2019 №03 (06) |
DOI of Article 10.15407/sem2019.03.07 |
2019 №03 (08) |
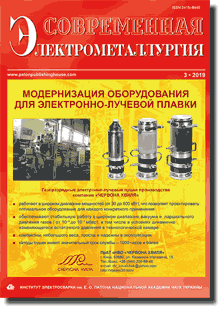
Electrometallurgy Today (Sovremennaya Elektrometallurgiya), 2019, #3, 45-54 pages
Journal Современная электрометаллургия
Publisher International Association «Welding»
ISSN 2415-8445 (print)
Issue № 3, 2019 (September)
Pages 45-54
Effect of condensed multilayer protective coatings on fatigue resistance of VT6 alloy samples
K.Yu. Yakovchuk1, A.V. Mykytchyk1, Yu.E. Rudoy1, Yu.F. Lugovskoy2
1State-Run Enterprise «International Center for Electron Beam Technologies of E.O. Paton Electric Welding Institute, NASU». 68 Gorky (Antonovich) Str. 03150, Kyiv, Ukraine. E-mail: mykytchyk@paton-icebt.kiev.ua
2Frantsevich Institute for Problems of Materials Sciences NASU. 3 Krzhizhanovsky str., 03680, Kyiv, Ukraine. E-mail: lugovskoi_u@ukr.net
The effect of multilayer damping and erosion-resistant functional coatings 28…96 μm thick on high-cycle fatigue strength of VT6 alloy samples is considered. Coatings were applied by electron beam physical vapor deposition (EB-PVD) on VT6 titanium alloy substrates. Room-temperature high-cycle fatigue tests were conducted by exciting resonant bending oscillations of the first (non-destructive stresses) and second forms of oscillations in the sample at frequencies of 0.4 and 2.0 kHz on the basis of 107 cycles, respectively. It was found that deposition of single-layer B4C coatings on VT6 alloy samples is impractical due to poor adhesion of the coating (bending angle was 4°). If inner bonding layer (Ti, Ag, Hf 1...3, 2.5...15.0, 1...2 μm thick, respectively) was used, it was possible to increase the adhesion of the coating (bending angle was 20...25°), while the endurance limit decreased by 29...33 % compared with an uncoated alloy. It was demonstrated that the inner bonding layer (Cu or AgCu) provides high adhesion (the bending angle reached 36…48°). However, the endurance limit decreased by 33…49 % due to rapid penetration of the fatigue crack through this inner bonding layer into the VT6 alloy. Deposition of inner bonding multilayer (coatings of Hf/Ti/Hf/Ti/Cr or AgСu/Ti/AgCu/Ti/AgCu/B4C type) with an optimal ratio of individual layer thicknesses ensures endurance limit at the level of 73...80 % of uncoated samples. Furthermore, it was found that multilayer Hf/Ag/Ni/Cr damping coatings 52 μm thick ensure a decrease of the amplitude of oscillations (effective stresses in the sample) by 23...56 % as compared to uncoated samples. The tests were carried out using the same power supplied from testing rig to coated and uncoated samples for oscillation excitation. Therefore, to evaluate the damping efficiency of various coatings and their effect on high-cycle fatigue of substrate material, it is recommended to conduct vibration tests of samples at the same power supplied for oscillation excitation. Ref. 18, Table 1, Fig. 8.
Key words: alloy; electron beam physical vapor deposition; high-cycle fatigue; protective (functional) coatings; multilayer coatings; fatigue crack; compressor blades
Received: 10.06.19
Published: 03.10.19
References
1. Kotelnikov, A.N., Gabov, I.G. (2015) Evaluation of fatigue strength of compressor blades under irregular loading. Fundamentalnye Issledovaniya, 9, 470-475 [in Russian].2. Gorlov, D.S., Muboyadzhyan, S.A., Shchepilov, A.A., Aleksandrov, D.A. (2017) Influence of ion implantation on damping capability of composition «alloy-ion-plasma coating». Trudy VIAM, 2, 24-32, DOI: 10.18577/2307-6046-2017-0-2-4-4 [in Russian]. https://doi.org/10.18577/2307-6046-2017-0-2-4-4
3. Malashenko, I.S., Kurenkova, V.V., Belousov, I.V., Biber, V.I. (2014) Structure and physical-mechanical properties of vacuum condensates of titanium alloy VT6. Sovrem. Elektrometallurgiya, 2, 26-35 [in Russian].
4. Chichkov, B.A. (2000) Blades of aircraft gas turbine engines. Pt 1. Operational damageability of blades. Moscow, MGTU GA [in Russian].
5. Mikitchik, A.V., Rudoy, Yu.E., Grushetsky, I.V. et al. (2016) Effect of multilayer condensation coatings on characteristics of titanium alloy VT6 damping. Sovrem. Elektrometallurgiya, 1, 26-31 [in Russian]. https://doi.org/10.15407/sem2016.01.04
6. Yakovchuk, K.Yu., Rudoy, Yu.E., Mikitchik, A.V. et al. (2012) Effect of condensation conditions on structure and properties of hard coatings on B4S base, produced by electron beam evaporation in vacuum. Ibid., 3, 15-19 [in Russian].
7. Torvik, P., Langley, B. (2015) Material properties of hard coatings developed for high damping. In: Proc. of the 51st AIAA/SA/ASEE Joint Propulsion Conf. (Orlando, Florida, USA, July 29, 2015). https://doi.org/10.2514/6.2015-4195
8. Trapezon, A.G., Lyashenko, B.A., Lysenkov, M.O. (2013) Fatigue resistance of metals with reinforcing coatings (Review). Problemy Prochnosti, 3, 42-57 [in Russian]. https://doi.org/10.1007/s11223-013-9457-y
9. Costa, M.Y.P. et al. (2011) Fatigue behavior of PVD coated Ti-6Al-4V alloy. Int. J. of Fatigue, 33, 759-765. https://doi.org/10.1016/j.ijfatigue.2010.11.007
10. Baragetti, S., Villa, F. (2014) An updated review of the fatigue behavior of components coated with thin hard corrosion-resistant coatings. The Open Materials Sci. J., 8, 87-98. https://doi.org/10.2174/1874088X01408010087
11. Ustinov, A.I., Zinkovsky, A.P., Tokar, I.G., Skorodzievsky, V.S. (2010) About capabilities of nanostructured coatings to reduce the dynamic intensity of design elements of machines. Sovrem. Elektrometallurgiya, 2, 28-33 [in Russian].
12. Trapezon, A.G., Lyashenko, B.A., Lipinskaya, N.V. (2009) Fatigue of titanium alloy VT20 with vacuum-plasma coatings at high temperatures. Problemy Prochnosti, 4, 101-107 [in Russian]. https://doi.org/10.1007/s11223-009-9138-z
13. Movchan, B.A., Yakovchuk, K.Yu. (2004) Electron beam installations for evaporation and deposition of inorganic materials and coatings. Advances in Electrometallurgy, 2, 9-14.
14. (1979) Fatigue tests under high frequencies of loading. Ed. by V.A. Kuzmenko. Kiev, Naukova Dumka [in Russian].
15. Lugovskoj, Yu.F. (1987) Procedure of fatigue tests of composite materials under bending, produced by electron beam evaporation. Problemy Spets. Elektrometallurgii, 4, 61-65 [in Russian].
16. Lashko, S.V., Lashko, N.F. (1988) Soldering of metals. Moscow, Mashinostroenie [in Russian].
17. Shmorgun, V.G., Slautin, O.V., Evstropov, D.A. et al. (2014) Structure and phase composition of Cu-Ti system coatings formed on copper substrate. Vestnik Sibirsk. Gos. Industr. Un-ta, 4, 8-10 [in Russian].
18. Szczepanik, R. (2013) Analysis of 1st stage compressor rotor blade stress and vibration amplitudes in one-pass jet engine. J. of KONES Powertrain and Transport, 20(4), 441-450. https://doi.org/10.5604/12314005.1137858