2020 №05 (03) |
DOI of Article 10.37434/as2020.05.04 |
2020 №05 (05) |
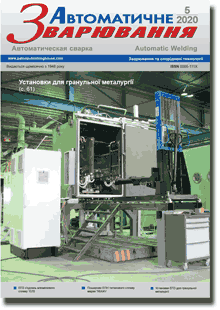
"Avtomatychne Zvaryuvannya" (Automatic Welding), #5, 2020, pp. 25-30
Improvement of crack resistance of banded support rolls at high-speed surfacing with low energy input
S.V. Shchetinin, V.I. Shchetinina, S.P. Desyatskii
Priazovskii State Technical University, 7 Universitetskaya Str., 87555, Mariupol, Ukraine. E-mail: shchetynin.sergey2012@gmail.com
The objective of the work is improvement of deposited metal crack resistance and development of the process of high-speed surfacing with a low energy input of banded support rolls. In order to achieve the set objective, we developed the process of improving the crack resistance due to high-speed surfacing of banded support rolls with a low energy input. In keeping with the equation of heat propagation at high-speed surfacing with a low energy input, increase of surfacing speed is accompanied by lowering of heat input, narrowing of melting isotherm width and HAZ. Calculation and experimental methods were used to establish that at increase of surfacing speed, lower heat input results in decrease of deformations and welding stresses, and reduction of HAZ, where cold cracks form, that prevents delamination of the deposited metal. Melting and solidification rates rise, time of the pool staying in the liquid state is reduced that prevents liquid metal pouring out of the weld pool and improves deposited metal formation. Established regularities were the base for development of the process of high-speed surfacing with low energy input, at which the heat input and welding stresses decrease, HAZ is reduced and deposited metal delamination is prevented, melting and solidification rate increase, time of the pool staying in the liquid state becomes shorter, and crack resistance of banded support rolls becomes higher. Developed process of high-speed surfacing of banded support rolls with a low energy input provides a lowering of the heat input and welding stresses, HAZ reduction, increase of melting and solidification rates and crack resistance, and absence of deposited metal delamination or band failures. 11 Ref., 6 Fig.
Keywords: high-speed surfacing with low energy input, melting isotherms, heat input, welding stresses, HA, crack resistance, banded support rolls
Received: 24.10.2019
References
1. Prokhorov, N.N. (1976) Physical processes in metal during welding. Moscow, Metallurgiya [in Russian].2. Shorshorov, M.Kh., Belov, V.V. (1972) Phase transformations and changes of properties of steel in welding. Moscow, Nauka [in Russian].
3. Makhnenko, V.I. (1976) Calculation methods of investigation of kinetics of welding stresses and strains. Kiev, Naukova Dumka [in Russian].
4. Makhnenko, V.I., Poznyakov, V.D., Velikoivanenko, E.A. et al. (2009) Risk of cold cracking in welding of structural highstrength steels. The Paton Welding J., 12 , 2-6.
5. Yushchenko, K.A., Velikoivanenko, E.A., Chervyakov, N.O. et al. (2016) Effect of anisotropy of properties of nickel alloy on stresses and plastic deformations in weld zone. Ibid., 1 0 , 2-7. https://doi.org/10.15407/tpwj2016.10.01
6. Finkel, V.M. (1970) Physics of fracture. Moscow, Metallurgiya [in Russian].
7. Nikolaev, G.A., Kutkin, S.A., Vinokurov, V.A. (1982) Strength of welded joints and deformations of structures. Moscow, Vysshaya Shkola [in Russian].
8. Vinokurov, V.A., Grigoryants, A.G. (1984) Theory of welding stresses and strains. Moscow, Mashinostroenie [in Russian].
9. Rykalin, N.N. (1951) Calculation of thermal processes in welding. Moscow, Mashgiz [in Russian].
10. Volobuev, Yu.V., Fedorov, V.G., Kuligin, G.B. (1983) Evaluation of influence of parameters of welding thermal cycle on austenitic grain size in heat-affected zone of steels of 12KhN4MA type. Svarochn. Proizvodstvo, 12 , 6-8 [in Russian].
11. Shchetynin, S.V., Shchetynina,V.I. (2019) Method of electric arc surfacing of low-carbon steels. Ukraine Pat. 119594, Int. Cl. B23 K 9/04 [in Ukrainian].