2018 №06 (04) |
DOI of Article 10.15407/tpwj2018.06.05 |
2018 №06 (06) |
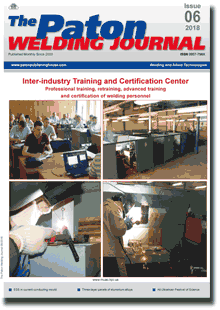
The Paton Welding Journal, 2018, #6, 32-39 pages
Modern methods of manufacturing three-layer panels of aluminium alloys (Review)
Yu.V. Falchenko and L.V. Petrushinets
E.O. Paton Electric Welding Institute of the NAS of Ukraine 11 Kazimir Malevich Str., 03150, Kyiv, Ukraine. E-mail: office@paton.kiev.ua
Three-layer panels with periodic cellular core from aluminium alloys are promising for application in aerospace products, ground and water transportation. The uniqueness of the three-layer panel design consists in that they are characterized by high values of strength and rigidity at a relatively small mass. The work deals with the main types of three-layer panels, design features of manufacturing the cores, methods to join the honeycomb core strips to each other, as well as the three-layer panel elements into one structure. The objective of the presented review is analysis of modern methods of manufacturing three-layer panels from aluminium alloys. Analysis of published data showed that such methods of joining the three-layer panel elements as adhesive bonding and brazing became the most widely applied. Their main disadvantage, however, is increase of the structure mass due to application of an adhesive or braze alloy. Application of diffusion welding with manufacture of honeycomb core from a stronger titanium alloy for joining three-layer panels or application of a specialized fixture, which allows limiting the degree of plastic deformation of the structure, are promising for welding three-layer panels. 28 Ref., 1 Table, 9 Figures.
Keywords: aluminium alloys, three-layer panels, core, adhesive bonding, brazing, welding
Received: 25.04.18
Published: 05.07.18
References
- Paik, J.K., Thaymballi, A.K., Kim, G.S. (1999) The strength characteristics of aluminum honeycomb sandwich panels. Thin-Walled Structures, 35, 205–231. https://doi.org/10.1016/S0263-8231(99)00026-9
- Panin, V.F., Gladkov, Yu.A. (1991) Structures with filler material: Refer. book. Moscow, Mashinostroenie [in Russian].
- Amraei, M., Shahravi, M., Noori, Z. et al. (2013) Application of aluminium honeycomb sandwich panel as an energy absorber of high-speed train nose. of Composite Materials, 48(9), 1027–1037.
- Khertel G. (1965) Thin-walled structures (structural elements, determination of accurate sizes and design in aircraft construction and other engineering fields). Moscow, Mashinostroenie [in Russian].
- Slivinsky, V.I., Tkachenko, G.V., Slivinsky, M.V. (2005) Efficiency of application of honeycomb structures in flying vehicles. Vestnik Sib. Aerokosmich. Un-ta im. Akad. M.F. Reshetnyova, 4, 169–173 [in Russian].
- Kindinger, J. (2001) Lightweight structural cores. ASM Handbook, Vol. 21: Composites, 3, 180–183.
- Haydn N.G.Wadleya, Norman, A. Fleckb, Anthony G. Evans (2003) Fabrication and structural performance of periodic cellular metal sandwich structures. Composite Sci. and Technology, 63, 2331–2343. https://doi.org/10.1016/S0266-3538(03)00266-5
- Lukina, N.F., Anikhovskaya, L.I., Dementieva, L.A. et al. (2007) Adhesives and adhesive materials for items of aircraft engineering. Proizvodstvo, 5, 19–27 [in Russian].
- Khan, S., Loken H.Y. (2007) Bonding of sandwich structures — the facesheet/honeycomb interface — a phenomenological study. In: of SAMPE 2007 (Baltimore, June 2007), 1–9.
- Yi-Ming Jen, Li-Yen Chang (2009) Effect of thickness of face sheet on the bending fatigue strength of aluminum honeycomb sandwich beams. Engineering Failure Analysis, 16, 1282–1293. https://doi.org/10.1016/j.engfailanal.2008.08.004
- Yi-Ming Jen, Chin-Wei Ko, Hong-Bin Lin (2009) Effect of the amount of adhesive on the bending fatigue strength of adhesively bonded aluminum honeycomb sandwich beams. J. of Fatigue. 31, 455–462. https://doi.org/10.1016/j.ijfatigue.2008.07.008
- Shuliang Cheng, Xuya Zhao, Yajun Xin et al. (2015) Experimental study on shear property of integrated sandwich panel of aluminum honeycomb and epoxy resin. The Open Mechanical Engin. J., 9, 1000–1006.
- Nikitinsky, A.M. (1983) Brazing of aluminium and its alloys. Moscow, Mashinostroenie [in Russian].
- Sporer, D., Fortuna, D. (2014) Selecting materials for brazing a honeycomb in turbine engines. Welding J., 93(2), 44–48.
- Kumagai, M. (2003) Recent technological developments in welding of aluminium and its alloys. Welding Int., 17(3), 173–181. https://doi.org/10.1533/wint.2003.3074
- Gregory, W. Kooistra,Vikram, S. Deshpande, Haydn N.G. Wadley (2004) Compressive behavior of age hardenable tetrahedral lattice truss structures made from aluminium. Acta Materialia, 52, 4229–4237. https://doi.org/10.1016/j.actamat.2004.05.039
- Ding Min, Zhang Pei-lei, Zhang Zhen-Yu et al. (2010) A novel assembly technology of aluminum alloy honeycomb structure. J. Adv. Manuf. Technol., 46, 1253–1258. https://doi.org/10.1007/s00170-009-2173-x
- Ferraris, S., Volpone, L.M. (2005) Aluminum alloys in third millennium shipbuilding: Materials, technologies, perspectives. In: of 5th Int. Forum on Aluminium Ships (Tokyo, Japan, 11–13 October 2005), 1–11.
- Levin, Yu.Yu., Erofeev, V.A. (2008) Calculation of parameters of pulsed laser welding of thin aluminium alloys. Proizvodstvo, 4, 20–24 [in Russian].
- Kozakov, N.F. (1968) Diffusion welding in vacuum. Moscow, Mashinostroenie [in Russian]. Gurevich, S.M. (1990) Reference book on welding. Kiev, Naukova Dumka [in Russian].
- Sergeev, A.V. (1990) Diffusion welding of aluminium alloys. In: Achievements and perspectives of development of diffusion welding. Moscow, 48–54 [in Russian].
- Chudin, V.N., Timokhov, A.P., Terentiev, M.M. et al. (1992) Diffusion welding of hollow structures of high-strength aluminium alloy sheets. Proizvodstvo, 10, 5–7.
- Falchenko, Yu.V., Ustinov, A.I., Petrushynets, L.V. et al. (2017) Device for diffusion welding of three-layer honeycomb panels. 113424 Ukraine, Int. Cl. B23K 20/00, B23K 20/14 [in Ukrainian].