2021 №09 (02) |
DOI of Article 10.37434/as2021.09.03 |
2021 №09 (04) |
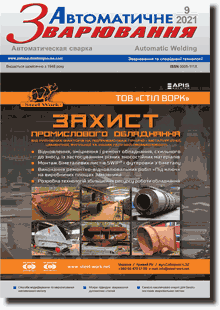
"Avtomatychne Zvaryuvannya" (Automatic Welding), #9, 2021, pp. 19-23
Some advantages of welded joints of aluminum 1201 alloy produced by friction stir welding
A.G. Poklyatsky, S.I. Motrunich, I.M. Klochkov, T.M. Labur
E.O. Paton Electric Welding Institute. 11 Kazymyr Malevych Str., 03150 Kyiv, Ukraine. E-mail: office@paton.kiev.ua
The article analyzes the structural features, characteristics of strength and resistance to initiation and propagation of operational cracks of butt joints of aluminum 1201 alloy of 2 mm thickness, produced by friction stir welding (FSW) and argon arc welding with non-consumable electrode (AAWNCE). It is shown that in FSW as a result of intensive plastic deformation of the metal in the weld nugget, a fine-grained structure with a grain size of 5…6 μm is formed. In the zone of thermomechanical influence, deformed long grains are observed, oriented in the direction of movement of the plasticized metal, and small equiaxial grains, the size of which varies within 4…12 μm. Whereas in AAWNCE of this alloy the weld metal has a characteristic cast structure with large (0.20…0.25 mm) dendrites. The absence of penetrations and reinforcements in the welds produced by FSW, allows avoiding high levels of stress concentration at the places of transition from the weld to the base material, which negatively affect the service and life characteristics of welded joints. The peculiarities of the formation of permanent joints in the solid phase during FSW also help to reduce the degree of softening of the metal in the welding zone and increase their tensile strength, resistance to initiation and propagation of operational cracks. 15 Ref., 7 Fig.
Keywords: microstructure, hardness, tensile strength, resistance to initiation and propagation of operational cracks
Received: 08.07.2021
References
1. Lahti, K. (2003) FSW - possibilities in Shipbuilding. Svetsaren, 1, 6-8. https://doi.org/10.22486/iwj.v36i4.1787802. Kallee, S., Nicholas, D. (1998) Causing a Stir in the Future. Welding and Joining, 2, 18-21.
3. Okamura, H., Aota, K., Ezumi, M. (2000) Friction Stir Welding of Aluminum Alloy and Application to Structure. Journal of Japan Institute of Light Metals, 4, 166-172. https://doi.org/10.2464/jilm.50.166
4. Mori, H., Noda, M., Tominaga, T. (2007) Current state on application of friction stir welding for rolling stock. Ibid., 11, 506-510.
5. Kallee, S.W., Davenport, J., Nicholas, E.D. (2002) Railway Manufacturers Implement Friction Stir Welding. Welding J., 10, 47-50.
6. Arbegast, W.J. (2006) Friction Stir Welding After a Decade of Development. Ibid, 3, 28-35.
7. Johnsen, M.R. (1999) Friction Stir Welding Takes Off at Boeing. Ibid, 2, 35-39.
8. Kallee, S., Nicholas, E., Thomas, W. (2002) Friction stir in aerospace - the industrial way. Part II. Bulletin TWI, 9-10, 13-18.
9. Takehisa, H. (2006) Friction stir welding technology of aluminum alloys for aircraft. Journal of Japan Institute of Light Metals, 3, 178-183. https://doi.org/10.2464/jilm.56.178
10. Beletsky, V.M., Krivov, G.A. (2005) Aluminium alloys. Composition, properties, technology, application: Refer. Book. Ed. by I.N. Fridlyander. Kiev, KOMINTEKH. ISBN 966- 8550-25-0 [in Russian].
11. Mashin, V.S., Poklyatsky, A,G., Fedorchuk, V.E. (2005) Mechanical properties of aluminium alloys in consumable and nonconsumable electrode arc welding. The Paton Welding J., 9, 39-45.
12. Defalco, J. (2006) Friction stir welding vs. fusion weldin. Welding J., 3, 42-44.
13. Pietras, A., Zadroga, L., Lomozik, M. (2004) Characteristics of welds formed by pressure ,welding incorporating stirring of the weld material (FSW). Welding International, 1, 5-10. https://doi.org/10.1533/wint.2004.3215
14. Ishchenko, A.Ya., Poklyatsky, A.G. (2010) Tool for friction stir welding of aluminium alloys. Pat. 54096 Ukraine, Int. Cl. В23К 20/12; u201005315; fill. 30.04.2010; publ. 25.10.2010 [in Ukrainian].
15. Poklyatsky, A.G. (2011) Resistance of welds on thin-sheet aluminium alloys to initiation and propagation of service cracks. The Paton Welding J., 10, 5-9.