2018 №02 (06) |
DOI of Article 10.15407/sem2018.02.07 |
2018 №02 (01) |
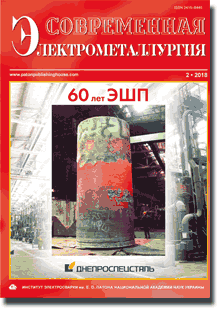
Electrometallurgy Today (Sovremennaya Elektrometallurgiya), 2018, #2, 52-55 pages
Formation of structure of high-chromium cast iron, surfaced by shots in current-carrying mould
Yu. M. Kuskov, F. K. Biktagirov, T. I. Grishchenko, A. I. Evdokimov
E.O. Paton Electric Welding Institute of the NAS of Ukraine. 11 Kazimir Malevich Str., 03150, Kyiv, Ukraine. E-mail: office@paton.kiev.ua
Abstract
Metallographic examination of metal, surfaced by shots of high-chromium cast iron in current-carrying mould, was carried out. It was established, that in spite of peculiar conditions of formation of metal pool in this case, the structure of periphery zones of deposited metal are not greatly differed from the structure, formed at ESR in conventional water-cooled mould. To produce the homogeneous structure of the deposited layer without the presence of non-melted metal inclusions in it, it is necessary to select the surfacing electric modes with account for a mass speed of shot feeding and its fractional composition. Ref. 10, Fig. 5.
Key words: electroslag surfacing; current-carrying mould; surfacing shot; high-chromium cast iron; metal structure
Received: 05.02.18
Published: 25.05.18
References
- Garber, M.E. (1972) Castings of wear-resistant white cast irons. Moscow, Mashinostroenie [in Russian].
- Tsypin, I.I. (1983) Wear-resistant white cast irons. Structure and properties. Moscow, Metallurgiya [in Russian].
- Gavrilyuk, V.P., Tikhonovich, V.I., Shalevskaya, I.A., Gutko, Yu.I. (2010) Abrasion-resistant high-chromium cast irons. Lugansk, Knowledge [in Russian].
- Zhukov, A.A., Silman, G.I., Froltsov, M.S. (1984) Wear-resistant castings from complexly-alloyed white cast irons. Moscow, Mashinostroenie [in Russian].
- Valits, K.A., Stojko, V.P., Ponomarenko, V.P., Pasechnik, S.Yu. (1988) Electroslag surfacing of rotary hammer crushers of by-product coke production. In: Theoretical and technological principles of surfacing. Surfacing in metallurgical and mining industry. Kiev, PWI, 24–25 [in Russian].
- Kiseleva, I.V., Dorokhov, V.V., Shvartser, A.Ya., Gerasimov, E.A. (1989) Application of electroslag heating in hardening-restoration surfacing of excavator bucket teeth. Problemy Spets. Elektrometallurgii, 3, 28–30 [in Russian].
- Ponomarenko, V.P., Pasechnik, S.Yu., Stojko, V.P., Shvartser, A.Ya. (1990) Strength and wear resistance of deposited high-chromium cast iron alloyed with titanium and manganese. In: Equipment and materials for surfacing. Kiev, PWI, 86–89 [in Russian].
- Kuskov Yu.M., Gordan G.N., Bogajchuk I.L. and Kajda T.V. (2015) Electroslag surfacing using discrete materials of different methods of manufacture. The Paton Welding J., 5–6, 34–36. https://doi.org/10.15407/tpwj2015.06.06
- Kuskov, Yu.M., Sarychev, I.S. (2004) Restoration electroslag surfacing of mill rollers 2000. Proizvodstvo, 2, 39–43 [in Russian].
- Tomilenko, S.V., Kuskov, Yu.M. (1999) Energy specifics of electroslag process in current-supplying mould. Svarka, 2, 51–53 [in Russian].