2020 №07 (03) |
DOI of Article 10.37434/tpwj2020.07.04 |
2020 №07 (05) |
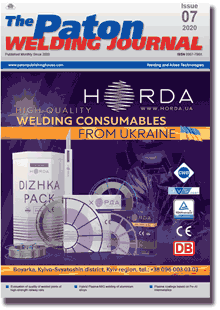
The Paton Welding Journal, 2020, #7, 29-37 pages
Coatings based on Fe–Al intermetallics produced by the methods of plasma and supersonic plasma gas-air spraying
Yu.S. Borysov, A.L. Borysova, N.V. Vigilyanska, O.P. Gryshchenko and M.V. Kolomytsev
E.O. Paton Electric Welding Institute of the NAS of Ukraine 11 Kazymyr Malevych Str., 03150, Kyiv, Ukraine. E-mail: office@paton.kiev.ua
Abstract
The results of investigations of the structure and phase composition of thermal coatings based on Fe–Al intermetallics are presented. Fe–Al intermetallics were selected as a material of protective coatings due to their high heat and corrosion resistance and cost effectiveness as compared to many modern heat-resistant materials. As spraying materials, the powders of mechanical mixtures of Fe and Al as well as powders produced by the method of mechanochemical synthesis of Fe–Al intermetallics by the treatment of mixtures of powders Fe and Al in a high-energy ball mill were used. The content of powder components corresponds to the intermetallics Fe3Al, FeAl and Fe2Al5. For spraying, the alloyed powders were also used having the composition corresponding to the intermetallic Fe3Al. To increase the mechanical and physicochemical properties of the intermetallic, as alloying elements Ti, Mg, Cr, Zr, and La were also used. The coating was produced by the methods of plasma and supersonic plasma gas-air spraying. It was found that in plasma coatings with FeAl-powders, in addition to the initial phase (Fe3Al, FeAl and Fe2Al5), Fe and Al oxides are also present, due to which microhardness of the coatings increases by about 1300 MPa relative to the initial powders. The microhardness of the plasma coating of the alloying powder Fe–TiAl, 2 times increases relatively to the initial powder due to the formation of the intermetallic phase FeTi in the coating. During spraying of mechanical mixtures, due to a low probability of contact interaction of Fe and Al particles during flight and rapid cooling of melts particles on the surface of the base, the synthesis of intermetallics does not have a time to develop and in the coatings no intermetallic phases are revealed. In the coatings produced by supersonic plasma gas-air spraying, the main phase is α-Fe(Al)-solid solution, which is the result of a high rate of melt hardening. 14 Ref., 4 Tables, 8 Figures.
Keywords: Fe–Al intermetallic, powders, mechanochemical synthesis, mechanical mixture, plasma spraying, supersonic plasma gas-air spraying, coating, structure, microhardness
Received 30.06.2020
References
1. Zamanzade, M., Barnoush, A., Motz, C. (2016). A Review on the properties of iron aluminide intermetallics. Crystals, 6, 1, 10. https://doi.org/10.3390/cryst60100102. Palm, M., Stein, F., Dehm, G. (2019). Iron aluminides. Annual Review of Materials Research, 49, 297-326. https://doi.org/10.1146/annurev-matsci-070218-125911
3. Cebulski, J. (2015). Application of FeАl intermetallic phase matrix based alloys in the turbine components of a turbocharger. Metalurgija-Sisak then Zagreb, 54, 154-156.
4. Morris, D. G., Muñoz-Morris, M. A. (2010). Recent developments toward the application of iron aluminides in fossil fuel technologies. Advanced Engineering Materials, 13, 1-2, 43-47. https://doi.org/10.1002/adem.201000210
5. Cordier-Robert, C., Grosdidier, T., Ji G., Foct, J. (2006). Mössbauer and X-ray diffraction characterization of Fe- 60Al40 coatings prepared by thermal spraying. Hyperfine Interact, 168, 1, 951-957. https://doi.org/10.1007/s10751-006-9393-3
6. Senderowski, C., Bojar, Z. (2008). Gas detonation spray forming of Fe-Al coatings in the presence of interlayer. Surface & Coatings Technology, 202, 3538-3548. https://doi.org/10.1016/j.surfcoat.2007.12.029
7. Xiao, Ch., Chen, W. (2006). Sulfidation resistance of CeO2-modified HVOF sprayed FeAl coatings at 700 °C. Ibid., 201, 3625-3632. https://doi.org/10.1016/j.surfcoat.2006.08.138
8. Xiang, J., Zhu, X., Chen, G. et al. (2009). Oxidation behavior of Fe40Al-xWC composite coatings obtained by high-velocity oxygen fuel thermal spray. Transactions of Nonferrous Metals Society of China, 19, 1545-1550. https://doi.org/10.1016/S1003-6326(09)60067-4
9. Yang, D. M., Tian, B. H., Cao, Y. (2011). Microstructures and properties of FeAl coatings prepared by LPPS, APS and HVOF. Proceedings of the International Thermal Spray Conference, Hamburg, Germany, 1229-1234.
10. Borisov, Yu.S., Borisova, A.L., Astahov, E.A.et al. (2017). Detonation coatings of intermetallic powders of Fe-Al system produced using mechanical alloying. The Paton Welding J., 4, 23-29. https://doi.org/10.15407/tpwj2017.04.05
11. Chen, Y., Liang, X., Wei, Sh. et al. (2009). Heat treatment induced intermetallic phase transition of arc-sprayed coating prepared by the wires combination of aluminum-cathode and steel-anode. Applied Surface Science, 255, 19, 8299-8304. https://doi.org/10.1016/j.apsusc.2009.05.142
12. Hansen, M., Anderko, K. (1962). Structure of Double Alloys. Part 2. Moscow, Metallurgizdat [in Russian]
13. Borisova, A.L., Timofeeva, I.I., Vasil`kovskaya, M.A. et al. (2015). Structural and phase transformations in Fe-Al intermetallic powders during mechanochemical sintering. Powder Metallurgy and Metal Ceramics, 54, 7-8, 490-496. https://doi.org/10.1007/s11106-015-9740-5
14. Borisov, Yu.S., Borisova, A.L., Burlachenko, A.N. et al. (2017). Structure and properties of alloyed powders based on Fe3Al intermetallic for thermal spraying produced using mechanochemical synthesis method. The Paton Welding J., 9, 33-39. https://doi.org/10.15407/tpwj2017.09.06