2020 №06 (07) |
DOI of Article 10.37434/as2020.06.08 |
2020 №06 (01) |
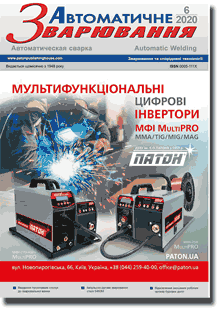
"Avtomatychne Zvaryuvannya" (Automatic Welding), #6, 2020, pp. 45-50
Peculiarities of repair of worn areas of drill bit bodies
B.V. Stefaniv
E.O. Paton Electric Welding Institute of the NAS of Ukraine, 11 Kazymyr Malevych Str., 03150, Kyiv, Ukraine. E-mail: office@paton.kiev.ua
The peculiarities of wear of operating elements of the bodies of steel, matrix drill bits and heads were considered and studied, and repairability criteria were determined. Performed analysis of worn areas of operating elements of used drill bit bodies showed that at drilling wear of cutters and seats is the most common, and wear of flushing components of the drill bit bodies occurs less often. Metallographic examination showed that the deposited layer and the base metal are connected by a thin transition layer of diffusion origin, which shows that base metal melting and filler metal dissolution did not occur in it. It is established that the drill bit repair is cost-effective in those cases, when the cost of such repair does not exceed one third of the cost of the bit proper. Multiple repeated reconditioning of operating elements of worn areas reduces the cost of manufacturing new drill bits several times. Conducted production trials of reconditioned drill bits showed that repair of worn areas of the operating elements allows considerable extension of the service life and saving 30…50 % of the initial cost of a specific drill bit type. 12 Ref., 2 Tabl., 8 Fig.
Keywords: wear, surfacing, tungsten carbides, area, bridge, diamond-carbide cutter (DCC), polycrystalline diamond cutter (PDC), carbide coating (CC), microstructure, wear resistance.
Received: 02.06.2020
References
1. Draganchuk, O.T., Prygorovska, T.O. (2008) Analysis of drill bit working out of PDC type in deposits of Ukraine and world. Nafrogazova Energetyka, 4, 9, 11-15 [in Ukrainian].2. Wear-resistant materials. Rods for gas and TIG welding. https://docplayer.ru/32381351-Iznosostoykie-materialy-itvyordye-splavy-na-osnove-kobalta.html.
3. Laansoo, A., Kübarsepp, J., Vainolab V., Viljus M. (2012) Induction brazing of cermets to steel. Estonian J. of Engineering, 18(3), 232-242. https://doi.org/10.3176/eng.2012.3.08
4. Materials for brazing and surfacing Tero Cote. http://www.castolin.com.ua/
5. Materials of Postalloy Company for surfacing of protective coatings. http://www.postle.com
6. Samsonov, G.V., Vitryanyuk, V.N., Chaplygin, F.I. (1974) Tungsten carbides. Kiev, Naukova Dumka [in Russian].
7. Pierson, H. O. (1996) Handbook of Refractory Carbides and Nitrides. New Jersey: Noyes Publications. https://doi.org/10.1016/B978-081551392-6.50001-5
8. Stefaniv, B.V., Khorunov, V.F., Sabadash, O.M., Maksymova, S.V., Voronov, V.V. (2014) Features of reconditioning steel drill bit watercourse. The Paton Welding J., 11, 50-54. https://doi.org/10.15407/tpwj2014.11.10
9. Stefaniv, B.V., Khorunov, V.F., Sabadash, O.M. et al. (2015) Peculiarities of restoration of working parts of drilling bit matrix bodies. Ibid., 8, 47-50. https://doi.org/10.15407/tpwj2015.08.10
10. Stefaniv, B.V. (2016) Investigation of wear resistance of protective coatings under conditions of hydroabrasive wear. Ibid., 9, 26-29. https://doi.org/10.15407/tpwj2016.09.05
11. Stefaniv, B.V., Nyrkova, L.I., Larionov, A.V., Osadchuk, S.O. (2020) Corrosion resistance of composite material deposited by TIG method using flexible cord Tero Cote 7888T. Ibid., 9, 26-29. https://doi.org/10.37434/tpwj2020.02.05
12. Wear-resistant materials. http://www.svarka52.ru/upload/osnovnoi_katalog_po_paike_i_Terocote_BRAZING_1.pdf.