2020 №04 (08) |
DOI of Article 10.37434/sem2020.04.01 |
2020 №04 (02) |
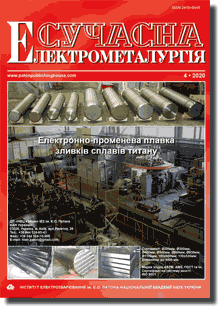
"Suchasna Elektrometallurgiya" (Electrometallurgy Today), 2020, #4, 3-6 pages
Electroslag remelting of consumable electrodes of variable section
L.B. Medovar1, Y.O. Pedchenko1, A.V. Sybir2, V.L. Petrenko1, D.V. Kolomiets1
1E.O. Paton Electric Welding Institute of the NAS of Ukraine. 11 Kazymyr Malevych Str., 03150, Kyiv, Ukraine. E-mail: office@paton.kiev.ua
2National Metallurgical Academy of Ukraine. 4 Gagarin Ave., 49600, Dnipro, Ukraine. E-mail: nmetau@nmetau.edu.ua
Abstract
The practice of using electroslag remelting for recycling worn rollers of slab type continuous casters is considered. The expediency of remelting the rollers without cutting off necks and welding them into a solid consumable electrode is shown. The use of ESR with a two circuit scheme for remelting rollers with necks is proposed and investigated on experimental melts. Electrodes of a variable section of 150 mm diameter were used as electrodes-simulators of real rollers, which simulated the 110 mm and 80 mm barrel of a roller, as well as the transition from the barrel to the neck and the neck proper of a real roller of slab caster, respectively. The filling factor varied from 0.69 to 0.2. Two series of experimental melts were performed in order to obtain a stable depth of the two-phase zone during the ingot solidification. It was found that the same remelting rate and depth of the two-phase zone are preserved at 2:1 ratio of electric power supplied to the consumable electrode to the power supplied to the current-supplying mould. Ref. 8, Fig. 3.
Keywords: electroslag remelting; recycling; roller; continuous casting; consumable electrode; mushy zone; current supplying mould
Received 17.12.2020
References
1. Samojlovich, Yu.A., Timashpolskij, V.I., Goryainov, V.A., Kabishov, S.N. (2008) Increase of service life of BCCM bearing rollers. Litio i Metallurgiya, 45(1), 49–55 [in Russian].2. Vdovin, K.N., Berdnikov, A.S., Podosyan, A.A. (2010) Development of technology for producing BCCM rollers by ESR method. Teoriya i Tekhnologiya Metallurgicheskogo Proizvodstva, 2, 68–73 [in Russian].
3. 30 years of metallurgical equipment repair shop No. 3, LLC Mechanical-repair Complex (PJSC Magnitogorsk Metallurgical Plant) [in Russian]. bizon.ru/news/view/news_id/376228
4. Khrebto, V.E. (2002) Procedural bases of BCCM reconstruction in accordance to modern requirements of technology and reliability: Syn. of Thesis for Cand. of Techn. Sci. Degree, Magnitogorsk, 114 [in Russian].
5. Yusin, A.N. (2004) Development of rational modes of electroslag remelting of rollers and mold walls of billet continuous casting machines: Syn. of Thesis for Cand. of Techn. Sci. Degree, Magnitogorsk, 162 [in Russian].
6. Berdnikov, A.S. (2013) Resource-saving technologies for producing of BCCM roller ingots based on electroslag remelting: Syn. of Thesis for Cand. of Techn. Sci. Degree, Magnitogorsk, 143 [in Russian].
7. Medovar, L. et. аl. (2005) ESR with two power sources and process control. In: Proc. of Int. Symposium on Liquid Metal Processing and Casting (Santa-Fe, New Mexico, USA, Sept. 11–14, 2005), 131–135.
8. Yanwu, Dong, Zhouhua, Jiang, Haibo, Cao et al. (2016) Study of single-power, two-circuit ESR process with current-carrying mold, development of the technique and its physical simulation. Metallurg. and Mater. Transact. B, 47b, 3575-3581 https://doi.org/10.1007/s11663-016-0813-8