2002 №01 | 2002 №03 |
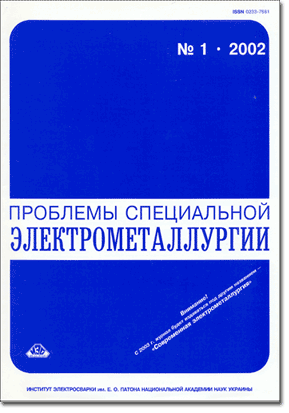
CONTENTS
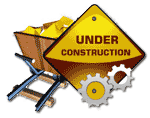
ELECTROSLAG TECHNOLOGY
Saenko V.Ya. About history of creation of the first ESR furnaces. P. 2
History of creation and design features of the first ESR furnaces is described. It is shown that even at the earlier stage of the ESR progress the various designs of the furnaces were developed and implemented in industry, thus making it possible in a very short period (1956-1959) to test the most challenging technological diagrams of remelting and to create the reliable bases for the rapid industrial realization of the new electroslag technologies.
Tsykulenko A.K., Medovar L.B. and Chernets A.V. Some new fields of application of electroslag technology. P. 7
Capabilities of producing large-tonnage homogeneous and composite billets from high-alloyed steels and superalloys for the needs of power machine building are considered. It is shown that the application of electroslag remelting using a two-circuit diagram providing the absence of rigid relation between the temperature condition of melting and rate of melting of consumable electrode allows comparatively simple realization of these capabilities.
Tsykulenko K.A. Devices for molten metal pouring. requirements to these devices for EST LM. P. 10
Devices available in metallurgy for molten metal pouring are described. Feasibility of use of these devices in electroslag processes using liquid filler metal was analyzed. It is shown that there are no yet portable devices neither in big metallurgy nor in foundry that could perform pouring of liquid metal at a required rate. This device is necessary to develop for EST LM. Some basic requirements to the devices for molten metal pouring are formulated.
Skripnik S.V. and Chernega D.F. Application of the electroslag process for repair of forging hammer die plates. P. 12
Application of the electroslag process for repair of die plates (die holders) is described. The technology provides for repair of thick plates of hard-to-weld structural steels by the method of electroslag filling up of the cavity and electroslag hot topping using chips. The electroslag process includes metal filling up of the lower and upper technological pockets.
ELECTRON BEAM PROCESSES
Mogilnikova T.T., Nerodenko L.M. and Movchan B.A. Microscopic limit of elasticity of two-phase Cu-68 vol.% Fe material produced by electron beam physical vapour desosition in vacuum. P. 16
Dependence of microscopic limit of elasticity of two-phase Cu-Fe condensate with 68 vol.% Fe on annealing temperature was studied. It was experimentally demonstrated that the microscopic limit of elasticity decreases by more than 2 times as a result of annealing at fixed temperatures in the range of 600-650 oC.
Zhuk G.V. Calculation of the thickness of intermetallic layer formed in deposition of titanium and aluminium matrix on steel fibres by the method of electron beam melt dispersion. P. 18
Basic parameters and principles of construction of a mathematical model of producing a fibrous composite material by the method of electron beam melt dispersion are described. Calculation of thermal processes for the titanium and aluminium matrices reinforced with steel fibres has been conducted using the model. Optimal technological modes are given, which allow minimising the thickness of the formed intermetallic interlayer.
Kalinyuk A.N., Kozlovets O.N. and Akhonin S.V. Manufacture of semi-finished products from titanium ingots produced by the EBCHM method. P. 21
Results of investigations of structure and mechanical properties of forgings and tubes made from titanium ingots produced by electron beam melting are given. It has been established that the degree of reduction of titanium ingots for the manufacture of forgings and rods should be not less than six. The technology is suggested for the manufacture of hot-rolled tubes directly from titanium cast billets with a diameter of 200 mm, and the high quality of the resulting items is shown.
Fyodorov V.N., Shchekin-Krotov V.A. and Kasumov A.M. Vibration of the melt with electron beam during EBR. P. 25
The method for excitation of vibration of the titanium melt with electron beam is described. It is shown that vibration causes levelling of the side surface of ingot and increases uniformity of distribution of low-volatile impurities.
PLASMA-ARC TECHNOLOGY
Lobanov L.M., Zhadkevich M.L., Shapovalov V.A., Zabarilo O.S., melnik G.A., Zhdanovsky A.A., Prikhodko M.S. and Gnatushenko A.V. Plasma technology of remelting metallic radioactive waste. P. 27
Technology of utilization of metallic radioactive waste (MRW) using a method of plasma-arc skull melting (PASM) in a water-cooled crucible is offered. Diagram of furnace for PASM and technological scheme of mini-plant for processing MRW are presented. Technical-economical characteristics of plasma technology and equipment for MRW remelting are given.
Burnashev V.R., Zhadkevich M.L. and Shapovalov V.A. Plasma-arc skull melting and casting of refractory metals and alloys. P. 30
Technology of plasma-arc skull melting and casting of refractory metals is developed. Yield factors are determined. Technical recommendations for processing chromium, molybdenum, tungsten and niobium are given.
VACUUM-INDUCTION MELTING
Shejko I.V. Removal of shrinkage cavity from ingots during induction melting in sectional mould. P. 34
Capabilities of remelting processes to form ingots in a cooled mould are analysed. It is shown that remelting processes, having no strict relationship between power input and melting rate (EBR and PAR), allow a sufficiently flexible control over solidification of metal, including at the final stage of melting. This provides ingots which are free from such defects as shrinkage cavities. Induction melting in a sectional mould (IMSM) is also characterised by the absence of strict relationship between the melting rate and power input. The mechanism of transformation of parameters of the metal pool in removal of a shrinkage cavity at the final stage of melting of an ingot by the IMSM method is described on the basis of analysis of the investigation results.
Anikin Yu.F., Dobkina Yu.G., Ladokhin S.V., Klochikhin V.V. and Zhemanyuk P.D. Combined induction and electron beam melting of casting production wastes of heat-resistant alloys ZhS3DK and ZHS26-VI. P. 37
A method of melting the wastes of ZhS3DK and ZhS26-VI alloys, using a combined induction and electron beam heating was studied. Melting was conducted in a unit, based on a vacuum-induction furnace that was further fitted with an electron beam gun. The main advantages of the new technology consist in improvement of the metal quality and rather low specific power consumption.
GENERAL PROBLEMS OF METALLURGY
Kharchenko G.K., Falchenko Yu.V., Taranova T.G., Novomlinets O.A. and Polovetsky E.V. Sublimation of metals in heating under autovacuum conditions. P. 44
Processes of sublimation of metals under the autovacuum conditions are investigated. It was established that in closed sealed volumes the sublimation of copper occurs in heating with the formation of condensate at the surfaces of samples of molybdenum, chromium, niobium and steel Kh18N10T. It is shown that copper condensate on chromium, produced at heating temperature 950 oC and 20 min holding, consists of spherical particles of diameter of not more than 2 mm. With increase in time of heating the copper condensate thickness is increased.
(You are viewing the simplified file contents)