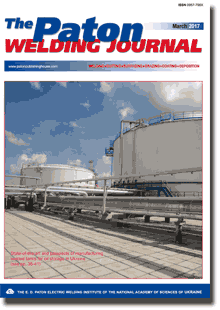
The Paton Welding Journal, 2017, #3, 25-32 pages
Vacuum diffusion welding of foil from powder nickel-chromium alloy
I.A. Gusarova1, A.M. Potapov1, T.A. Manko1, Yu.V. Falchenko2, A.I. Ustinov2, L.V. Petrushinets2 and T.V. Melnichenko2
1DB «M.K. Yangel Yuzhnoye» 3 Krivorozhskaya Str., 49008, Dnepr, Ukraine. E-mail: info@yuzhnoye.com
2E.O. Paton Electric Welding Institute, NASU 11 Kazimir Malevich Str., 03680, Kiev, Ukraine. E-mail: office@paton.kiev.ua
Abstract
The paper deals with the influence of diffusion welding parameters on formation of joints from foil of Ni–20Cr powder alloy 25 mm thick. It is shown that welding of nichrome alloy in the temperature range of 800–1200 °C without application of interlayers does not allow producing defectfree joints. Features of formation of Ni–Cr alloy joints at application of interlayers from foils, produced by the technology of electron beam deposition and condensation in vacuum were studied. Foil with multilayer structure of Ni–Al, Ti–Cu systems and foil with porous structure from Cu, Ni and Cr was used in the work. Microstructure and chemical composition of the joints were studied, using optical and electron microscopy. Strength properties of metal in the joint zone were assessed by the results of microindentation and tensile testing of flat samples. It is found that application of such interlayers in welding allows producing defectfree microstructure of the joint zone. It is shown that joints with strength properties on the level of those of base metal are formed in welding through an interlayer from copper-based porous foils. 18 Ref., 2 Tables, 9 Figures.
Keywords: vacuum diffusion welding, Ni–Cr powder alloy, porous foils, multilayer foils, microstructure, microindenting
Received: 02.02.17
Published: 19.04.16
References
- Tumino, G. (2003) European development and qualification status and challenges in hot structures and thermal protection systems for space transportation concepts. In: of the 4th European Workshop on Hot Structures and Thermal Protection Systems for Space Vehicles (Palermo, Italy, 26–29 Nov. 2002). Paris: European Space Agency, 2003, 39–43.
- Multilayer thermal protection system of reusable space vehicle. 91891 Ukraine. Int. Cl. B64G 1/58, B64C 1/38, B64C 3/36. Fill. 26.11.2013. Publ. 25.07.2014.
- Frolov, G.A., Tsyganenko, V.S., Pasichny, V.V. (2010) Thermal tests of elements of rocket and space engineering products at radiation heating. Aviatsionno-Kosmicheskaya Tekhnika i Tekhnologiya, 10, 28–32.
- Gusarova, I.A., Parko, M., Potapov, A.M. et al. (2016) Evaluation of high temperature resistance of three-layer honeycomb panel produced from YuIPM-1200 alloy by vacuum diffusion welding. The Paton Welding J., 12, 29–33. https://doi.org/10.15407/tpwj2016.12.05
- Medovar, B.I. (1966) Welding of heat-resistant austenitic steels and alloys. Moscow: Mashinostroenie.
- Sporer, D., Fortuna, D. (2014) Selecting materials for brazing a honeycomb in turbine engines. Welding J., 93(2), 44–48.
- Atkinson, H.V. (1985) Review of the role of short-circuit diffusion in the oxidation of nickel, chromium and nickel-chromium alloys. Oxidation of Metals, 24(3/4), 177–197. https://doi.org/10.1007/BF00664231
- Musin, R.A., Antsiferov, V.N., Kvasnitsky, V.F. (1979) Diffusion welding of heat-resistant alloys. Moscow: Metallurgiya.
- Stolyarov, V.N. (1971) Heat-resistant joints of nickel alloys made by diffusion welding and press braze-welding. Proizvodstvo, 1, 26–29.
- Lyushinsky, A.V. (2006) Diffusion welding of dissimilar metals. Moscow: Akademiya.
- Musin, R.A., Lyamin, Ya.V. (1991) Application of perforated inserts in diffusion welding. Proizvodstvo, 2, 2–4.
- Falchenko, Yu.V., Muravejnik, A.N., Kharchenko, G.K. et al. (2010) Pressure welding of micro-dispersed composite material AMg5 + 27 % Al2O3 with application of rapidly solidified interlayer of eutectic alloy Al + 33 % Cu. The Paton Welding J., 2, 7–10.
- Ustinov, A.I., Falchenko, Yu.V., Melnichenko, T.V. et al. (2015) Diffusion welding of steel to tin bronze through porous interlayers of nickel and copper. Ibid., 9, 13–19. https://doi.org/10.15407/tpwj2015.09.02
- Kharchenko, G.K. et al. (2009) Examination of diffusion processes in welded joints of titanium aluminide (TiAl). Visnyk ChDTU. Seriya Tekhn. Nauky, 37, 117–119.
- Ustinov, A.I., Matvienko, Ya.I., Polishchuk, S.S. et al. (2009) Investigation of phase transformations and plastic deformation at continuous heating of Al/Cu multilayer foil. The Paton Welding J., 10, 23–27.
- Firstov, S.A. et al. (2007) Indentation equation. Dopovidi Nats. Akademii Nauk Ukrainy, 12, 100–106.
- Davies, B.J., Stephenson, S. (1962) Diffusion bonding and pressure brazing of Nimonic 90 nickel-chromium-cobalt alloy. British Welding J., Vol. 2, Issue 3, 139–148.
- Akimov, V.V. et al. (2009) Influence of porosity on elastic properties of hard alloys TiC–TiN. Mekhanika i Tekhn. Fizika, 50(4), 136–138